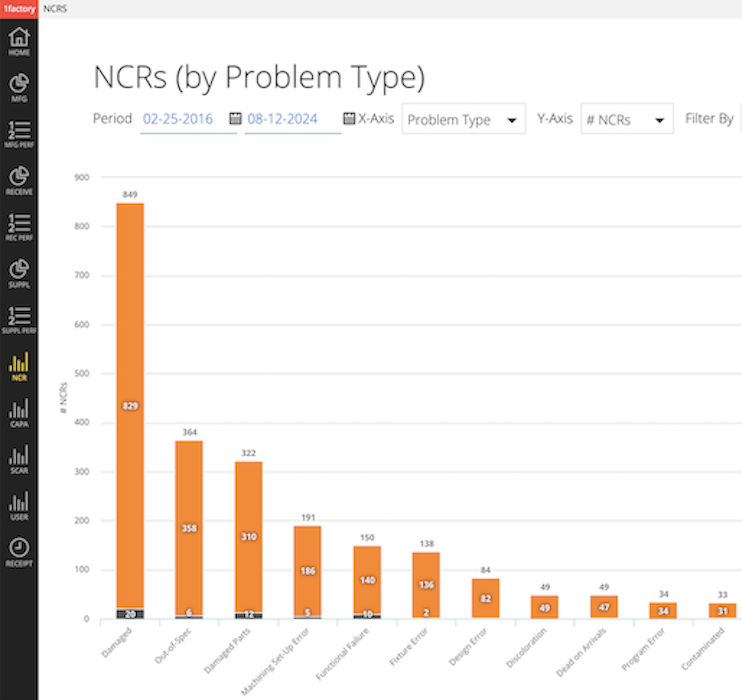
Powerful, Easy-to-Use, Lightning-Fast
NCR, CAPA, SCAR and Complaint Management Software.
Easily record, manage, and analyze Nonconformance Reports (NCRs), Corrective & Preventive Action Reports (CAPAs), Supplier Corrective Action Reports (SCARs), and Customer Complaints. Assign Tasks. Track status and ensure timely completion.
RESOLVE ISSUES QUICKLY. ANALYZE TRENDS. PREVENT RECURRENCE.
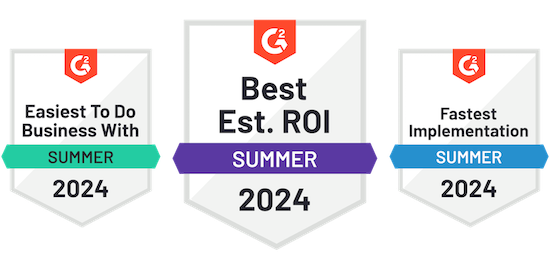
SIMPLE YET ELEGANT APPROACH TO QUALITY
“The software is easy to use and learn. I have been in the Quality Assurance world for quite some time now and find that both new and seasoned persons would appreciate the simplistic, yet elegant, approach to quality. The simplistic way that it produces reporting is a great and useful tool for anyone looking to gain or maintain compliance with regulatory bodies (ISO/AS/IATF) as well as keeping customer satisfaction high with quick reporting/number assisgnments to CAPA/8D reports.”
G. Mejia, Camisasca Automotive
KEY ISSUE MANAGEMENT FEATURES
1 Nonconformances (NCRs,)
Easily create and manage nonconformances for manufacturing or engineering caused defects, deviations, customer returns, audit findings, safety problems etc. Autopopulate NCR details from Inspections. Assign action-items, and use automated reminders to ensure timely resolution.
2 Corrective Actions (CAPA, SCARS)
Initiate CAPAs and SCARs from NCRs. Setup CAPA templates to guide the user, and ensure a consistent problem-solving process. Track CAPA and SCAR progress, and use automatic reminders to ensure timely resolution. Review and Approve.
3 Supplier Corrective Actions (SCARs)
Request Corrective Actions from suppliers using the 8D process. Work together with suppliers to resolve problems and prevent recurrence. Ensure all 8D sections are filled-out, supplier actions are completed and effectiveness is verified prior to closing out the corrective action.
4 Complaints
Record and track product failures or deficiencies reported by field service teams and customers. Track reported issues from initial complaint through Investigation (Review of Device /Lot History Record, Failure Analysis), Risk Assessment, Containment, Corrective Action, and Preventive Action. Assign and track actions
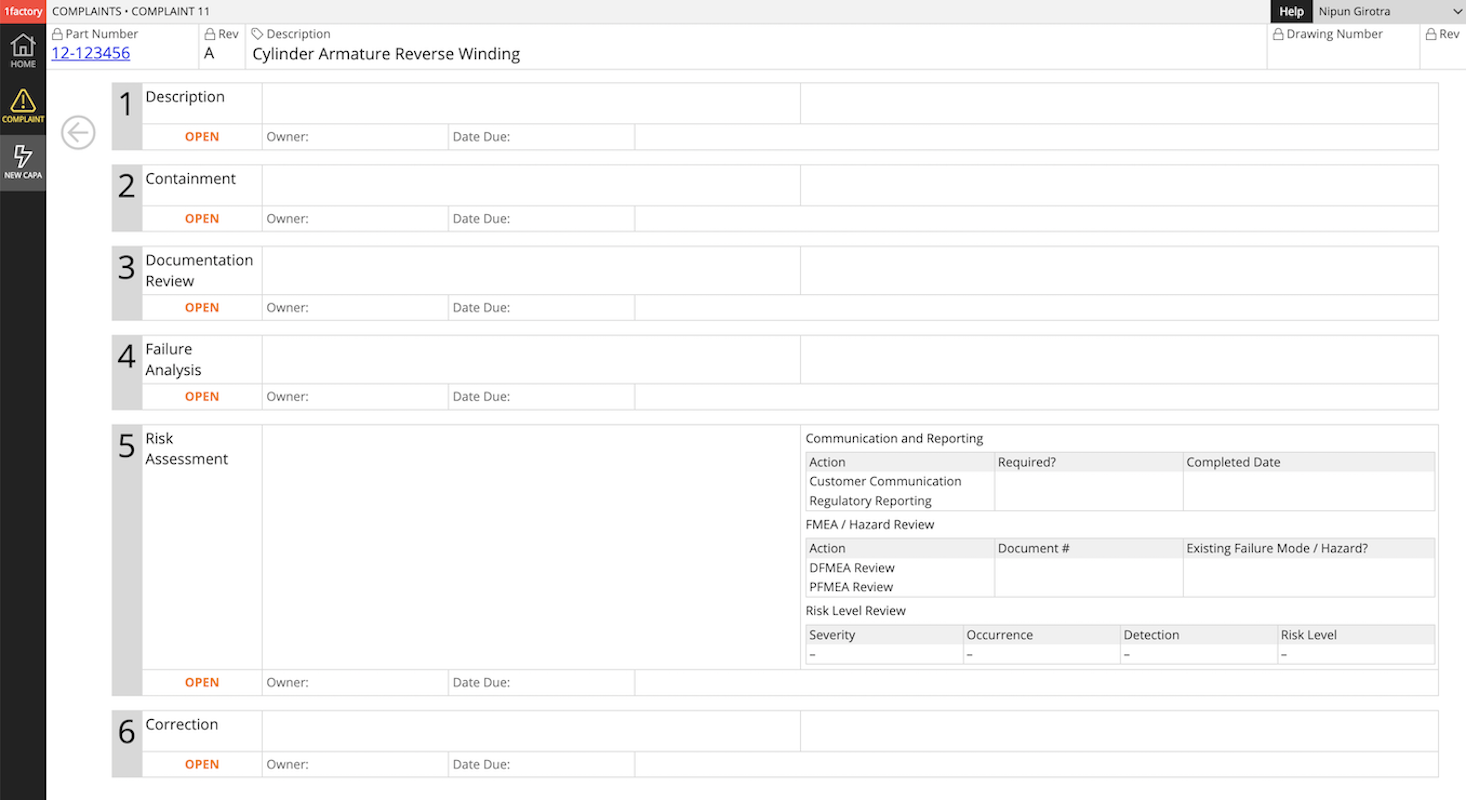
5 Audit Findings
Manage audit findings and associated tasks. Ensure compliance and readiness for customer or regulatory audits. Support a continuous improvement culture by enabling team-members to log and track business process improvement actions.
6 Task Management
Assign tasks with due-dates at any point in a non-conformance (NCR) or CAPA process for investigation, correction, containment, rework and other actions. Automate reminders and follow-ups to ensure tasks are completed.
7 Real Time Analytics
Instantly analyze non-conformances, CAPAs, SCARs, Complaints etc. with built-in lightning-fast analytics without expensive 3rd-party BI tools. Pareto and trend data by Part Number, Customer, Supplier, Defect Code, Root Cause. Quickly identify and resolve problems.
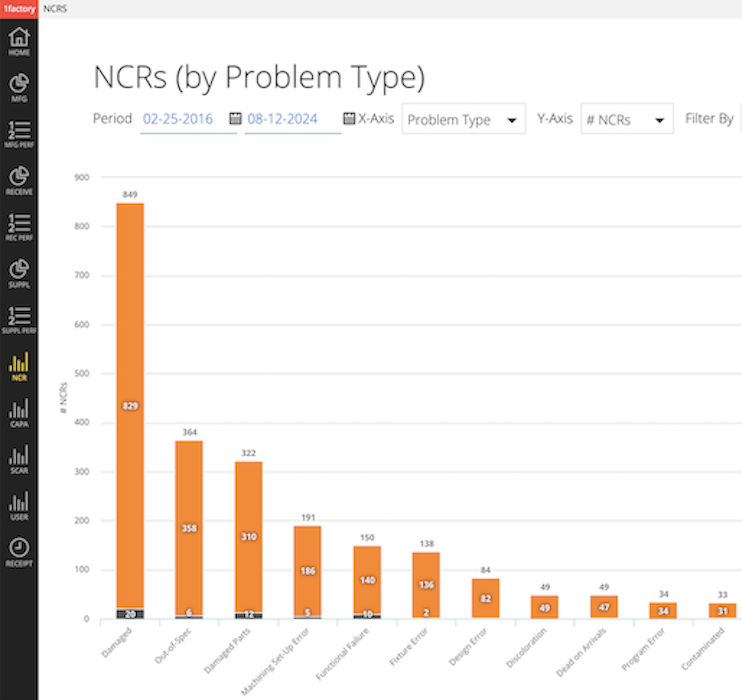
CASE STUDIES
Ultra Machining Company (UMC)- Manufacturing QC
UMC is a manufacturer of high-precision components for medical device, aerospace, and defense applications. The products are complex, with 100 — 800 features per product.
With 1factory, UMC successfully consolidated 5 separate QC systems into 1. Today, data is automatically uploaded from 20 CMMs and 8 VCMMs, 24 hours a day. Over 1 million measurements are recorded in 1factory each month. Auto-ballooning speeds up FAI creation. And hours are saved from each PPAP package creation.
Watch a 4-minute video to hear first-hand experiences from the cross-functional UMC team: Machinists, Quality Engineers, Director of Quality, VP of IT, and VP of Operations.
EASY TO USE. LIGHTNING FAST.
INTUITIVE DESIGN
1factory is designed for the front-line of quality control with design inputs and ideas from our users. 1factory's intuitive navigation and best-in-class screen-designs make training a breeze. Training and full-deployment takes under two hours with no disruption to operations.
LIGHTNING FAST SPEED
1factory is engineered to be lightning-fast. We serve customers all over the world 24 hours a day, 7 seven days a week, 365 days a year. Our customers in United States, Mexico, Canada, Israel, China, South Africa, Denmark, UK, India, Malaysia, Taiwan all enjoy lightning-fast data collection and powerful real-time analytics.
SECURE AND RELIABLE
SECURITY
1factory is hosted on AWS GovCloud. The AWS GovCloud service is an isolated Amazon region designed to host sensitive data and regulated workloads, including International Traffic in Arms Regulations (ITAR) data.
All customer data transfer from client to server is encrypted over standard HTTPS/TLS 1.2, using a certificate with 2048-bit RSA public key / SHA-256 with RSA encryption. All customer data is encrypted at rest. Data (e.g. Part Numbers, Measurements etc.) are stored in an encrypted Amazon RDS instance. Drawings, Raw Material Certificates etc. are stored on encrypted Elastic Block Storage (EBS) volumes. Drawings and other documents may be additionally encrypted with individual encryption keys.
1factory complies with all NIST-800-171 requirements. 1factory also maintains a SOC2 Type 2 certification, and a copy is available upon request.
RELIABILITY
1factory has been engineered to be highly reliable, scalable and available. Over 200 million parts have been inspected with 1factory by customers in 26 countries.
1factory has delivered an uptime of >99.99% over the last 8 years. We use a third-party service to monitor system uptime, and our customers can view our uptime and availability metrics in real time.
1factory backs-up database with a daily snapshot. Files are stored on redundant hard-drives and backed up via daily snapshots.
500+ CUSTOMERS. 30+ COUNTRIES. 20+ INDUSTRIES.
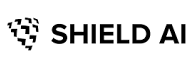
AEROSPACE & DEFENSE

AEROSPACE MACHINING
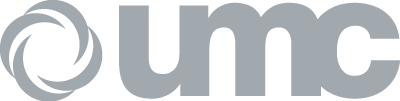
PRECISION MACHINING
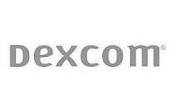
MEDICAL DEVICES
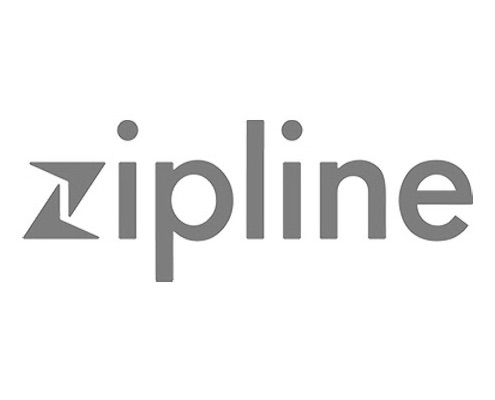
AUTONOMOUS AIRCRAFT
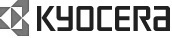
ADVANCED CERAMICS