1factory Case Studies
rms (a Cretex Medical Company)
As John Braun (President, rms Company) says, "Quality is paramount at rms."
rms is a leader in medical device manufacturing for the Interventional, Cardiac Rhythm Management, and Orthopedic markets.
When rms set out to replace their legacy systems, they sought a partner capable of meeting their challenging requirements, along with ease of implementation, ease of use, and scalability.
In just one year, rms successfully deployed 1factory for: 4 manufacturing sites, 900+ machine-tools, 1300 users and 100+ CMM / vision systems.
rms created 21,000+ Inspection Plans, inspected over 70,000+ Lots, recorded 12 million+ Data Points and consolidated 6 QC systems into one.
Watch a 4-minute video to hear first-hand experiences from the cross-functional rms team: Machinists, Quality Engineers, Quality Managers, Project Manager and President.
Avalign Technologies
"There are thousands of software suppliers to select from. And during the sales cycle you often find that the relationship is terrific, but then it falls apart very quickly after you sign the contract. With 1factory, they stayed with us every step of the way, and they continue to partner with us into our future." Robin H., CIO
Avalign Technologies is an industry leader in the design and manufacturing of high-precision implants and instruments for orthopedic, spine, and trauma applications.
The Challenge: Avalign needed a comprehensive Quality Control solution that delivered: Robust capabilities, Enterprise-grade security, Seamless scalability, Intuitive user experience, and Initial and on-going validation
Watch a 4-minute video to hear first-hand from the Avalign team about their experience with 1factory.
Ultra Machining Company
Ultra Machining Company (UMC) is a manufacturer of high-precision components for medical device, aerospace, and defense applications. The products are complex, with 100 — 800 features per product.
With 1factory, UMC successfully consolidated 5 separate QC systems into 1. Today, data is automatically uploaded from 20 CMMs and 8 VCMMs, 24 hours a day. Over 1 million measurements are recorded in 1factory each month. Auto-ballooning speeds up FAI creation. And hours are saved from each PPAP package creation.
Watch a 4-minute video to hear first-hand experiences from the cross-functional UMC team: Machinists, Quality Engineers, Director of Quality, VP of IT, and VP of Operations.
And read the Modern Machine Shop Feature on 1factory's work with UMC.
Zipline
Zipline designs, manufactures and operates the world's largest autonomous delivery system, delivering life-saving supplies such as blood and medicines, and cutting delivery time from hours to minutes.
High-quality parts are critical to successful and reliable delivery. To ensure the quality of parts coming in from suppliers, Zipline deployed the 1factory system across its supply chain. Today suppliers create Control Plans and First Articles and submit them to Zipline for review and approval via 1factory. Once Plans and FAIs are reviewed, suppliers submit on-going inspection data to Zipline via 1factory.
Watch a 7-minute video to hear first-hand from the Zipline team (Incoming Inspection, Quality Engineering, Supplier Quality, and Chief Technology Officer) about the power of 1factory, its ease-of-use, its impact on cost of quality, and why 1factory is the best SaaS software Zipline uses.
Next Intent - Manufacturing Quality
"The Software worked just like the demo!" Rodney B. President & CEO.
Next Intent is a world-class precision manufacturer, serving the space, defense, aerospace and semiconductor industries. The parts they craft are critical to the success of billion-dollar, multi-decade missions — where a single failure isn't just costly, it's catastrophic.
Notable projects include components for THREE Mars missions, and the revolutionary Red Camera Assembly for the Giant Magellan Telescope and more.
Next Intent picked 1factory to meet its challenging quality requirements. With 1factory, Next intent has unified quality planning, inspections, gage managements, and quality records into one seamless ecosystem, automating paperwork, eliminating errors, and helping deliver the highest quality parts to customers.
"We were going to go with another company's software. The implementation time was nine months. That was too long. With 1factory, they were getting it to work within the first day. Within twenty minutes, I had bubble-printed the plans and inspection sheets".
Allegheny Performance Plastics
Allegheny Performance Plastics manufactures advanced parts and assemblies from high-performance polymers for the space, aerospace, defense, and transportation industries.
Allegheny made the switch to 1factory and saw immediate benefits, including the ability to see SPC data in real time versus days later after bulk uploading in the old systems. Since adopting the software, the company says the biggest savings in time and resources have come from ending manual transposing and navigating multiple systems to retrieve quality information.
Allegheny's customers are able to view a live feed of their jobs via 1factory's Deep Collaboration feature, including all SPC and process capability calculations. This level of transparency is unprecedented and has helped their build customers' confidence in their capabilities.
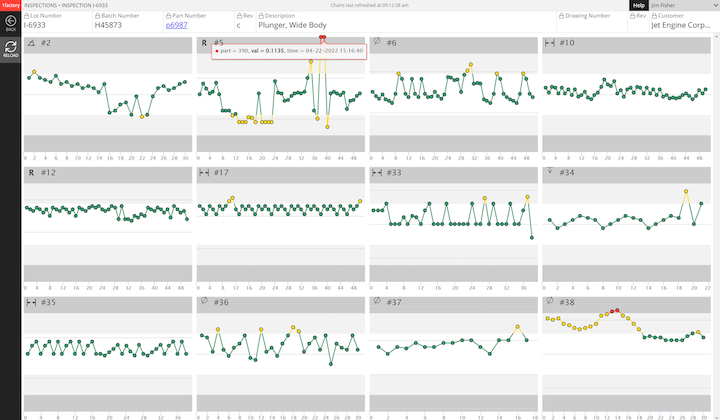
Eskridge Inc
Eskridge Inc designs and manufactures application-specific gear drives for aerospace, farming, energy, marine, industrial, and other applications.
Eskridge has to ensure quality for nearly 900 different Gear Drive component made in-house and 500 components from across their supply chain.
With 1factory, Eskridge was able to communicate requirements to operators, ensure data was being collected, and was able to significantly reduce scrap and rework.
Read the full case-study along with the Eskridge team's insights into how consistent quality gives them a competitive edge.
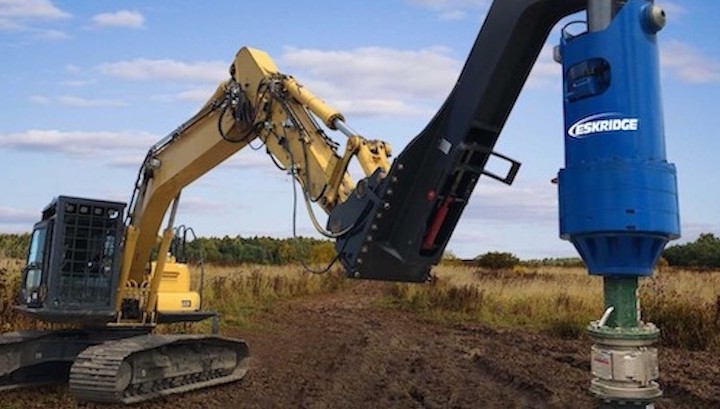
Fairview Machine
Fairview Machine is a manufacturer or high precision Aerospace and Medical components. Fairview Machine deployed the 1factory quality control and quality management (QMS) system and digitized their QC processes.
Harrison Moulton, Quality Manager at Fairview Machine Company, says:
"Within the first week, our machinists began to come into the quality department asking when their (inspection) jobs would be running with 1factory."
"I would 100% recommend the transition to 1Factory's QMS. It has helped Fairview go completely paperless over the past 3 years while helping us maintain exceptional traceability across the board."
Read the full case-study to learn how Fairview Machine transitioned the entire organization from a paper-based quality system to a paperless one.
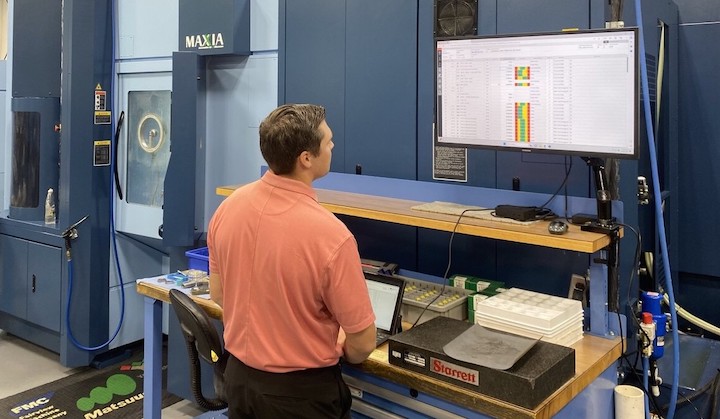
Orbit Irrigation
Orbit Irrigation (Husqvarna Group) is the world's largest manufacturer of sprinkler heads, smart timers, valves, manifolds, and other accessories for residential, agricultural, and commercial irrigation systems. These complex assemblies contain dozens to hundreds of mechanical and electrical components sourced from suppliers around the globe.
With 1factory, Orbit Irrigation was able to move away from paper and excel to digital inspection planning, data collection, and analysis. Once 1factory was selected, the results were practically immediate. "The time savings and reporting accuracy just went through the roof with 1factory, and so many of my tasks have been simplified," says Robin Bushman, Quality Manager at Orbit Irrigation.

Able Tool Corporation
"1factory has been a game changer for us" - Paul Hayes, President Able Tool Corporation
The 1factory platform was introduced to Able Tool Corporation by their customer, a Major Aerospace OEM. Using 1factory's Supplier Collaboration Portal, Able Tool was able to create and share plans, FAIs, and ongoing production inspection data directly with their OEM customer.
Within the first week, Able Tool successfully delivered 54 FAIs to their customer and realized significant productivity gains. By the end of the first month, Able Tool had delivered over 200 FAIs and decided to adopt 1factory as their internal Quality Control software, transforming their manufacturing operations.
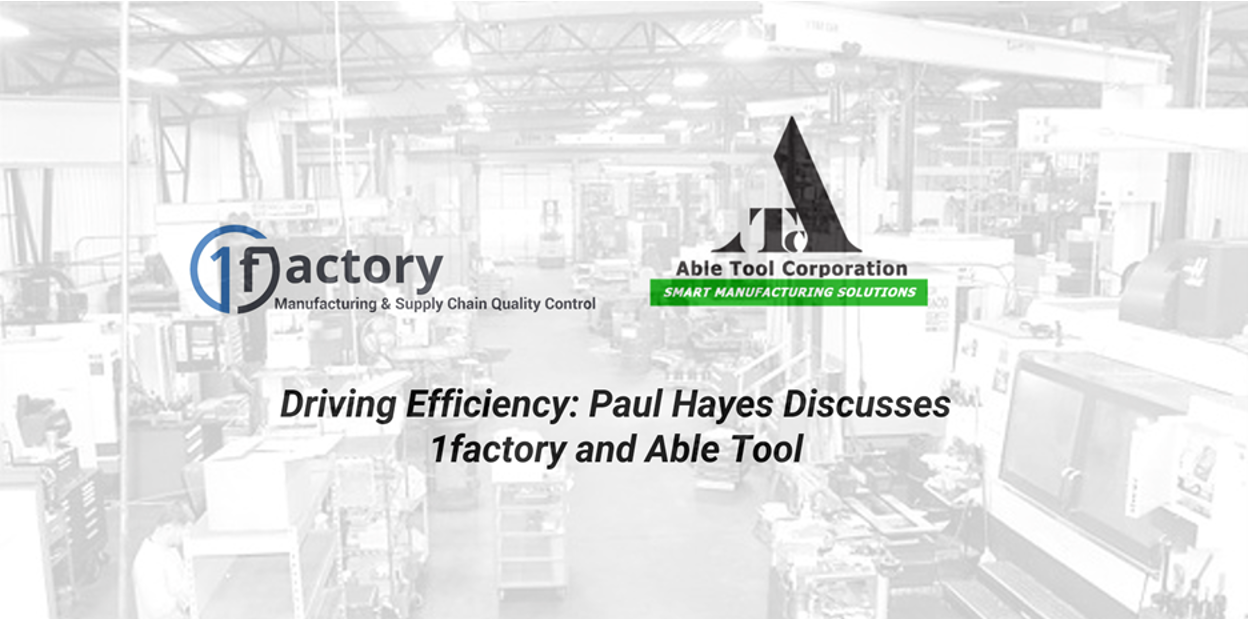
W.H. Bagshaw
W.H. Bagshaw, established in 1870, manufactures CNC precision components for the medical, aerospace, defense, agriculture and other industries
By leveraging 1factory, W.H. Bagshaw has realized significant savings in time, resources, and effort. For instance, conducting capability studies for a customer has led to the adoption of centerless ground material, resulting in reduced setup times and decreased scrap rates. These efficiencies directly contribute to cost savings and improved overall productivity.
They now benefit from cleaner inspection and First Article Inspection (FAI) reports, enhanced visualization of priority jobs for management, and improved reporting capabilities for customer requests.
The ability to provide data-driven charts demonstrating their manufacturing capability has strengthened their relationships with clients.
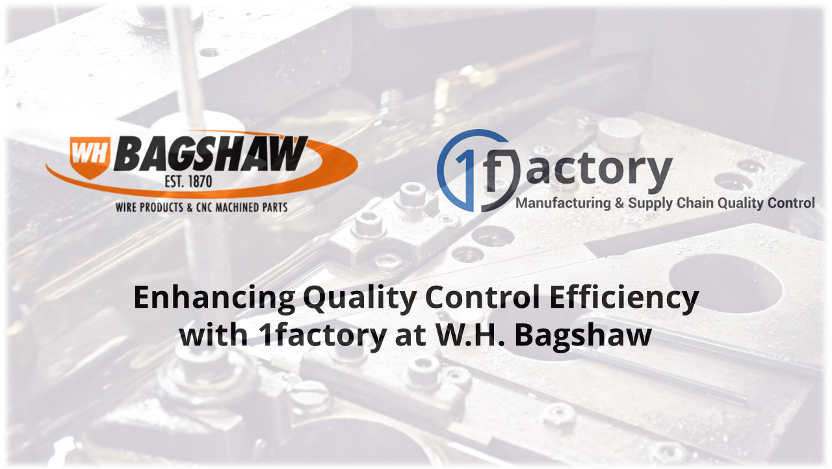
J&L Manufacturing
J&L Manufacturing provides a range of metal forming services (metal cutting, bending, stamping, welding and machining) to the automotive, hospital and other industries.
J&L did not have the manpower to support heavy PPAP documentation requirements and would turn away orders that required PPAPs. Then they found 1factory. And with 1factory, J&L was able to drop PPAP creation time from a week to just two hours.
J&L completed 168 PPAPs in the first 7 months of the year, and averages 5 PPAPs a week. More importantly nearly all PPAPs were delivered 100% accurate and complete in the first pass. They can now accept all the orders coming their way, and can grow their business.
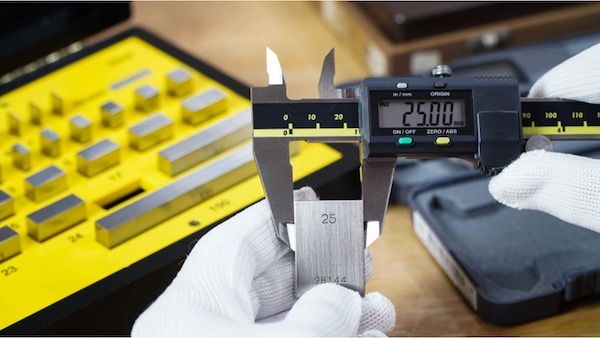
Savage Arms Canada
Savage Arms Canada, located in Lakefield, Ontario, is a leading firearms manufacturer known for producing high-quality rifles, shotguns, and accessories.
Quality Manager, Arron McChesney says "1factory has streamlined our PPAP process by automating the administrative tasks involved with documentation, speeding up submissions and approvals."
"With its automated data validation and centralized document management, 1factory ensures that all our information is accurate and up to date. The platform is designed to handle large volumes of data and complex processes, making it suitable for manufacturers of all sizes."
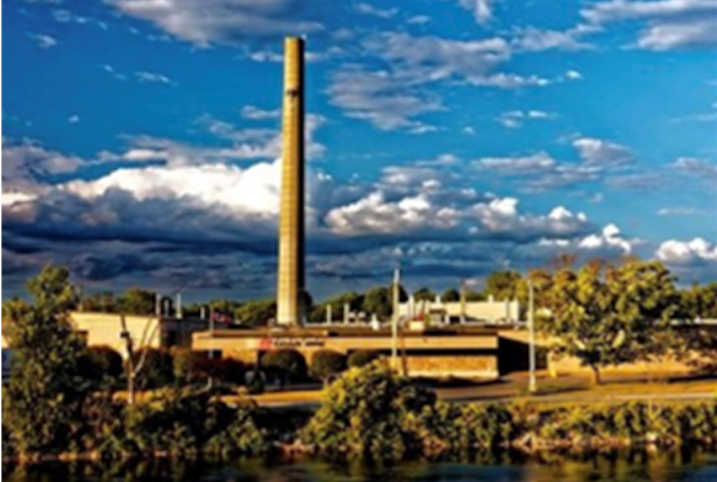