Savage Arms Accelerates Time-to-Market and Improves Efficiency with 1factory
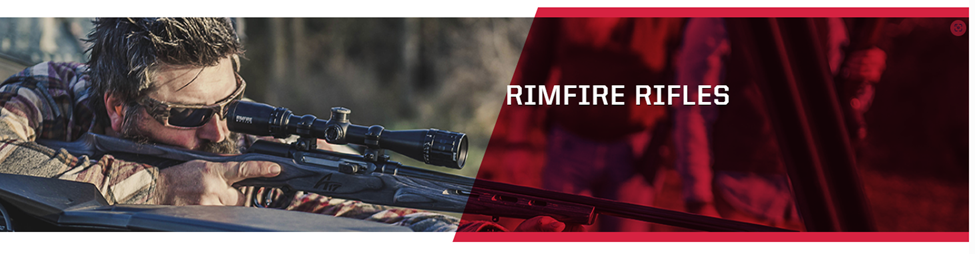
A Rich History
Savage Arms Canada, located in Lakefield, Ontario, is a leading firearms manufacturer known for producing high-quality rifles, shotguns, and accessories. The company's legacy is rooted in Lakefield Arms, a manufacturer that pioneered the development of precision firearms in Canada. In the late 20th century, Lakefield Arms was acquired by the American-based Savage Arms. The acquisition marked Savage Arms' first presence in Canada, and the Lakefield facility quickly became an integral part of the company's production capabilities. Today, Savage Arms Canada combines its rich heritage with cutting edge manufacturing techniques to meet the needs of modern shooters. The precision, durability, and affordability of Savage Arms Canada's products make them a preferred choice for hunters, sports shooters, and professionals across North America and beyond.
High Complexity and Rigorous Quality
Rifle Manufacturing and assembly is a precise and skilled process fundamental to producing reliable and high-performing firearms. This meticulous process involves carefully assembling intricate components into a fully functional firearm. The barrel, receiver, trigger mechanism, and stock must each be manufactured to exact specifications and undergo rigorous quality inspection to ensure every rifle operates safely and effectively. Savage Arms uses CNC machines to fabricate these components, and also sources components from trusted suppliers.
In 2020, as part of their ongoing quest for quality, Savage proactively implemented a supplier quality framework that goes above and beyond what is required in the firearm industry. The Production Parts Approval Process, or PPAP for short, is the AIAG (Automotive Industry Action Group) tool used to standardize the approval process between supplier and buyer for new and revised parts. It is a set of defined documents that, when completed and adhered to, ensures a manufacturer’s ability to meet stringent quality requirements and mitigate risks and inconsistencies across the supply chain. The structured PPAP approach not only facilitates clear communication between suppliers and manufacturers, but also enhances overall product reliability and performance. When managed poorly, PPAP can potentially add major logistical overhead and paperwork to the production of parts, consequently increasing costs and frustrating supply chains.
Initial PPAP Efforts
Savage initially began managing all PPAP documentation via a homegrown Excel-based system. While quick and familiar to set up, it soon became clear that the system was susceptible to issues caused by inaccurate data entry, broken Excel functions, and human error. Furthermore, consistent version control was virtually impossible, as several employees cordinate simultaneously on different copies of the same files, leading to confusion throughout the PPAP process. The homegrown PPAP system also lacked the security features needed to safeguard sensitive product information, leaving the door open to potential data exposure, unauthorized access, and even complete data loss. As Savage’s data grew, the entire process became cumbersome and inefficient, preventing timely and secure access to pertinent information.
Despite its auspicious beginnings, the system was bogging down the Savage team, and they began a search for a comprehensive, out-of-the-box software that could scale to handle the growing volume and complexity of supplier PPAPs they manage.
A Better Path
Savage Arms was introduced to 1factory, a quality control software that simplifies and automates all aspects of quality planning, inspection data collection, PPAP management, and all other QC tasks pertinent to precision manufacturers. Savage reviewed and tested 1factory and decided to give it a shot.
Savage was initially attracted to 1factory's modern interface and intuitive approach to handling PPAPs, but as they grew more familiar with the software discovered additional features and their use of the software grew significantly. Since 2023, Savage has solely used 1factory for all supplier quality management activities, including vendor approvals, scorecards, PPAPs, and receiving inspections. Quality Manager Arron McChesney states, "1factory's cloud-based solution has greatly simplified the process for receiving, reviewing, and approving production parts from suppliers, ensuring compliance to quality standards and reducing the administrative burden often associated with PPAP.”
How the 1factory PPAP Module and Supplier Portal Works
1factory can help both buyers and suppliers of parts. On the supplier side, 1factory creates PPAP documentation such as PFMEA, control plans, process flows, and MSA and compiles entire submission packages to be shared with customers. Being on the buyer side, Savage Arms primarily uses 1factory to receive and store their supplier’s PPAP documents.
When initially setting up 1factory, Savage Arms configured which documents are required at each PPAP level. When it is time to require certain PPAP documents from a certain supplier, they simply go into 1factory, fill out the form below, and forward the resulting list of required documents to the supplier.
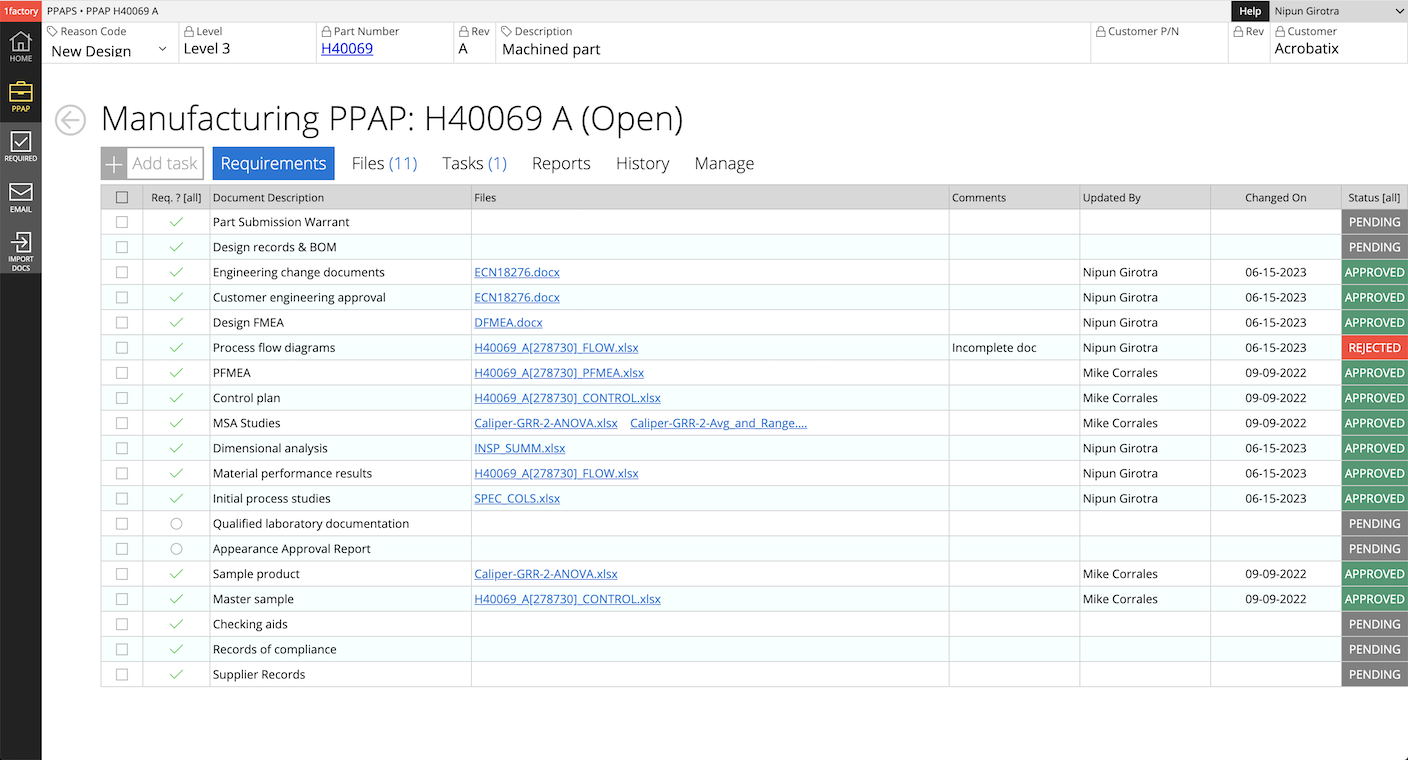
Savage Arms can track the due date of all outstanding PPAPs, and once they receive the supplier's PPAP submission (either directly through 1factory or via email) each document can be attached to the appropriate location, reviewed, and either accepted or rejected.
Organizing and centralizing all supplier documents makes it significantly easier for everyone in the Savage Arms organization to access, review, and provide feedback on these documents and the functions they affect. No longer are files stuck in one employee's email or hidden in a convoluted file path; everything is searchable and clear, simplifying the supplier review process and speeding up the time to market for finished goods.
Many other useful features in 1factory's PPAP module, like individual tasks and notifications, can be utilized to further improve traceability and transparency of the PPAP process.
Savage Arms' Review of 1factory
Savage Arms Canada’s Quality Assurance Manager, Arron McChesney works in the 1factory system daily. When asked about changes at Savage since 1factory was implemented, McChesney notes, “By utilizing 1factory PPAP, we have achieved greater efficiency and accuracy in all our quality control processes. The platform has facilitated real-time collaboration between us and our suppliers, enabling faster resolution of issues and more transparent communication. This modernized process not only accelerates time-to-market but also enhances product quality and consistency. All this makes 1factory an invaluable tool for Savage Arms and any other company striving to exceed quality requirements and maintain a competitive edge.”
McChesney breaks down the benefits of using 1factory to manage PPAPs into the following categories:
- Efficiency: 1factory has streamlined our PPAP process by automating the administrative tasks involved with documentation, speeding up submissions and approvals.
- Enhanced Data Accuracy: With its automated data validation and centralized document management, 1factory ensures that all our information is accurate and up to date.
- Improved Traceability: 1factory allows for better visibility into the status of each part and the approval process, enhancing transparency and accountability.
- Scalability: The platform is designed to handle large volumes of data and complex processes, making it suitable for manufacturers of all sizes.
- Integration: 1factory integrates with our other systems and tools and existing workflows, enhancing our overall operational efficiency.
- Data Security: 1factory is set up with everything we need to ensure our sensitive data is safeguarded against unauthorized access and loss.
- User-Friendly Interface: the software’s intuitive interface makes it accessible for users with varying levels of technical expertise.
1factory is thankful for customers like Savage Arms Canada that relentlessly pursue high quality in all aspects of their production. This, in turn, leads to valuable feedback and improvement requests that result in enhanced features for all customers.