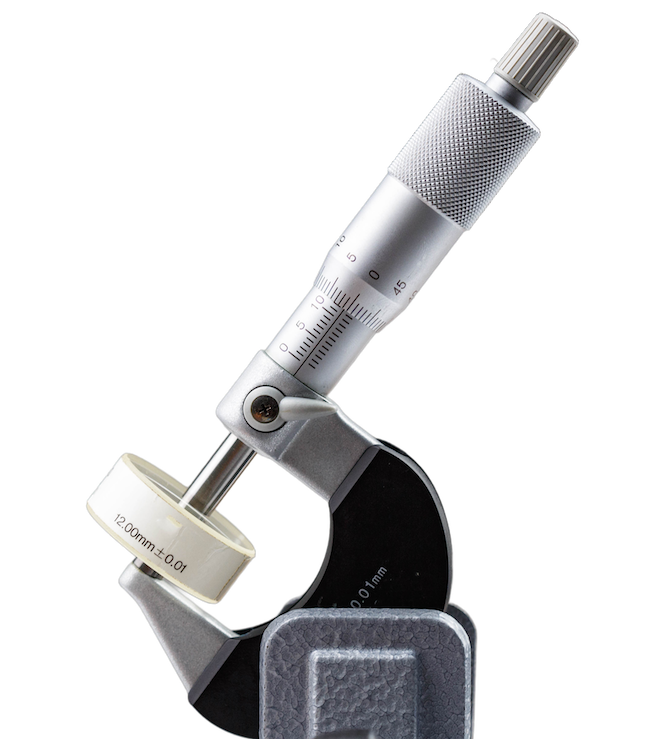
Powerful, Easy-to-Use, Lightning-Fast
Gage Calibration Management Software.
1factory's Gage Calibration software, makes it easy to manage calibration schedules and records for thousands of gages. With the Gage Management software, manufacturers can transact gages between Tool Crib, Factory Floor, and Calibration Vendors, create and manage Gage Kits, perform Gage R&R studies, and link gages to inspection lots for deep traceability.
With 1factory, manufacturers maintain calibration for tens of thousands of gages, avoid quality problems, and easily trace gage usage history across jobs.
LOAD 100,000+ GAGES. TRACK USAGE. EFFORTLESSLY MANAGE CALIBRATIONS.
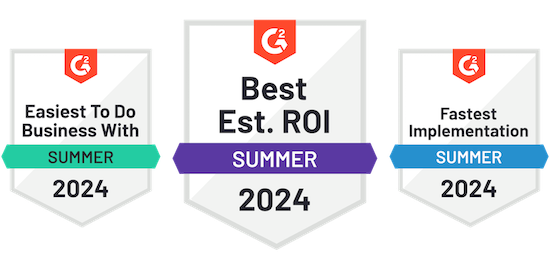
EASY TO USE
“One of the most useful features is the Master Gage library, this can set up reminders for calibration, calibration history, serial numbers, attachments and practically anything to manage complex environments like ours with many hand gauges, tools and equipment.
It gives you easy to understand color-coded warnings to alert you that some of your gages and equipment are due for calibration. Plus it has built-in sorting capabilities to easily find the record that you are looking for.”
S. Avila, Stone Machine
GAGE CALIBRATION MANAGEMENT FEATURES
1 Easily Import Gages
Load individual gages using the web-form, or load thousands of gages in a few seconds using our standard excel import template. Define Make, Model, Serial Number, Units, Resolution, Calibration Interval, and Accuracy.
2 Manage Calibration Schedules
Manage calibrations for all gages. Set frequency in Days or Months. Schedule to Exact Date or to End-of-Month. Instantly identify gages with Upcoming and Upcoming calibrations. Receive email notifications for upcoming calibrations.
3 Transact Gages
Transact Gages between Tool Crib, Factory Floor, and Calibration Vendors with simple barcode scanning. Issue gages from storage to a factory floor location (for a job number and operation), or to a user. Return gages to storage locations. Withdraw gages from the factory floor and from storage for calibration.
4 Create Pick Lists
Use powerful search to find gages. Generate a job-specific gage pick-list with a single click. Quickly find, pick and transact gages needed with built-in barcode printing and scanning capability.
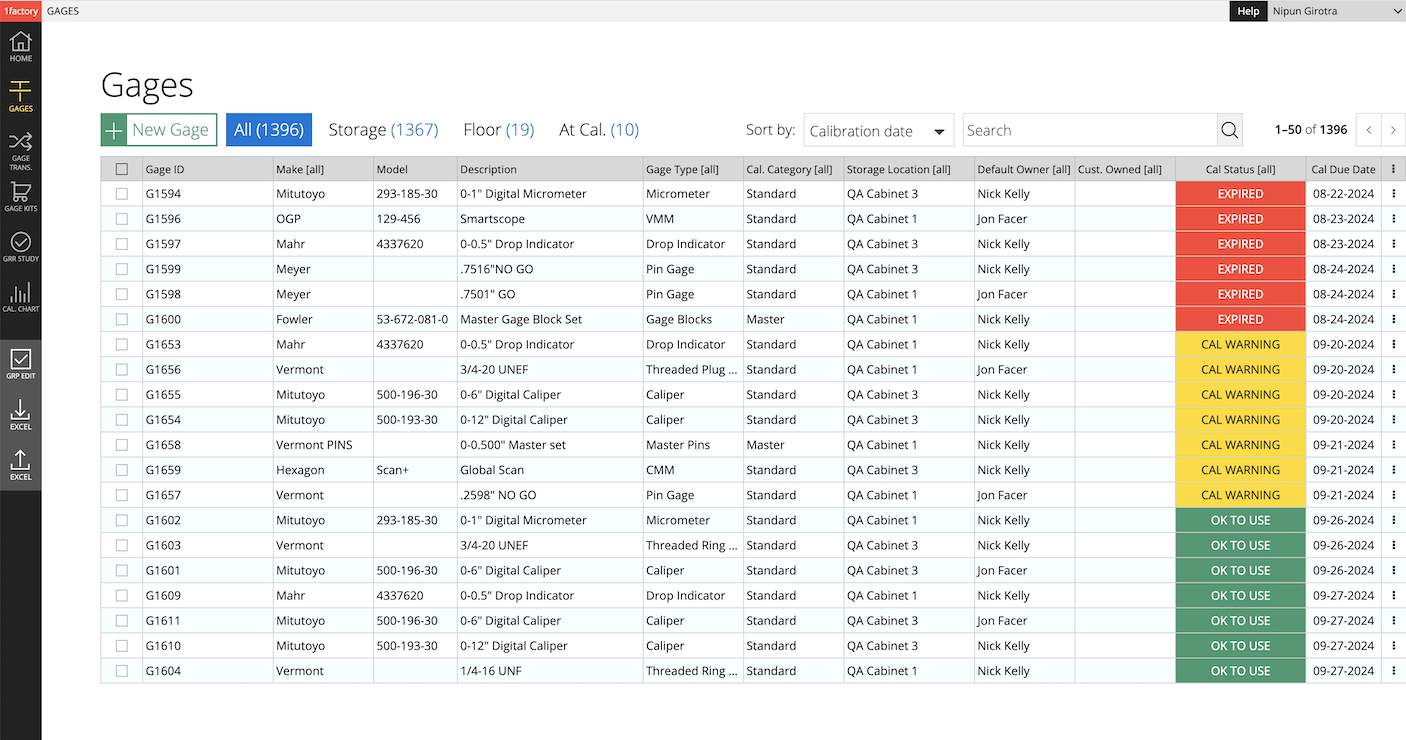
5 Record Calibration Measurements
Manage internal and external calibrations. Capture before-calibration (as found) and after-calibration (as calibrated) measurements against required tolerances. Record master gage IDs for NIST Traceability, actions taken, and notes. Attach associated vendor calibration certs.
6 Calibration Workload Planning
Chart the number of gages coming due for calibration by month and week to plan your workforce and capacity. Withdraw customer-owned gages early to allow for replacement lead-time.
7 Print Calibration Labels
Print barcoded calibration labels with Gage ID, Last Calibration Date, Calibration Due Date and Notes. Speed-up gage transactions with barcode readers.
8 Capture Digital Signatures
Access detailed gage calibration history with the user's name and time stamp. Ensure all calibration records are digitally signed for 21 CFR Part 11 Compliance before a gage is released for use on the factory floor.
9 Output Calibration Reports
Print calibration reports for customers and auditors with a complete record of all calibration functions, measurements, master gages used, condition before, condition after, and temperature and humidity.
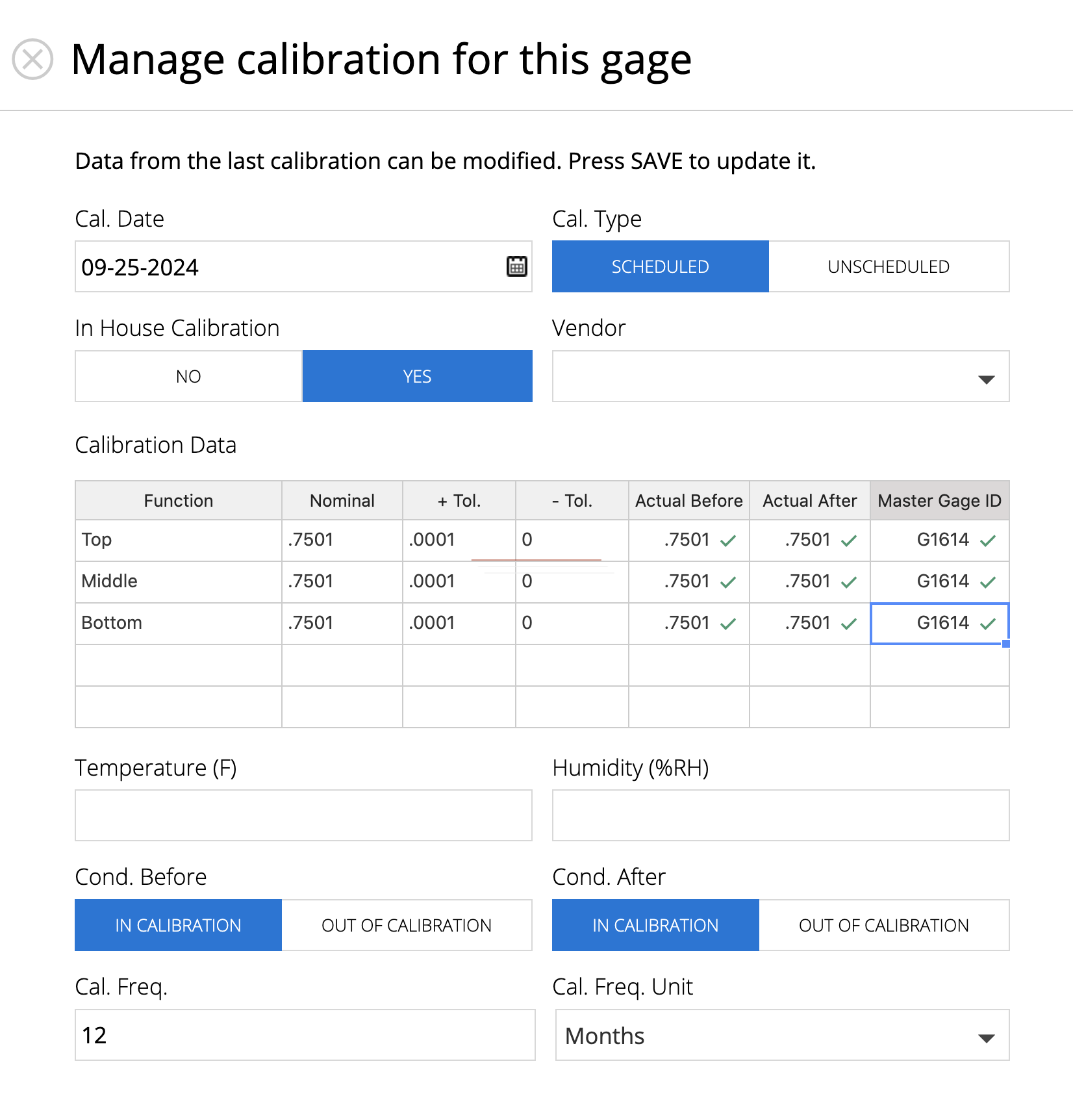
10 Gage Kits
Organize and manage part-number-specific kits of gages e.g. pin gages, thread gages, or other gages that are custom to a part or a family of parts. Easily find and transact all the gages required for a given part.
11 Gage R&R / MSA
Perform Variable Gage R&Rs. Configure number of operators, parts and trials. Instantly generate reports for both the ANOVA and Range methods. Accept/reject based on NDC, % Tolerance, % Contribution etc.
12 Classify Gages
Classify gages into Standard, Master Gages, Reference Gages, Fixtures, Customer Owned Gages etc. Customer-Owned gages require longer lead-tiems for calibration. Master gages can be recorded in calibration records for traceability to NIST standards. Reference Gages are not used for production and show up with a red warning in an inspection. Fixtures do not require calibration but require periodic maintenance.
13 Track Gages & Manage Recalls
Track gage by job number and feature. Easily find and recall all jobs for a specific gage and time period when needed.
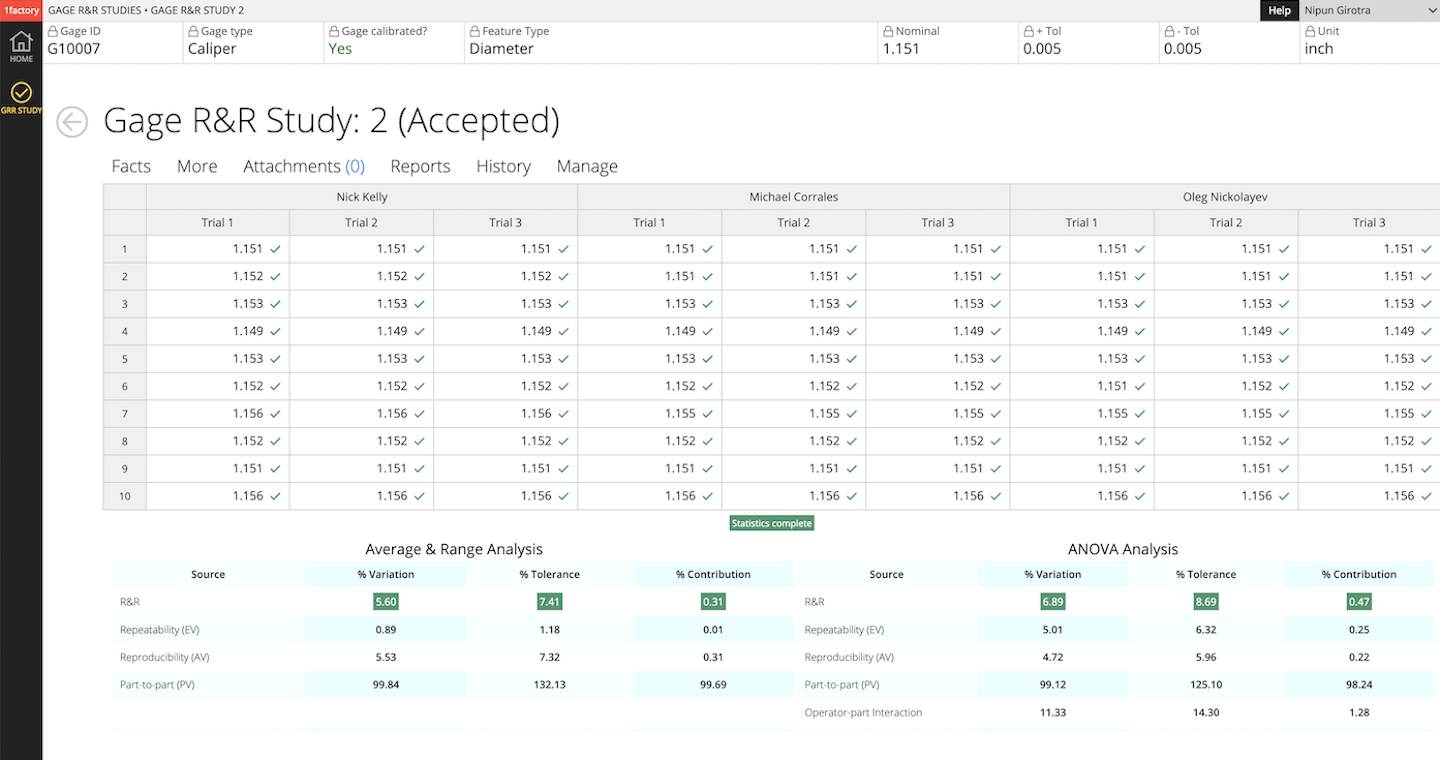
CASE STUDIES
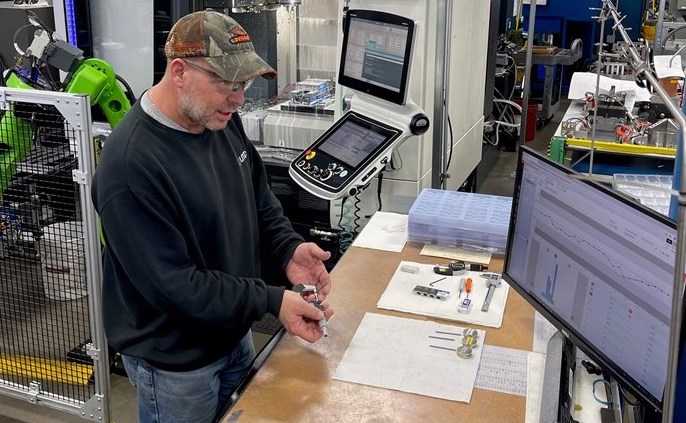
Ultra Machining Company (UMC)
Ultra Machining Company (UMC) is a manufacturer of high-precision components for medical device, aerospace, and defense applications. Products manufactured by UMC are complex, with 100 — 800 features per product. And as a result, UMC maintains over 10,000 hand-gages to verify product conformance to specification.
"(1factory) also identifies which gage or CMM was used for inspection, and can identify all prior inspections performed with that gage."
"On top of that, the software tracks calibration schedules for all measurement equipment - which at UMC includes more than 10,000 hand gages - and displays a red flag if an operator attempts to use a gage that requires calibration."
Read the full Modern Machine Shop Feature on 1factory's work with UMC.
EASY TO USE. LIGHTNING FAST.
INTUITIVE DESIGN
1factory is designed for the front-line of quality control with design inputs and ideas from our users. 1factory's intuitive navigation and best-in-class screen-designs make training a breeze. Training and full-deployment takes under two hours with no disruption to operations.
LIGHTNING FAST SPEED
1factory is engineered to be lightning-fast. We serve customers all over the world 24 hours a day, 7 seven days a week, 365 days a year. Our customers in United States, Mexico, Canada, Israel, China, South Africa, Denmark, UK, India, Malaysia, Taiwan all enjoy lightning-fast data collection and powerful real-time analytics.
SECURE AND RELIABLE
SECURITY
1factory is hosted on AWS GovCloud. The AWS GovCloud service is an isolated Amazon region designed to host sensitive data and regulated workloads, including International Traffic in Arms Regulations (ITAR) data.
All customer data transfer from client to server is encrypted over standard HTTPS/TLS 1.2, using a certificate with 2048-bit RSA public key / SHA-256 with RSA encryption. All customer data is encrypted at rest. Data (e.g. Part Numbers, Measurements etc.) are stored in an encrypted Amazon RDS instance. Drawings, Raw Material Certificates etc. are stored on encrypted Elastic Block Storage (EBS) volumes. Drawings and other documents may be additionally encrypted with individual encryption keys.
1factory complies with all NIST-800-171 requirements. 1factory also maintains a SOC2 Type 2 certification, and a copy is available upon request.
RELIABILITY
1factory has been engineered to be highly reliable, scalable and available. Over 200 million parts have been inspected with 1factory by customers in 26 countries.
1factory has delivered an uptime of >99.99% over the last 8 years. We use a third-party service to monitor system uptime, and our customers can view our uptime and availability metrics in real time.
1factory backs-up database with a daily snapshot. Files are stored on redundant hard-drives and backed up via daily snapshots.
BENEFITS: GAGE MANAGEMENT SOFTWARE
GAGE CALIBRATION CHALLENGES
Effective gage calibration management is fundamental to quality control, ensuring measurement accuracy and product conformance. This process extends far beyond simple periodic calibration, encompassing gage tracking, measurement system analysis (including Gage R&R studies), usage history, and recall management. Every measurement device, from simple calipers to complex CMMs, requires documented calibration and traceability.
Without proper calibration management, manufacturers risk making decisions based on unreliable measurements, potentially leading to quality escapes or unnecessary production adjustments.
Today's manufacturers struggle to manage calibration for thousands of gages across multiple locations and use cases. Teams face complex logistics tracking gages between tool cribs, factory floor locations, and external calibration vendors. Traditional systems fail to maintain clear links between gages and their measurement history, making recall situations particularly challenging.
Quality teams waste hours maintaining spreadsheets of calibration schedules, tracking down overdue gages, and manually documenting Gage R&R studies. Without real-time visibility into gage status and history, manufacturers risk using out-of-calibration equipment or losing track of affected measurements, compromising the reliability of their entire quality control process.
1FACTORY GAGE CALIBRATION MANAGEMENT SOLUTION
1factory transforms gage calibration from a tracking nightmare into a streamlined, automated process. The platform manages the complete gage lifecycle - from calibration scheduling and vendor management to Gage R&R studies and usage tracking. Quality teams gain real-time visibility into gage locations, calibration status, and upcoming due dates, eliminating the need for manual spreadsheet maintenance.
1factory automatically links gages to inspection lots, enabling instant retrieval of potentially affected measurements during recall situations. This critical capability addresses one of the most challenging aspects of traditional calibration management by maintaining clear connections between measurement devices and their usage history across all locations and applications.
For both in-house and vendor calibrations, the platform maintains comprehensive records while simplifying gage transactions between tool cribs, production areas, and calibration providers. This integrated approach ensures measurement integrity while dramatically reducing the administrative burden of calibration management, enabling quality teams to focus on analysis rather than tracking and documentation.
500+ CUSTOMERS. 30+ COUNTRIES. 20+ INDUSTRIES.
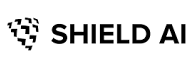
AEROSPACE & DEFENSE

AEROSPACE MACHINING
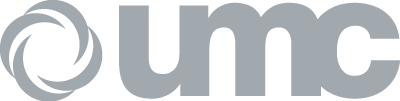
PRECISION MACHINING
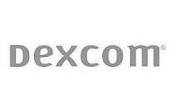
MEDICAL DEVICES
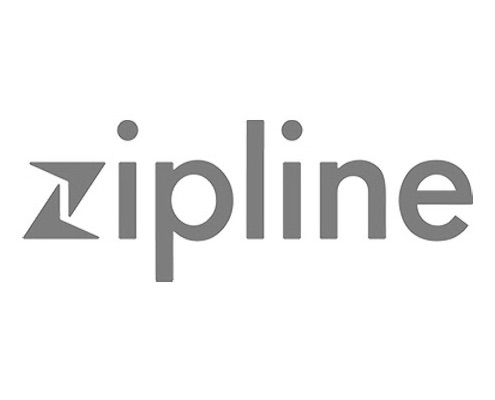
AUTONOMOUS AIRCRAFT
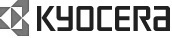
ADVANCED CERAMICS