Guide to Quality Management Systems (QMS)
01. What is a Quality Management System?
A Quality Management System (QMS) is a set of well-defined and executed business processes that cover every aspect of how a business develops and delivers and supports world-class products and services. Organizations may have anywhere from a handful to hundreds of critical business processes that interact with each other.
A QMS is a mechanism for ensuring that processes are documented, employees are trained, and records are maintained. Business processes must be documented using Procedures and supported by Work Instructions and Forms. Employees must be trained to perform these business processes. And records must be maintained to prove that each business process was executed as described in the relevant procedure.
A well-designed and executed QMS will help a company deliver world-class products and services.
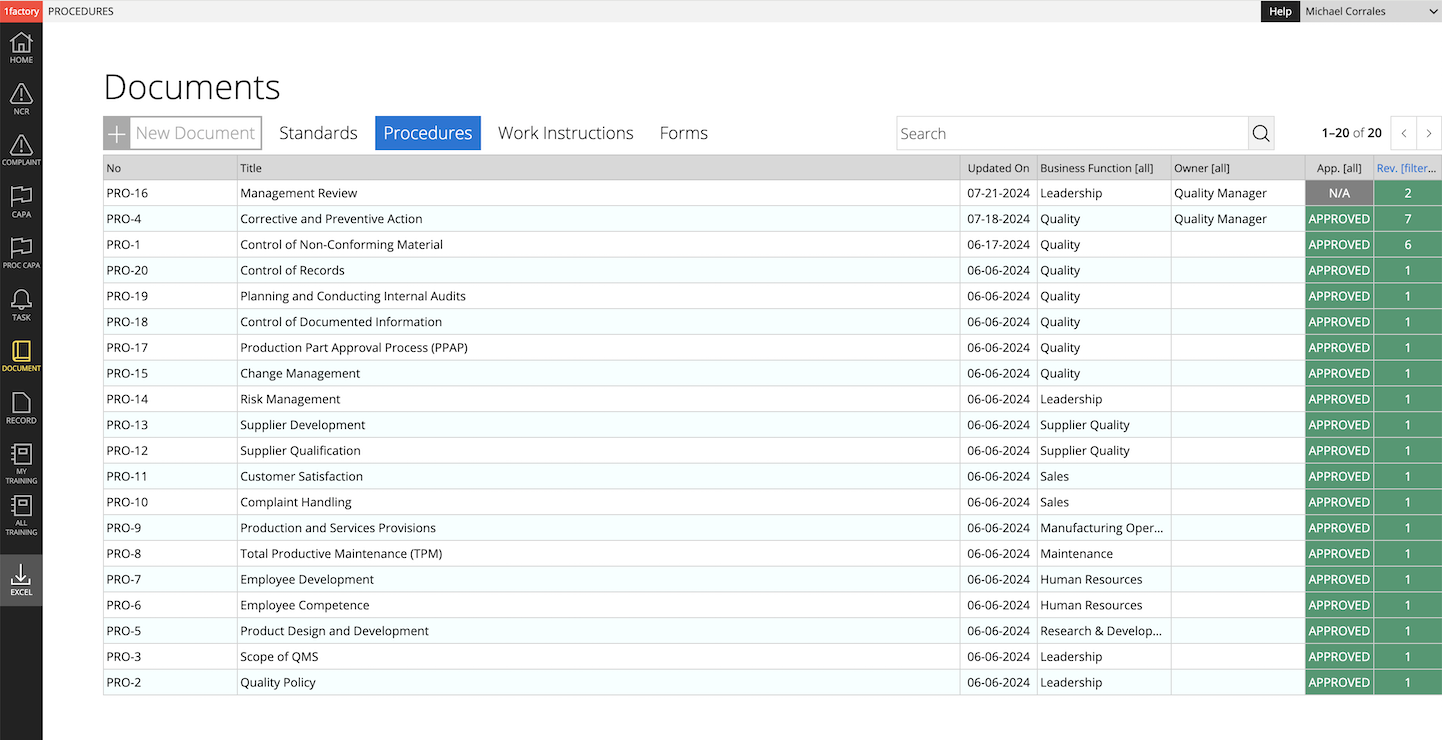
02. The Role of Business Processes
What is a business process? A business process is a set of actions by which a business completes a unit of work.
As an example, a small deli needs to ensure that it has sufficient inventory of ingredients - the breads, the vegetables, and the meats - stocked and ready to use at the beginning of each day. The actions it takes to monitor inventory and reorder stock when needed, makes up the inventory management business process. Business processes may be further broken down into smaller processes. For example, companies have processes for determining the level of inventory at which ingredients need to be reordered, for monitoring freshness and shelf-life of ingredients and so on.
Each business process must be clearly documented - with inputs, outputs and resources - and must have defined responsibilities and metrics for success (e.g. inventory accuracy must be >99.9%).
IMPORTANT: All Quality Management Systems and all standards (e.g. ISO 9001, ISO13485, AS9100, TS16949 etc.) emphasize the role of business processes. And they focus on business processes, because defects are caused by deficiencies or failure to follow business processes.
04. Example: A Coffee Shop
Let's start in a coffee shop - one of the most transparent businesses you can observe and experience - and understand what processes may be involved in delivering a great cup of coffee. This customer experience in a coffee shop is a combination of the cafe's environment, order accuracy, wait time, and the attributes of the coffee including its taste, aroma, temperature and consistency. The wait time and cafe environment - the seating, lighting, and noise-levels - can make or break the experience, but for now we'll focus on just the order-to-delivery process and the taste of the coffee. Here's a partial list of the business processes in a coffee shop.
We've all had days when our coffee orders were messed up. This happens more often than we like, and even happens to us at our favorite coffee shops!
If you look at the various business processes (see image) - from order-entry to delivery - to see where things could go wrong for your coffee order, you can see that your order can be messed up for many different reasons:
- You got the wrong drink
- Your order was written incorrectly by the cashier
- The barista made the wrong drink
- The barista missed an important ingredient
- Your coffee was over-brewed and tastes burnt.
To prevent these defects from occurring, the quality management system (QMS) for a coffee-shop would ensure these processes are documented, employees are trained, and records are maintained for verification.

06. Example: A Make-to-Order Manufacturer
And just like in a coffee shop, in the modern manufacturing environment, all the business processes - from order entry through product inspection and test and eventual customer support - need to be executed flawlessly by employees to eventually ship defect-free products.
Let's take for example a make-to-order machinery manufacturer in the semiconductor equipment industry. The order may be messed up for many different reasons
- The wrong configuration was built and shipped
- One of the components does not work
- One of the components is out of spec
- Labels are applied incorrectly ro are in the wrong language
- There was shipping-related damage
- The machine does not function as expected
- The machine was not installed or started-up correctly
To prevent these defects from occurring, the quality management system (QMS) for a manufacturer would ensure these processes are documented, employees are trained, and records are maintained for verification.
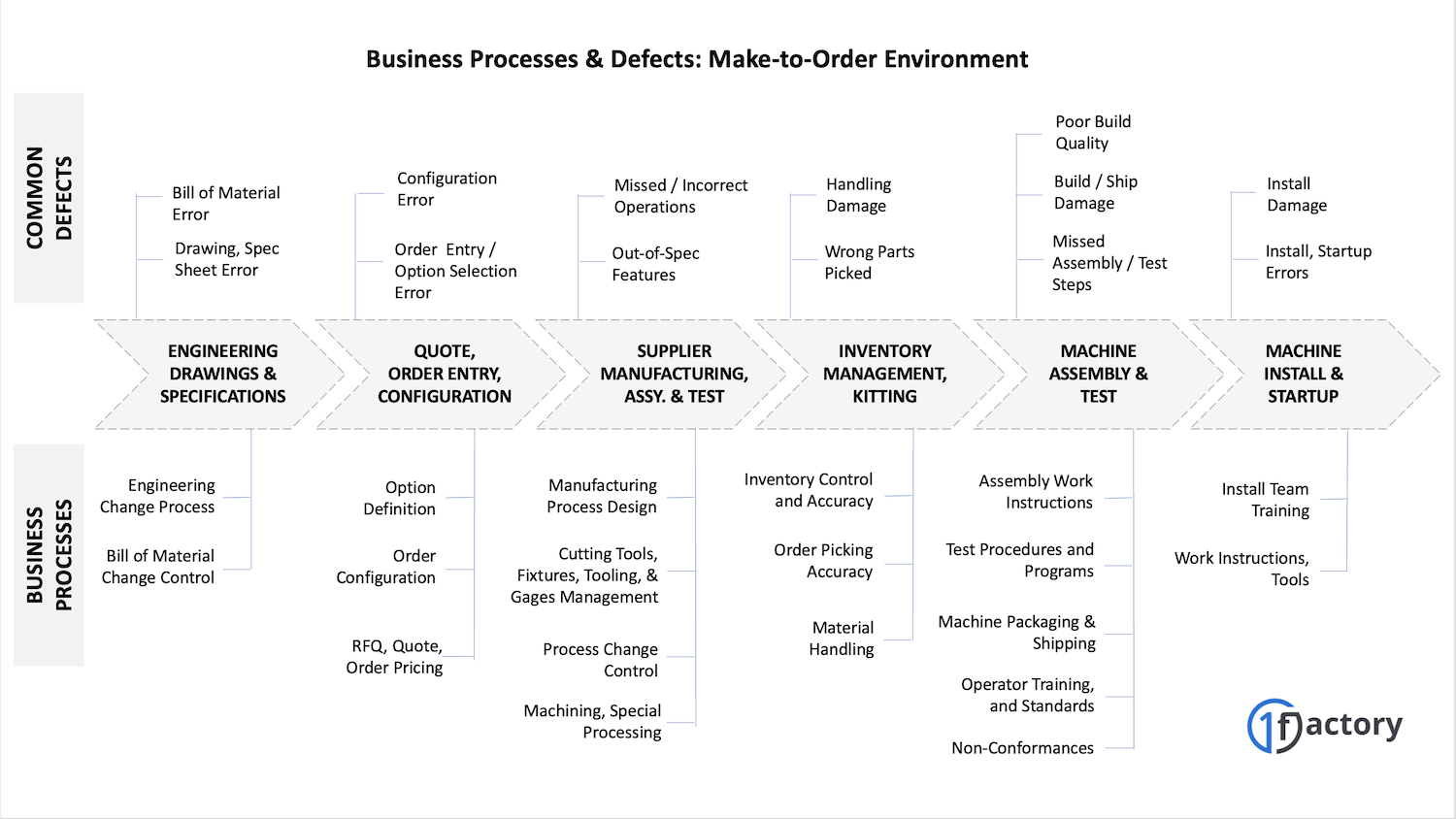
07. Essential QMS Elements
There are five essential elements to a QMS
- Document Control
- Process Management
- Training Management
- Audits
A QMS is not always a single software system. Instead, a QMS is typically a combination of software systems. For example, the business process for purchasing raw materials and the associated training for the purchasing process may be documented in a Doc Control system, while the purchasing process itself may be operated entirely in the ERP system and it's records may therefore reside in the ERP system.
08. Document Control
Document control forms the foundation of a QMS by ensuring that all quality-related documentation is properly managed throughout its lifecycle. This element encompasses the creation, review, approval, distribution, and revision of all quality documents. A robust document control system prevents the use of obsolete procedures, maintains version history, and ensures that only authorized personnel can access and modify documents. It typically includes a centralized repository where current versions are easily accessible while maintaining a complete audit trail of changes.
Key Components:
- Centralized document management system
- Version control and revision tracking
- Access control based on roles
- Clear approval workflows
- Training record management
09. Process Management
Process management involves identifying, documenting, and optimizing the interconnected processes that make up an organization's operations. This element ensures that processes are standardized, efficient, and aligned with quality objectives. It requires regular monitoring of process performance through metrics and continuous improvement initiatives. Process management helps organizations identify bottlenecks, reduce waste, and maintain consistent quality outputs.
Key Components:
- Process documentation and mapping
- Interaction between processes
- Performance metrics and monitoring
- Continuous improvement mechanisms
- Risk assessment and mitigation
10. Training Management
Training management ensures that all personnel have the necessary knowledge and skills to perform their roles effectively and in compliance with quality requirements. This element involves identifying training needs, developing training programs, and maintaining records of completed training. It's crucial for maintaining workforce competency and ensuring that changes to procedures are effectively communicated and implemented.
Key Components:
- Role-based training requirements
- Training tracking and documentation
- Retraining triggers for procedure updates
- Competency verification
- New hire onboarding processes
11. Audit Management
Audit management provides systematic evaluation of the QMS to verify its effectiveness and compliance with requirements. This element includes planning and conducting both internal and external audits, documenting findings, and implementing corrective actions. Regular audits help organizations identify gaps in their quality system, ensure regulatory compliance, and drive continuous improvement.
12. QMS Document Hierarchy
The QMS documentation structure follows a hierarchical approach, with each level building upon and supporting the others, building a cohesive system where:
- Standards define requirements
- Quality Manual establishes the framework
- Procedures outline processes
- Work Instructions detail specific tasks
- Forms capture required information
- Records demonstrate compliance and effectiveness
13. Standards
Standards form the apex of the documentation hierarchy, establishing the fundamental requirements that organizations must meet. These include ISO 9001, industry-specific standards (like ISO 13485 for medical devices), and regulatory requirements. Standards provide the framework for developing and implementing the entire quality management system.
14. Quality Manual
The Quality Manual is the cornerstone document that defines the organization's quality management system. It outlines:
- The scope of the QMS
- Quality policy and objectives
- Organization's context and interested parties
- Process interactions and relationships
- Key responsibilities and authorities
- References to supporting procedures
15. Procedures
Procedures describe the systematic methods for carrying out key processes. They answer the "who, what, when, where, and why" of activities, ensuring consistency across the organization. Procedures typically include:
- Purpose and scope
- Responsibilities
- Detailed process steps
- Related documentation
- Quality controls and metrics
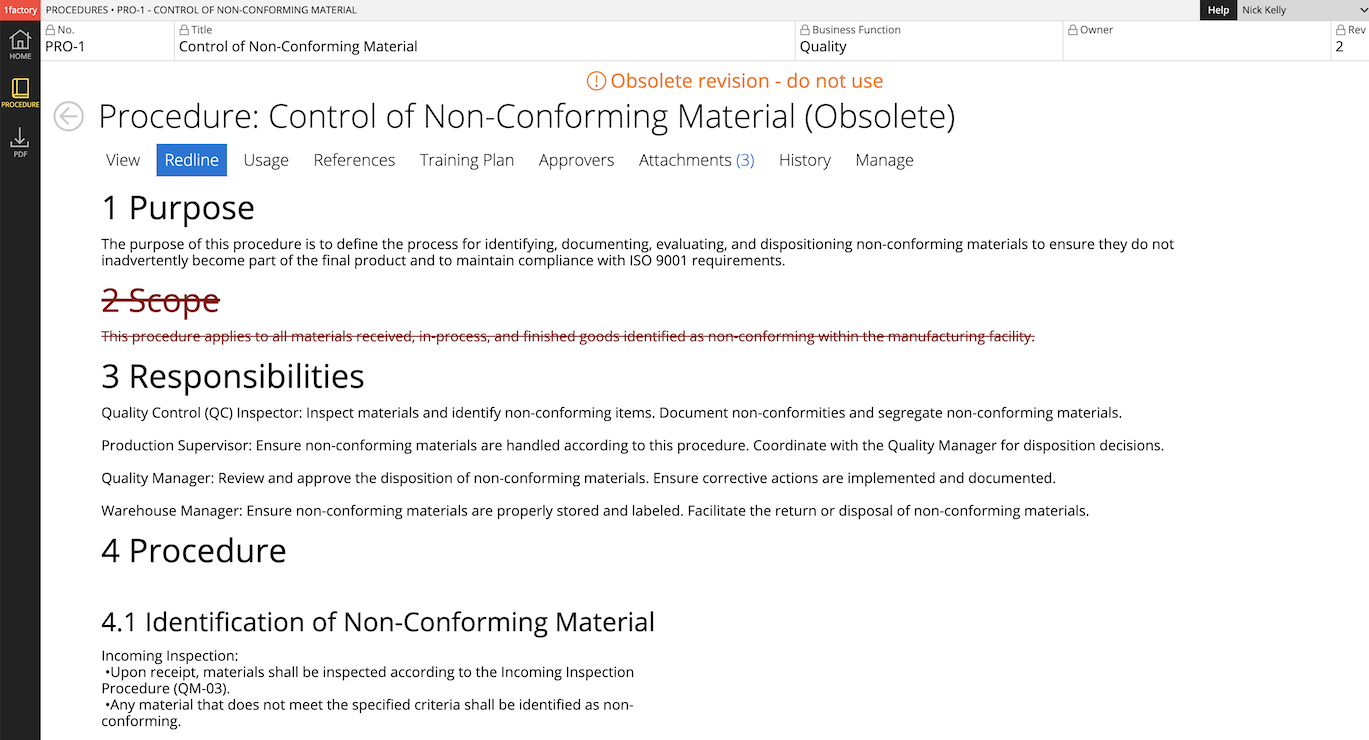
16. Work Instructions
Work Instructions provide detailed, step-by-step guidance for specific tasks within procedures. They focus on the "how" of individual activities and often include:
- Detailed steps for task completion
- Visual aids and diagrams
- Critical parameters and specifications
- Safety considerations
- Quality checkpoints
17. Forms
Forms are standardized templates used to capture data and information required by procedures and work instructions. They ensure consistent data collection and documentation across the organization. Forms become records once completed.
18. Records
Records provide evidence of activities performed and results achieved. They demonstrate compliance with requirements and effectiveness of the QMS. Records typically include completed forms for things like:
- Inspection and Test Records
- Nonconformances
- Training documentation
- Audit findings
- Engineering Change Orders
19. Training Management
Employees must be trained to successfully execute business processes. Training may be required under various conditions:
- Initial Training: When the employee is hired and onboarded
- Role Change: When the employee moves jobs (for example, the employee may move from an inventory management job to a cashier job)
- Procedure Initial Release: When a new procedure is released
- Procedure Revision: When an existing procedure is revised or updated.
- Corrective Action: Additional employee training may also be required as part of a Corrective Action
Training must be documented and where possible evaluated via a test (e.g. a quiz with questions regarding the nonconformance process) or via a demonstration of capabilities (e.g. for welding) or via peer assessment.