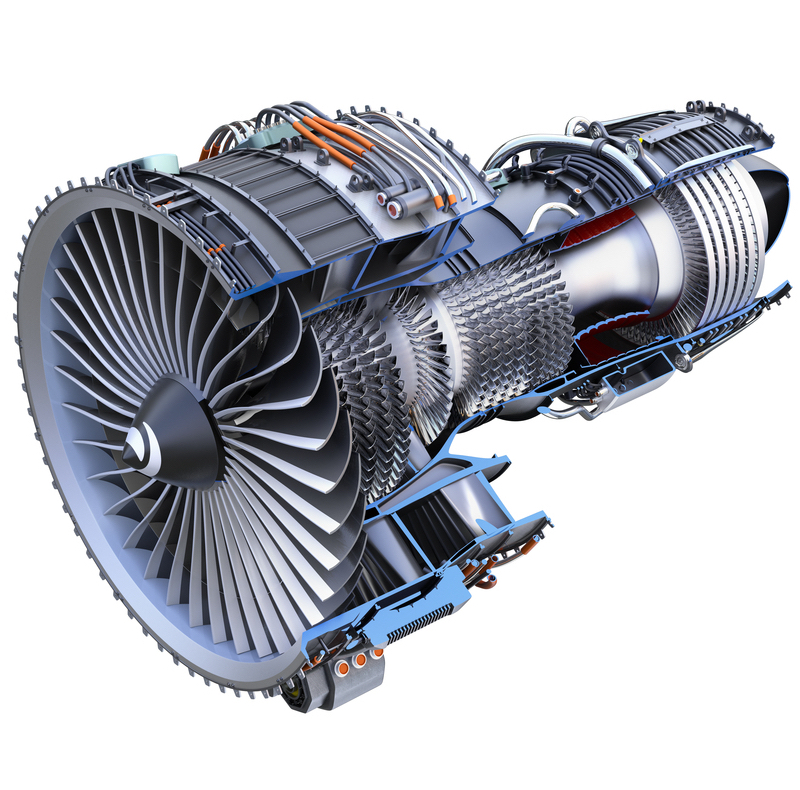
Powerful, Easy-to-Use, Lightning-Fast
Supplier Quality Management Software.
1factory's Supplier Quality Management software connects manufacturers with their suppliers, providing real-time visibility into inspection data from across the supply chain. 1factory speeds up new product introduction (NPI), and simplifies ongoing supply chain quality control.
With 1factory, buyers and suppliers work together seamlessly to ensure quality at source. Both buyer and supplier benefit from reduced risk of defects and cost of poor quality.
ENJOY DEEP SUPPLY CHAIN VISIBILITY. ENSURE QUALITY AT SOURCE.
THE CUSTOMER'S PERSPECTIVE
“1Factory has enabled a different level of integration with our key suppliers on high risk parts. We are solving the problem of stale and dusty control plans, and lack of supplier monitoring of quality data. We also found issues with measurement resolution on key features, and we found other cases where the distribution of data suggests abnormal processing (scrap, rework, fine tuning).”
Semiconductor Capital Equipment Manufacturer
THE SUPPLIER'S PERSPECTIVE
“With 1Factory, we give the customer access to the heart of RIVAL A/S. Everything is available and that gives the customer some security. The system saves us a lot of paperwork because we no longer have to make measurement reports and forward to the customer. We can also keep an eye on unmanned production on the weekends. Otherwise we would be left with over 1000 components all of which would have to be scrapped."
Rival A/S, Denmark
SUPPLIER QUALITY MANAGEMENT FEATURES
1 Approved Vendor List (AVL)
Simplify supplier evaluation and qualification. Manage supplier lifecycle from Onboarding through Approval, and Requalification or Disqualification. Monitor supplier quality and delivery performance. Reduce risk by ensuring supplier certifications are always up-to-date.
2 Incoming Inspections (IQC)
Inspect incoming materials. Capture visual and dimensional checks. Attach raw material & special processing certs. Enjoy automated sample size calculation. Use built-in lot switching rules to tighten or reduce inspection requirements based on historical supplier performance.
3 Supplier Portal
Connect with your suppliers over the 1factory portal. Simplify FAI, PPAP, SCAR, and ongoing Supplier Quality Management. Collaborate with suppliers to speed-up new product introduction, and ensure quality at source.
4 Deep Supplier Collaboration
With 1factory's powerful "deep collaboration" capability, you (the customer) can connect with your suppliers and view their control plans, and manufacturing inspection data in real-time. With a shared understanding of the data, you and your supplier can work together to resolve problems before parts are shipped.
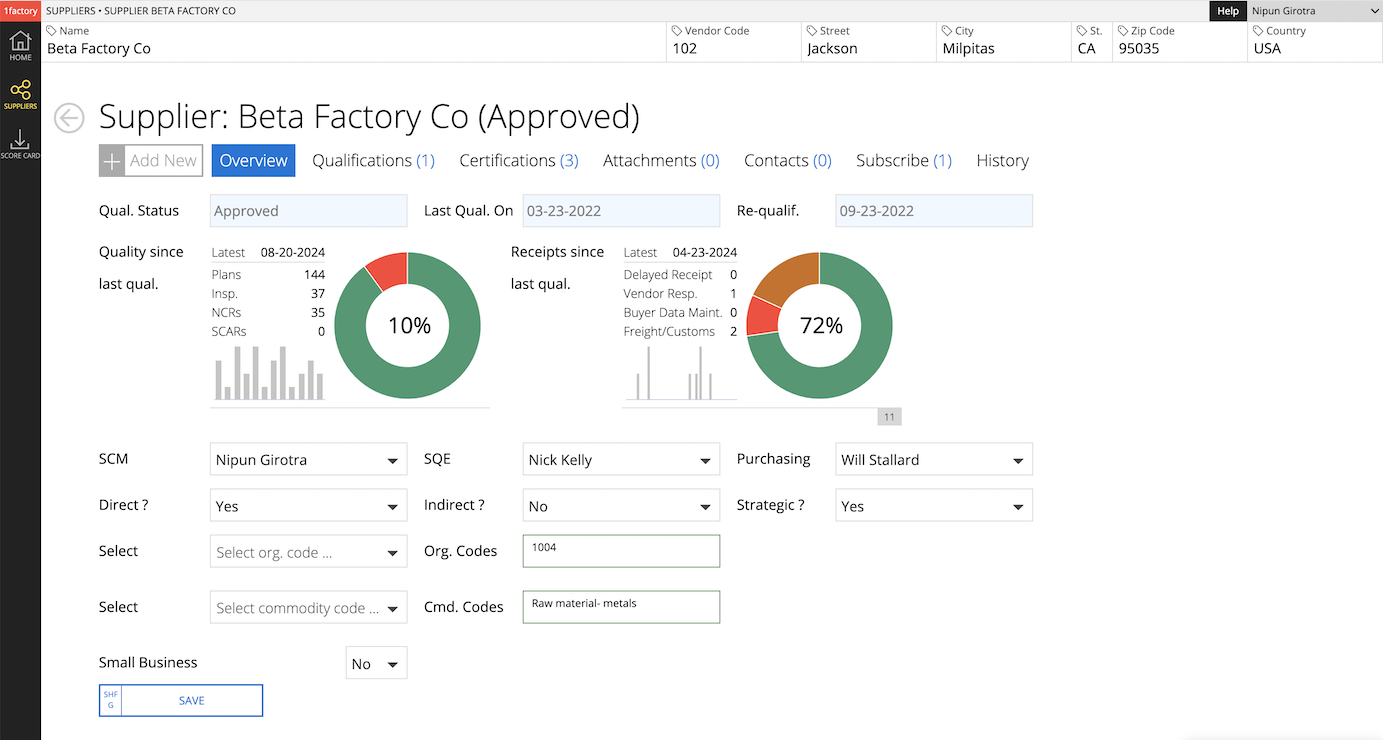
5 Supplier PPAP Management
Create and assign PPAPs to suppliers with 1factory's Supplier Quality software. Specify Levels, Requirements, Reason Codes, and Due Dates. Simplify PFMEA and Control Plan creation for suppliers. Review supplier PPAP documentation, provide feedback, and approve individual elements and the complete PPAP package.
6 Supplier Control Plans
Easily create and share quality control plans with suppliers or work with your suppliers to develop their quality control plans. Ensure adequate controls for critical product features and process parameters to prevent mistakes and control variation.
7 Supplier First Articles
Speed-up the FAI process for suppliers with automated drawing ballooning, CMM data collection, and FAI report creation. Ensure all required data and certs are collected. Review and approve supplier FAIs.
8 Supplier Inspections
Simplify and automate data-collection for suppliers. Ensure that suppliers are collecting data in a systematic manner and verify measurements against specifications at the point-of-manufacturing. Detect problems early and assess risk before parts leave the supplier. Review and approve or reject inspections.
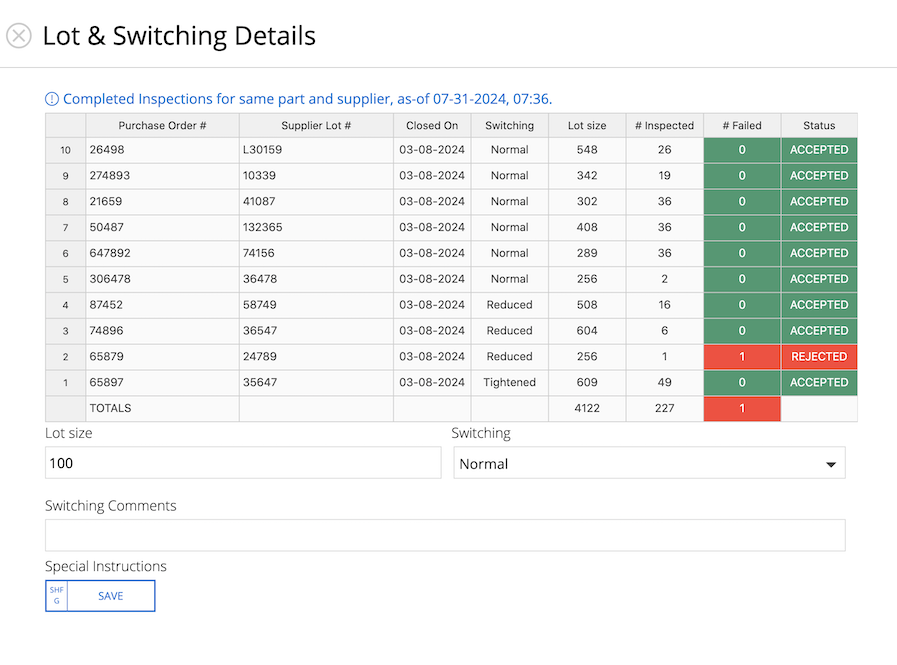
9 Supplier Corrective Actions
Request Corrective Actions (SCARs) from suppliers using the 1factory Supplier Quality Management software. Work together with suppliers to resolve problems and prevent recurrence. Ensure all 8D sections are filled-out, supplier actions are completed and effectiveness is verified prior to closing out the corrective action.
10 Data: Customer to Supplier
With this capability, you (the customer) can balloon drawings, create control plans and assign plans to your suppliers. You can also share incoming inspection data with your supplier to ensure alignment. This is ideal for situations where the customer/OEM defines what needs to be measured, at what frequency, and how it needs to be measured.
11 Data: Supplier to Customer
With this capability, your supplier can balloon drawings, create control plans and share those plans with you (the customer). Your suppliers can also share first articles and real-time manufacturing inspection data with you. This is ideal for situations where the supplier defines what needs to be measured, at what frequency, and how it needs to be measured.
12 Dashboards & Scorecards
1factory provides built-in supplier-level and part-level dashboards, scorecards and analytics. Buyers can manage Supplier Performance in DPPM (Defects in Parts per Million) or in Percentage terms. Buyers can also view feature-level SPC data (run-charts and histograms) to review manufacturing data and identify issues.
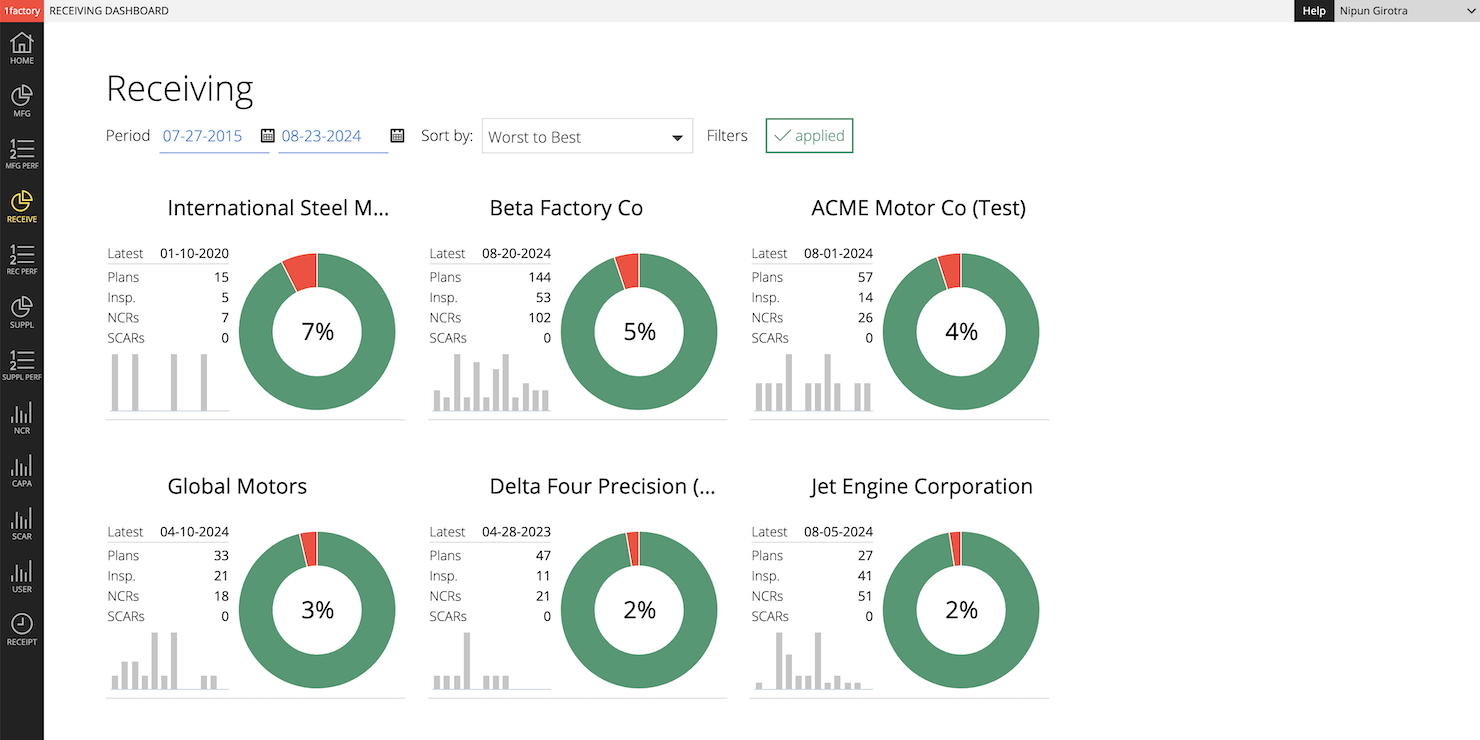
CASE STUDIES
Zipline - Autonomous Aircraft
Zipline designs, manufactures and operates the world's largest autonomous aircraft network, delivering life-saving supplies such as blood and medicines, and cutting delivery time from hours to minutes.
High-quality parts are critical to successful and reliable delivery. To ensure the quality of parts coming in from suppliers, Zipline deployed the 1factory system across its supply chain. Today suppliers create Control Plans and First Articles and submit them to Zipline for review and approval via 1factory. Once Plans and FAIs are reviewed, suppliers submit on-going inspection data to Zipline via 1factory.
Watch a 7-minute video to hear first-hand from the Zipline team (Incoming Inspection, Quality Engineering, Supplier Quality, and Chief Technology Officer) about the power of 1factory, its ease-of-use, and its impact on cost of quality.
EASY TO USE. LIGHTNING FAST.
INTUITIVE DESIGN
1factory is designed for the front-line of quality control with design inputs and ideas from our users. 1factory's intuitive navigation and best-in-class screen-designs make training a breeze. Training and full-deployment takes under two hours with no disruption to operations.
LIGHTNING FAST SPEED
1factory is engineered to be lightning-fast. We serve customers all over the world 24 hours a day, 7 seven days a week, 365 days a year. Our customers in United States, Mexico, Canada, Israel, China, South Africa, Denmark, UK, India, Malaysia, Taiwan all enjoy lightning-fast data collection and powerful real-time analytics.
SECURE AND RELIABLE
SECURITY
1factory is hosted on AWS GovCloud. The AWS GovCloud service is an isolated Amazon region designed to host sensitive data and regulated workloads, including International Traffic in Arms Regulations (ITAR) data.
All customer data transfer from client to server is encrypted over standard HTTPS/TLS 1.2, using a certificate with 2048-bit RSA public key / SHA-256 with RSA encryption. All customer data is encrypted at rest. Data (e.g. Part Numbers, Measurements etc.) are stored in an encrypted Amazon RDS instance. Drawings, Raw Material Certificates etc. are stored on encrypted Elastic Block Storage (EBS) volumes. Drawings and other documents may be additionally encrypted with individual encryption keys.
1factory complies with all NIST-800-171 requirements. 1factory also maintains a SOC2 Type 2 certification, and a copy is available upon request.
RELIABILITY
1factory has been engineered to be highly reliable, scalable and available. Over 200 million parts have been inspected with 1factory by customers in 26 countries.
1factory has delivered an uptime of >99.99% over the last 8 years. We use a third-party service to monitor system uptime, and our customers can view our uptime and availability metrics in real time.
1factory backs-up database with a daily snapshot. Files are stored on redundant hard-drives and backed up via daily snapshots.
BENEFITS: SUPPLIER QUALITY SOFTWARE
CHALLENGES IN SUPPLIER QUALITY MANAGEMENT
It is increasingly difficult to control product quality across the supply chain. Increasing product complexity (product variants, number of parts, and number of features) and increasing supply chain complexity (number of suppliers, number of tiers, and global spread) make quality control very challenging
The globalization of supply chains has created multi-tiered networks that span continents, making direct oversight and quality control significantly more challenging. Most buyers lack real-time visibility into supplier production data, forcing them to operate reactively and discover quality issues only after defective parts have entered the supply chain.
A significant number of product defects now originate in the supply chain, leading to production disruptions, shipment delays, and wasted capacity. The risks and costs of supplier quality issues extend beyond the factory. A single quality escape can put end-customer health and safety at risk, potentially resulting in expensive recalls and reputation-damaging litigation.
Traditional quality management methods have proven inadequate for today's challenges. Existing IT systems were never designed for collecting and monitoring feature-level data across a global supply chain. Organizations resort to manual methods like receiving inspections, witness inspections (source inspections), and emailed spreadsheets to control quality. These approaches burden both buyers and suppliers with time-consuming processes, leading to costly delays, data gaps, and quality escapes.
The lack of standardized quality management processes across suppliers further complicates the challenge. Each supplier may use different reporting formats, making it difficult to compare performance and identify systemic issues. This variation in data management creates additional overhead in monitoring and managing supplier quality performance.
Without real-time insight into supplier production processes, buyers cannot proactively address quality risks before they impact the supply chain. This reactive approach to quality management increases costs, extends problem resolution time, and raises the risk of defective products reaching customers.
THE 1FACTORY SUPPLIER QUALITY MANAGEMENT SOFTWARE SOLUTION
1factory's Supplier Quality software directly addresses the complexity of modern supply chains by providing a unified cloud-based platform that connects manufacturers with their multi-tiered supplier networks. The platform standardizes quality management processes across all suppliers regardless of their location or tier, eliminating the confusion created by varying reporting formats and data management systems.
Unlike traditional manual methods that rely on emailed or uploaded spreadsheets, 1factory provides real-time visibility into supplier production data. This transforms reactive quality management into proactive risk prevention, allowing buyers to identify and address quality issues before defective parts enter the supply chain.
The platform's automated data collection capabilities integrate directly with CMMs, Vision Systems, and Digital Gages, eliminating the time-consuming manual processes that burden both buyers and suppliers. Automated process capability calculations (Cp, Cpk, Pp, Ppk) and SPC provide immediate insights into process performance, reducing the data gaps and delays that plague traditional approaches.
1factory's early warning system uses lot defect risk analysis to prevent quality escapes before they impact production or reach customers. This proactive approach significantly reduces the risk of costly recalls, reputation damage, and litigation that can result from defective products reaching end-customers.
The platform streamlines the New Product Introduction process by enabling suppliers to efficiently assemble PFMEAs and Control Plans using a built-in process library. Buyers gain immediate visibility into supplier readiness and can track FAI and PPAP submission status across multiple parts, eliminating the bottlenecks that traditionally slow product launches.
1factory simplifies supplier management and speeds up root cause analysis, with instant access to data by purchase order, lot number, operator etc.
By replacing manual, reactive quality management with automated, proactive systems, 1factory helps manufacturers regain control over product quality across their entire supply chain, regardless of its complexity or global spread.
500+ CUSTOMERS. 30+ COUNTRIES. 20+ INDUSTRIES.
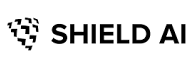
AEROSPACE & DEFENSE

AEROSPACE MACHINING
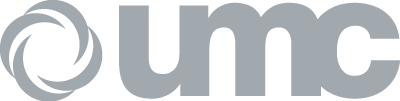
PRECISION MACHINING
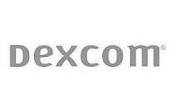
MEDICAL DEVICES
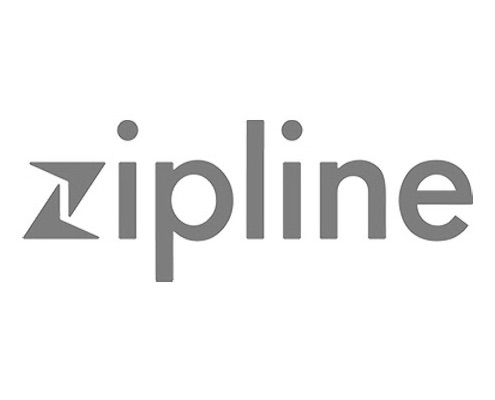
AUTONOMOUS AIRCRAFT
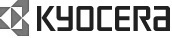
ADVANCED CERAMICS