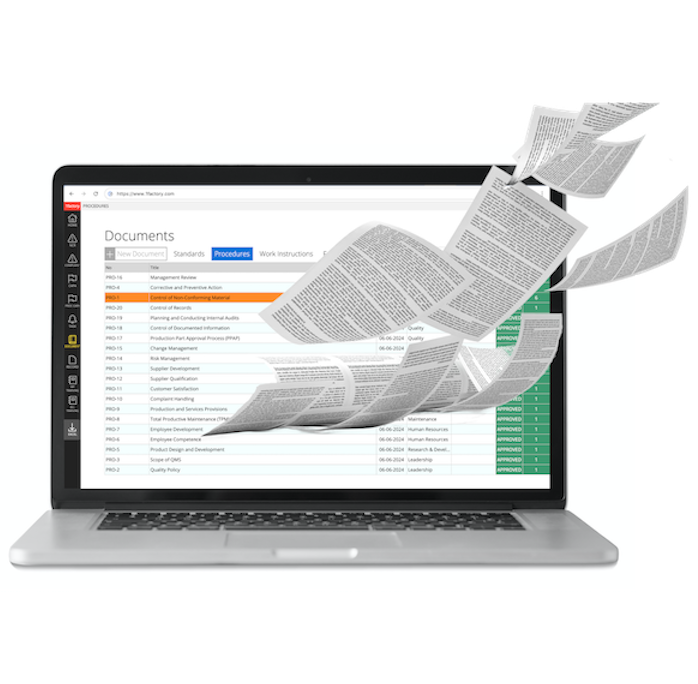
Powerful, Easy-to-Use, Lightning-Fast
Quality Management Software (QMS).
1factory's QMS software simplifies every aspect of quality management, including document authoring, redlines, version control, approvals, access control, training management and more. 1factory also provides powerful issues management capabilities for NCRs, CAPAs, SCARs, Audit Findings, and Complaints.
With 1factory, manufacturers ensure all regulatory and customer requirements are met, users are working with up-to-date documents, and training is complete. 1factory simplifies audit preparation saving thousands of man-hours each year.
AUTOMATE COMPLIANCE. GET CERTIFIED FASTER. ACE YOUR AUDITS.
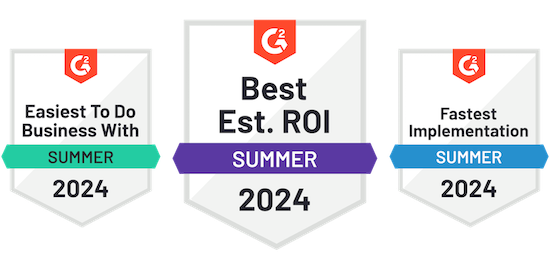
COMPLIANCE MADE EASY
Eliminate paper and Word documents with 1factory's Document Control software.
Effortlessly ensure all requirements from standards (AS9100, ISO9001, ISO13485, AS13100 etc.), regulatory bodies (FDA etc.), and customers are addressed by procedures and work instructions.
Ensure all documents are always up-to-date and users are working with the latest versions. Easily assign and track training to completion. Ensure all corrective and preventive action tasks are complete.
Ace your audits.
OVERVIEW: QUALITY MANAGEMENT SYSTEM (QMS)
WHAT IS A QUALITY MANAGEMENT SYSTEM (QMS)?
A Quality Management System (QMS) enables organizations to deliver world-class products and services through effective documentation, execution, and continuous improvement of their business processes.
A QMS can be complex - organizations must document all their business processes, often hundreds of interconnected processes, from new product introduction and order entry through manufacturing, shipping, and invoicing.
Organizations must ensure proper review and approval of these procedures, maintain version control, assign training by role, and verify process effectiveness through regular audits.
Quality Management Software (also known as eQMS or Digital QMS) platforms provide a centralized digital framework where organizations can author and manage procedures, control document versions, and establish clear links between requirements, processes, and records.
These systems ensure that employees have access to the latest approved procedures they need. And they streamline training management by automatically tracking requirements across roles, managing new hire onboarding, and ensuring retraining when procedures change.
A QMS is not always a single software system. Instead, a QMS is typically a combination of software systems. For example, the business process for purchasing raw materials and the associated training for the purchasing process may be documented in a Doc Control system, while the purchasing process itself may be operated entirely in the ERP system and it's records may therefore reside in the ERP system.
An organizations Quality Management System provides the framework to ensure all these elements work together - maintaining clear documentation, verifying proper training, and enabling continuous improvement through systematic tracking of process performance, non-conformances, and corrective actions.
WHAT ARE SOME OF THE CHALLENGES WITH QUALITY MANAGEMENT SYSTEMS?
Setting up and maintaining a Quality Management System can be challenging.
Document authoring and version control is time-consuming and error-prone. Without proper systems, organizations struggle to track changes, maintain revision history, and ensure only current versions are in use.
Document review and approval processes are complex and difficult to manage. Tracking multiple approvers, managing feedback, and comparing document versions manually leads to delays and confusion.
As document repositories grow, finding specific procedures, work instructions, or records becomes increasingly difficult. Organizations struggle to maintain proper access controls while ensuring employees can quickly access the documents they need.
Training management becomes overwhelming as organizations try to track requirements across roles, new hires, and document revisions. Manual tracking of training completions and due dates leads to compliance gaps and missed deadlines.
Maintaining audit readiness is a constant challenge. Quality teams spend excessive time verifying document updates, confirming training completion, and ensuring compliance with standards and requirements.
Larger organizations with multi-site operations face additional complexity in document management. Organizations struggle to maintain consistency between corporate-wide procedures while managing site-specific requirements and ensuring proper document distribution.
Without a unified system linking requirements to procedures, organizations lack visibility into their quality system's effectiveness. Quality managers struggle to track document status, training compliance, and audit preparedness across the organization.
THE 1FACTORY QUALITY MANAGEMENT SOLUTION:
1factory's Quality Management Software simplifies all aspects of quality management, including document control, training management, issues management and more.
Authoring, Version Control, Approval: 1factory makes it easy to author and version-control documents. Documents can be routed for approvals by all required roles and users. And powerful red-line capability makes it easy to review changes across versions.
Organization and Search: 1factory organizes QMS procedures and work instructions with the correct context, making them easy to find, use and maintain. Access can be restricted to only the required roles. Powerful search instantly retrieves documents and records.
Issue Resolution & Prevention: 1factory provides comprehensive tools for managing quality issues across the organization. Customer complaints can be tracked from initial report through investigation, risk assessment, and resolution.
Training Management: 1factory makes itbeasy to assign training and track completion by role and by user. Training can be assigned at initial release or revision of a document, or when users are hired, change roles, and require retraining.
Corporate and Site Documents: 1factory's powerful multi-org capability makes it easy to manage both corporate-wide and site-specific procedures and work instructions, while ensuring employees are always working to the correct procedure.
Onboarding and Migration: 1factory's built-in data import tools simplify migration of documents - text and images - from legacy QMS systems and Word documents.
Audit Readiness: 1factory helps ensure that requirements are covered, users are trained and working to the latest version of documents. With 1factory, the quality system is always up-to-date and users are always prepared for an audit.
QUALITY MANAGEMENT SOFTWARE (QMS) FEATURES
1 Standards & Requirements
Digitize your Quality Management System. Simplify Document Control. Manage all external standards (e.g. ISO 9001:2015), customer-specific requirements (e.g. supplier quality manual), and regulatory requirements (e.g. 21 CFR Part 820) in one place. Digitize requirements and make them easy to find.
2 Procedures & Work Instructions
Author procedures and work-instructions with text and images directly in the 1factory Quality Management Software. Enjoy powerful version control, with clear change history across revisions. Establish clear links between standards (requirements), procedures, and other related documents.
3 Forms & Records
Manage Forms (e.g. Document Change Order) with revision control and approvals in the 1factory Quality Management Software. Ensure that records are generated only with the latest version of the form. Route records for approval. Easily search and retrieve records for audits.
4 Training Management
Simplify training management with 1factory's digital Quality Management Software. Establish training plans. Easily assign and track training by role and user. Generate training for (1) initial release & new revision of a procedure, (2) new hire or role change, (3) scheduled periodic retraining, and (4) retraining as part of corrective action. Ensure training is always up-to-date and avoid audit findings.
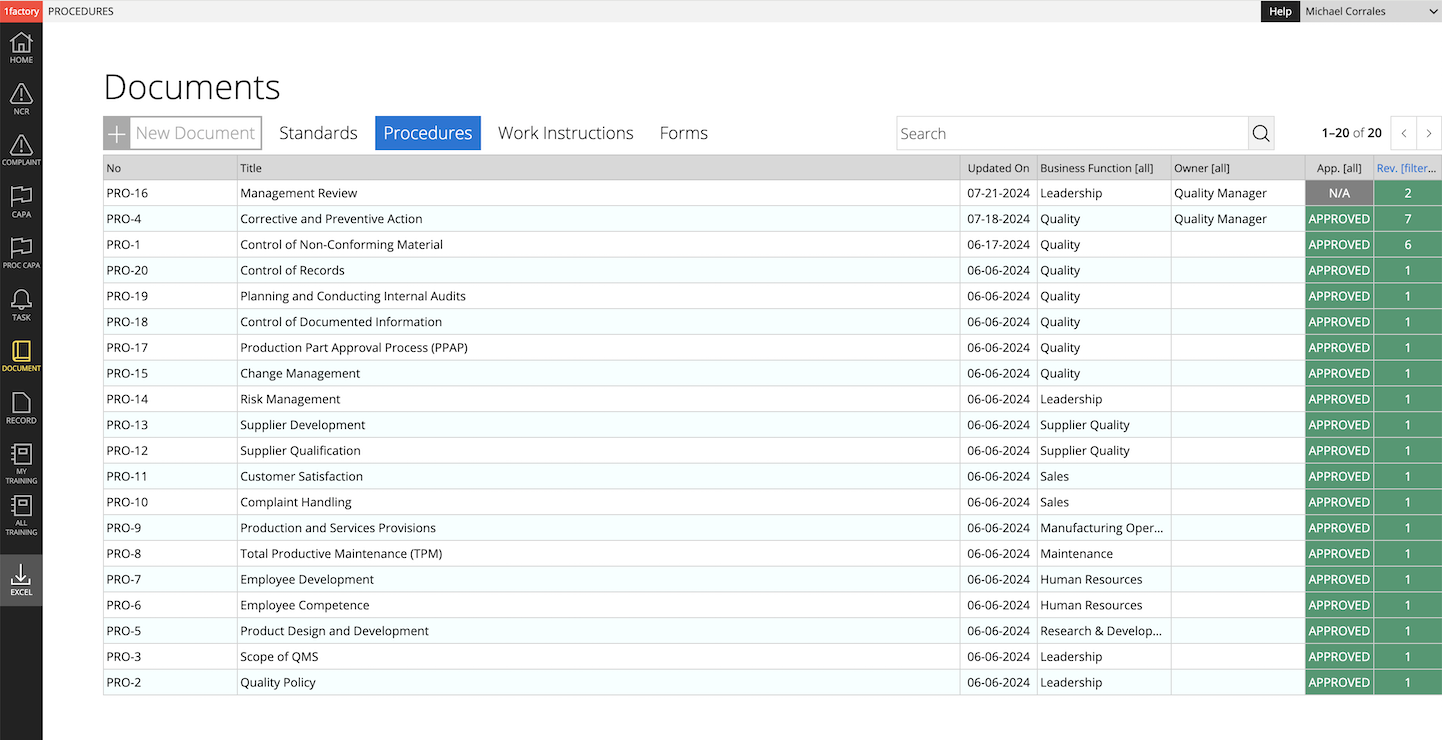
5 Multi-Site Deployments
Effortlessly manage corporate and site-specific procedures and work instructions with 1factory's Quality Management Software. Corporate documents apply to all or selected sites, while site-specific documents apply to only the specific site. Effortlessly assign and track training across all sites.
6 Access Controls
Protect critical documents and organizational intellectual property - procedures, work instructions, and records - by limiting access to specific user roles.
7 Approval Workflows
Route documents - procedures, work instructions, and records - for approval by role and user. Notify users of required approvals and document status changes via email. Record approvals and electronic signatures.
8 Change History & Version Control
Easily manage changes with powerful built-in document Change History, Redline View, and Version Control capabilities. Simplify document review and approval with the powerful redline view showing additions, deletions and edits.
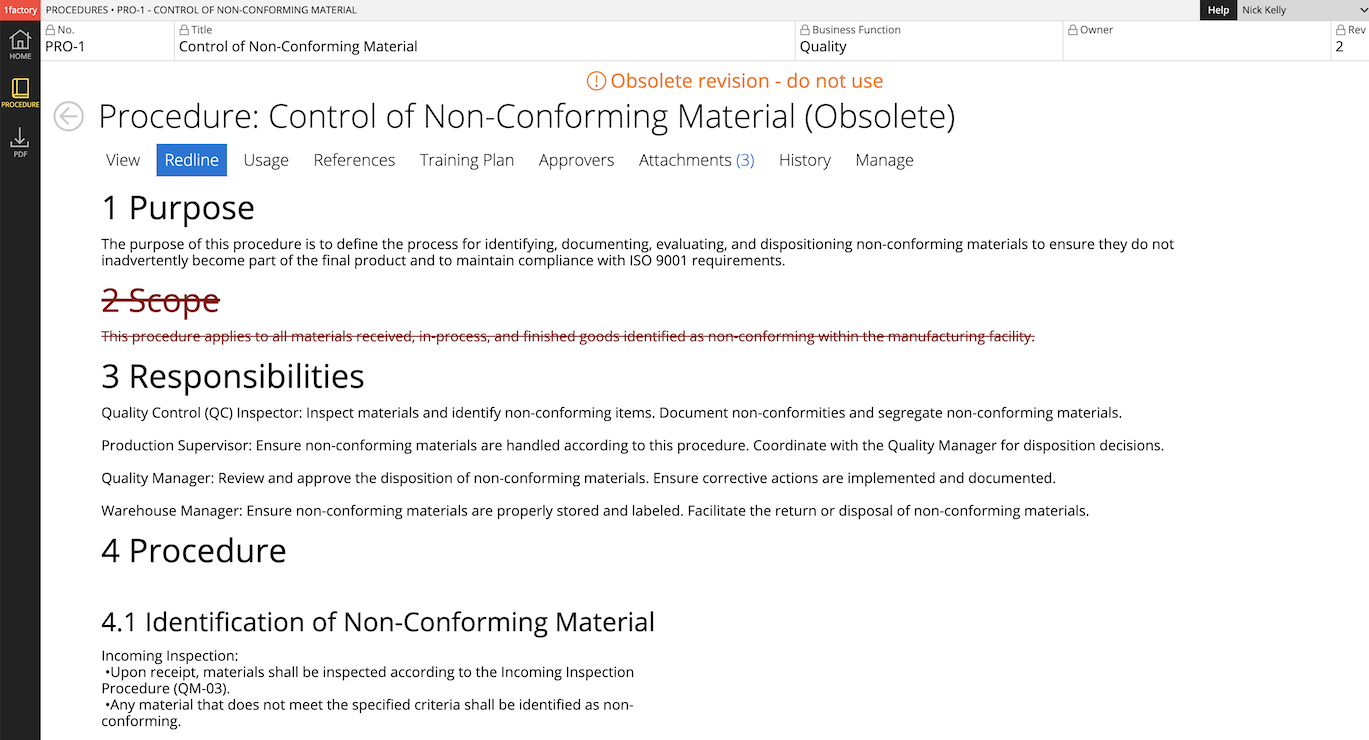
9 Non-conformances
Easily create and manage non-conformances for manufacturing or engineering caused defects, deviations, customer returns, audit findings, safety problems etc. Autopopulate NCR details from Inspections. Assign action-items, and use automated reminders to ensure timely resolution.
10 Corrective Actions
Initiate CAPAs and SCARs from NCRs. Setup CAPA templates to guide the user, and ensure a consistent problem-solving process. Track CAPA and SCAR progress, and use automatic reminders to ensure timely resolution. Review and Approve.
11 Supplier Corrective Actions
Request Corrective Actions (SCARs) from suppliers using the 8D process. Work together with suppliers to resolve problems and prevent recurrence. Ensure all 8D sections are filled-out, supplier actions are completed and effectiveness is verified prior to closing out the corrective action.
12 Complaints
Record and track product failures or deficiencies reported by field service teams and customers. Track reported issues from initial complaint through Investigation (Review of Device /Lot History Record, Failure Analysis), Risk Assessment, Containment, Corrective Action, and Preventive Action. Assign and track actions
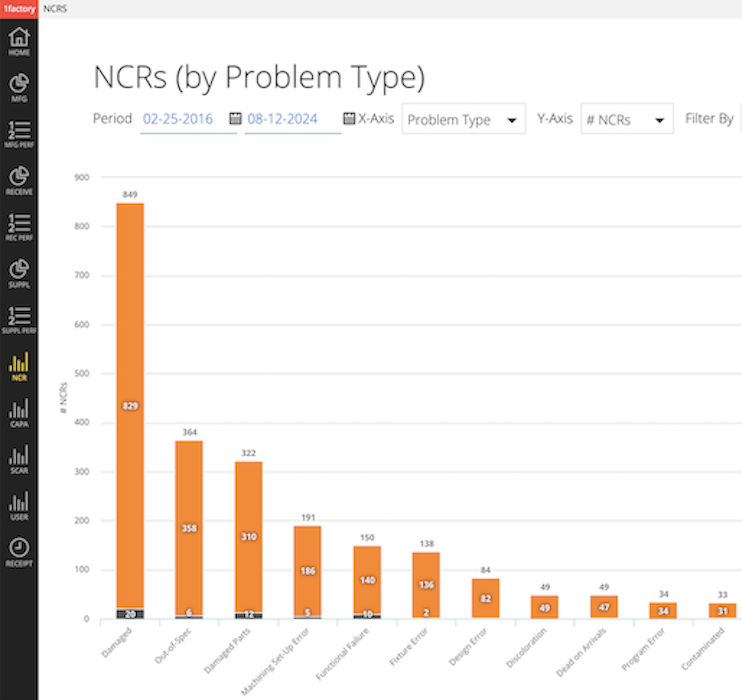
13 Audit Findings
Manage audit findings and associated tasks. Ensure compliance and readiness for customer or regulatory audits. Support a continuous improvement culture by enabling team-members to log and track business process improvement actions.
14 Quality Matrix / Dashboard
Get a birds-eye view of your QMS and audit-readiness with the Quality Management Software (QMS Software) Dashboard. View a hierarchical view of Standards, Requirements and associated Procedures. Simplify audit-prep by ensuring all documents up-to-date and all required training is complete.
15 QMS Analytics & Reporting
Easily pareto non-conformances, CAPAs, SCARs and Complaints by part number, type, supplier, detected at, caused by and other fields. Deliver CAPAs and Suppliers electronically within 1factory to connected Customers and Suppliers or email CAPAs and SCARs to customers and suppliers.
16 QMS Deployment and Go-Live
1factory has the fastest QMS Software deployment time on the market. With 1factory's powerful onboarding tools, you can go-live within a week. In comparison, other Quality Management Software (QMS) systems will take months or even years to deploy.
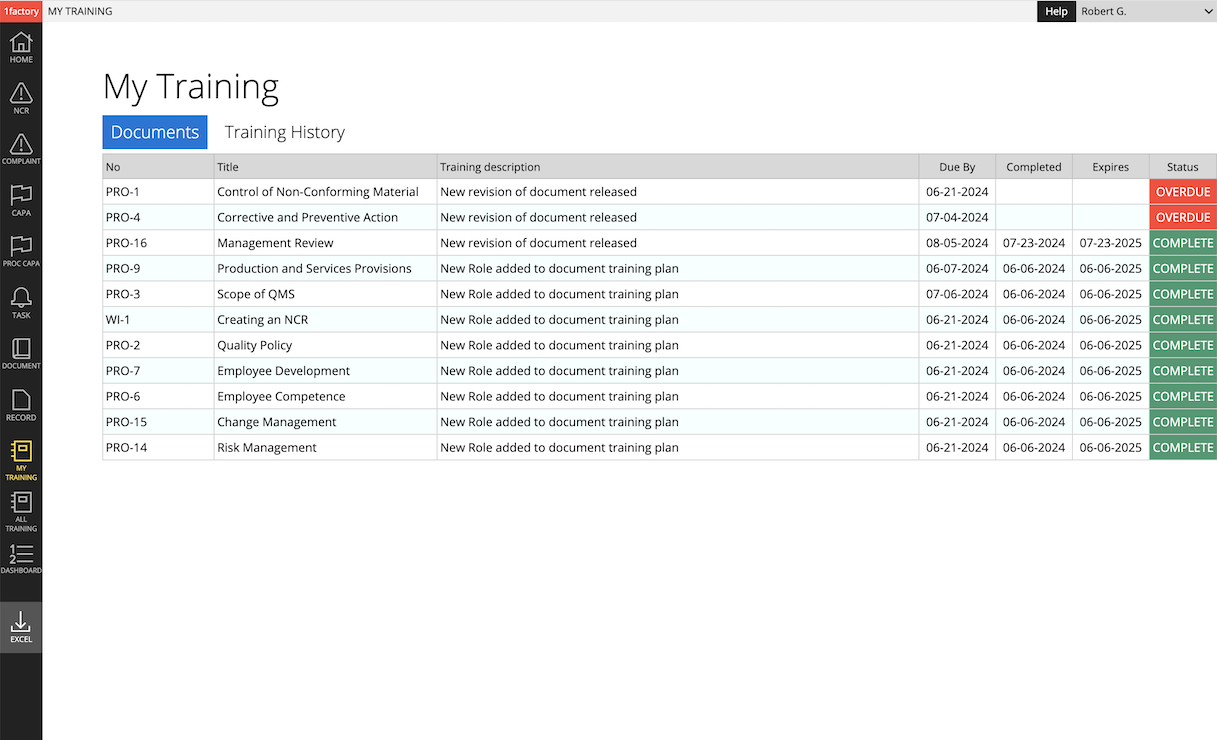
EASY TO USE. LIGHTNING FAST.
INTUITIVE DESIGN
1factory is designed for the front line of quality control with design inputs and ideas from our users. 1factory's intuitive navigation and best-in-class screen-designs make training a breeze. Training and full-deployment takes under two hours with no disruption to operations.
LIGHTNING FAST SPEED
1factory is engineered to be lightning-fast. We serve customers all over the world 24 hours a day, 7 seven days a week, 365 days a year. Our customers in United States, Mexico, Canada, Israel, China, South Africa, Denmark, UK, India, Malaysia, Taiwan all enjoy lightning-fast data collection and powerful real-time analytics.
SECURE AND RELIABLE
SECURITY
1factory is hosted on AWS GovCloud. The AWS GovCloud service is an isolated Amazon region designed to host sensitive data and regulated workloads, including International Traffic in Arms Regulations (ITAR) data.
All customer data transfer from client to server is encrypted over standard HTTPS/TLS 1.2, using a certificate with 2048-bit RSA public key / SHA-256 with RSA encryption. All customer data is encrypted at rest. Data (e.g. Part Numbers, Measurements etc.) are stored in an encrypted Amazon RDS instance. Drawings, Raw Material Certificates etc. are stored on encrypted Elastic Block Storage (EBS) volumes. Drawings and other documents may be additionally encrypted with individual encryption keys.
1factory complies with all NIST-800-171 requirements. 1factory also maintains a SOC2 Type 2 certification, and a copy is available upon request.
RELIABILITY
1factory has been engineered to be highly reliable, scalable and available. Over 200 million parts have been inspected with 1factory by customers in 26 countries.
1factory has delivered an uptime of >99.99% over the last 8 years. We use a third-party service to monitor system uptime, and our customers can view our uptime and availability metrics in real time.
1factory backs-up database with a daily snapshot. Files are stored on redundant hard-drives and backed up via daily snapshots.
500+ CUSTOMERS. 25+ COUNTRIES. 20+ INDUSTRIES.
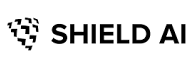
AEROSPACE & DEFENSE

AEROSPACE MACHINING
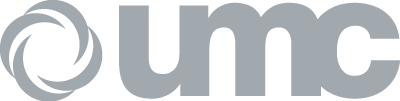
PRECISION MACHINING
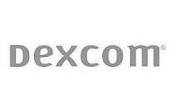
MEDICAL DEVICES
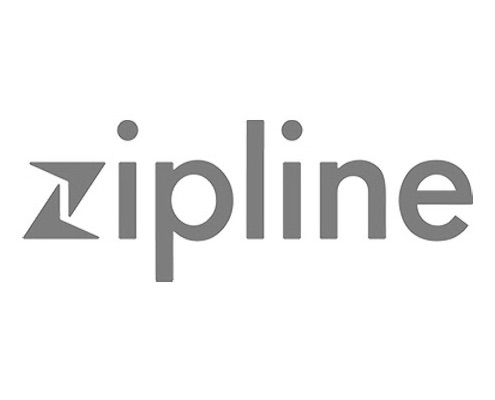
AUTONOMOUS AIRCRAFT
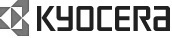
ADVANCED CERAMICS