Complete Guide to Digital Thread: From Design through Service
Table of Contents
- Introduction: Understanding the Digital Thread
- What Is a Digital Thread?
- Digital Thread Across the Product Lifecycle
- Case Study: Digital Thread in Root Cause Analysis
- The Incident: Engine Failure Investigation
- Following the Digital Thread
- The Manufacturing Error
- Preventing Future Disasters
- Strategic Benefits and ROI
1. Introduction: Understanding the Digital Thread
In today's complex manufacturing environment, products involve thousands of components, multiple suppliers, sophisticated manufacturing processes, and decades of operational service. Traditional approaches to managing product information—scattered across disconnected systems, paper records, and tribal knowledge—can no longer support the traceability and analysis requirements of modern engineering.
The Digital Thread represents a fundamental transformation in how organizations manage product information throughout the entire product lifecycle. Rather than treating design, manufacturing, and service data as separate domains, the digital thread creates an integrated framework that connects every piece of product information from initial concept through final retirement.
This connected approach to product data management enables unprecedented capabilities in quality management, root cause analysis, predictive maintenance, and continuous improvement. When quality issues arise, organizations with robust digital threads can quickly trace problems back to their sources, identify other potentially affected products, and implement targeted solutions that prevent recurrence.
The strategic importance of digital thread capabilities has never been greater. As products become more complex and supply chains more distributed, the ability to maintain complete traceability becomes a competitive advantage that directly impacts product quality, customer satisfaction, and regulatory compliance.
This guide explores how leading organizations implement digital thread capabilities to transform product development, manufacturing, and service operations while delivering measurable improvements in quality, efficiency, and customer satisfaction.
2. What Is a Digital Thread?
A digital thread is a comprehensive framework that integrates product data across its entire lifecycle—from initial design concepts through manufacturing, service, and eventual retirement. This connected data framework creates an unbroken chain of information that accelerates product development, improves operational performance, and enables rapid resolution of quality issues through complete traceability.
Core Components of the Digital Thread
The digital thread encompasses four critical domains of product information that traditionally exist in isolation but deliver exponential value when integrated:
Design and Engineering Data includes CAD models, engineering specifications, material selections, performance requirements, simulation results, and design validation testing. This domain establishes the product definition and performance targets that guide all subsequent activities.
Manufacturing Information encompasses process plans, machine programming, quality control procedures, actual production parameters, inspection results, and supplier documentation. This domain captures how products are actually produced and verified.
Service and Maintenance Records include installation documentation, operational performance data, maintenance activities, repair procedures, component replacements, and field failure analysis. This domain tracks actual product performance in customer applications.
Quality and Compliance Documentation spans regulatory approvals, certification testing, audit trails, nonconformance reports, corrective actions, and continuous improvement initiatives. This domain ensures that products meet all applicable requirements throughout their lifecycle.
The Integration Challenge
Traditional product development and manufacturing processes create information silos where each domain operates independently. Design teams work in CAD systems, manufacturing teams use ERP and MES platforms, service teams maintain separate maintenance management systems, and quality teams track issues in disconnected databases.
This fragmentation creates significant challenges when problems arise. Root cause analysis becomes time-consuming detective work as teams struggle to correlate information across multiple systems. Impact assessment is difficult because it's unclear which other products might be affected by similar issues. Continuous improvement efforts are hampered by the inability to identify patterns and trends across the complete product lifecycle.
The digital thread solves these challenges by creating seamless connections between all product information domains, enabling rapid navigation from any data point to related information across the entire product lifecycle.
3. Digital Thread Across the Product Lifecycle
To understand how the digital thread creates value in practice, let's follow a critical aerospace component—a hydraulic manifold used in aircraft and helicopters—through its complete lifecycle. This example demonstrates how integrated data management transforms each phase of product development and service while building the comprehensive traceability that enables rapid problem resolution.
In aerospace applications, hydraulic manifolds direct high-pressure fluid through precision-machined internal passages to control critical aircraft functions including landing gear, flight controls, thrust reversers, and engine actuation. Component failure risks catastrophic consequences, making complete data traceability not just valuable but essential for safety and regulatory compliance.
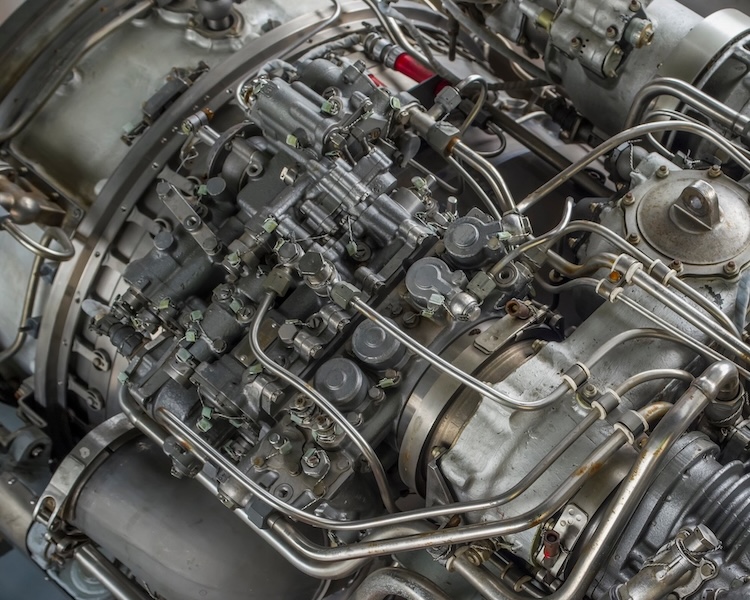
3.1 Design and Requirements Phase
The digital thread begins with comprehensive requirements definition that establishes verifiable targets for all subsequent development and manufacturing activities. For aerospace hydraulic manifolds, these requirements include specific operating pressures (typically 3,000-5,000 psi), flow rates, temperature ranges (-65°F to +275°F), weight constraints, space limitations, reliability targets (failure rates below 10^-9 per flight hour), and environmental considerations.
These requirements drive material selection decisions that become permanent parts of the digital thread. Aluminum alloys (6061-T6, 7075-T6) are selected for lightweight applications, stainless steel (303, 304, 316) for high-temperature environments, or titanium alloys for specialized applications. The digital thread maintains complete material certification, composition analysis, heat treatment verification, and mechanical property testing results that support both manufacturing and long-term service decisions.
Design Development and Validation
Engineers create detailed 3D CAD models with precise port specifications including thread standards, surface finishes, and tolerances. Internal passage geometry is optimized for hydraulic performance, with each port serving specific functions: primary pressure supply ports handle maximum pressure, return ports direct fluid back to reservoirs, and servo control ports manage actuator pressure. The digital model captures these details with complete geometric dimensioning and tolerancing that guides manufacturing and inspection activities.
Before any physical manufacturing begins, digital simulations verify hydraulic performance by analyzing pressure drops (target: <50 psi at full flow), flow velocities (target: <25 ft/sec), turbulence factors, cavitation risks, and thermal expansion effects. These simulations often reveal optimization opportunities such as rounding internal corners to reduce pressure drops or adjusting passage diameters for balanced flow. All simulation results become part of the digital thread, providing performance baselines for comparison against actual service data.
3.2 Manufacturing and Production Phase
Manufacturing engineers develop detailed process plans that translate design requirements into specific production activities. These plans include machine tool selection for required accuracy (±0.001"), fixturing design to maintain datum references, and statistical process control parameters. The typical production sequence includes raw material procurement, initial machining, primary drilling, cross-drilling, threading, deburring, surface treatments, and inspection—with the digital thread maintaining links between each operation and original design requirements.
Advanced Manufacturing Integration
Production employs specialized equipment including 5-axis CNC machining for complex port angles, deep-hole drilling equipment, and specialized deburring tools. Modern manufacturing systems feed real-time data back to the digital thread including actual machining parameters, tool wear measurements, vibration signatures, and dimensional accuracy trends.
Computer-Aided Manufacturing (CAM) programming transforms 3D CAD models into precise digital instructions for CNC machinery. For hydraulic manifolds with complex internal passages, CAM engineers create sophisticated toolpaths that accommodate multi-axis movements while avoiding collisions and ensuring optimal surface finishes. The programming includes detailed drilling sequences with specific depths for intersecting passages, specialized tool selection for different operations, and precisely calculated cutting speeds and feeds based on material properties.
Advanced CAM systems simulate the entire machining process before any physical cutting begins, verifying tool clearances and identifying potential issues. For aerospace components, these simulations must account for fixture designs that maintain critical datums through multiple setups while providing rigid workholding to prevent part movement that could lead to defects. The resulting NC code becomes part of the digital thread, linking manufacturing instructions directly to design intent and enabling traceability of specific machining parameters to individual component features.
Quality Control and Verification
Aerospace hydraulic components undergo rigorous cleaning and treatment including multi-stage ultrasonic cleaning, chemical degreasing, material-specific surface treatments (passivation for stainless steel, anodizing for aluminum), and application of thread sealants. Process parameters become part of the digital thread, ensuring consistency across production batches.
Comprehensive verification includes coordinate measuring machine (CMM) inspection, borescope examination of internal passages, pressure decay testing, helium leak testing, and non-destructive evaluation. Functional testing subjects components to proof pressure (typically 1.5× operating pressure), flow rate verification, vibration testing, and temperature cycling. All results feed into the digital thread, establishing baseline performance profiles that support both immediate quality decisions and long-term trend analysis.
3.3 Service and Maintenance Phase
As hydraulic manifolds integrate into aircraft systems, the digital thread captures critical assembly data including fitting torque values, seal certifications, and initial system pressure checks. The connected nature of this data framework streamlines regulatory approval by providing complete traceability from design through manufacturing to final testing and installation.
Operational Data Integration
Once installed, the digital thread continues expanding with operational data including installation records, ground tests, flight performance data, and maintenance inspections. Modern aircraft health monitoring systems track hydraulic system parameters during flight, comparing actual performance against original design predictions and identifying trends that may indicate developing issues.
Throughout service life, maintenance activities continuously enrich the digital history with inspection results, fluid analysis, part replacements, and repair procedures. This operational data provides valuable feedback to design and manufacturing teams, revealing how components actually perform in service compared to original predictions.
End-of-Life Analysis and Continuous Improvement
When components reach retirement, engineers analyze complete service life data including wear patterns, maintenance history, and failure modes to improve future designs. This analysis closes the loop in the digital thread, ensuring that lessons learned from field service are incorporated into next-generation product development.
The digital thread for aerospace hydraulic manifolds represents sophisticated data integration spanning design, manufacturing, certification, operation, and retirement. This unbroken chain of information ensures safety and reliability while enabling continuous improvement through data-driven insights that would be impossible without comprehensive lifecycle traceability.
4. Case Study: Digital Thread in Root Cause Analysis
The true value of digital thread capabilities becomes most apparent during crisis situations when rapid root cause analysis can mean the difference between isolated incidents and widespread safety risks. This case study examines how comprehensive lifecycle data integration enabled investigators to quickly identify the source of a catastrophic engine failure and prevent similar incidents across an entire fleet.
4.1 The Incident: Engine Failure Investigation
An Airbus aircraft taking off from Singapore experienced a catastrophic engine failure that could have ended in tragedy. The engine caught fire, hydraulic systems were damaged, and engine parts fell onto buildings below. Fortunately, the pilots managed to return the aircraft safely to the airport, and no one was injured.
What happened next demonstrates the critical importance of maintaining comprehensive digital thread capabilities across the aerospace supply chain. The investigation required rapid analysis of interconnected data across four critical domains to determine whether this was an isolated incident or a systemic problem affecting other aircraft.
The Investigation Challenge
When aircraft incidents occur, investigators must quickly determine the root cause to assess broader fleet risk. The failure could have originated from multiple sources: operational factors such as bird strikes or weather conditions, maintenance issues including improper service or missed inspections, manufacturing defects from production errors, or design flaws from engineering miscalculations.
Only by understanding the true cause can investigators determine if other aircraft might be at risk and implement appropriate safety measures. This particular investigation demonstrates how digital thread capabilities accelerate root cause analysis by providing seamless access to integrated lifecycle data.
4.2 Following the Digital Thread
The investigation team systematically examined data across all four domains of the digital thread, using integrated information to rapidly narrow the scope of potential causes and identify the actual failure mechanism.
Flight Data Analysis
Investigators began by examining data from the flight data recorder and cockpit voice recordings. When the failure occurred, multiple warning systems activated in the cockpit, particularly alerts about the green hydraulic system—one of three independent systems powering critical flight controls. The pilots followed established procedures perfectly, stabilizing the aircraft and making a safe emergency landing.
The flight data showed no external cause for the failure. There were no bird strikes, unusual weather conditions, or pilot errors that could explain the catastrophic engine failure. This analysis eliminated operational factors and pointed investigators toward other domains in the digital thread.
Maintenance Record Examination
Following the digital thread to maintenance records, investigators found that all required servicing had been performed according to schedule. Maintenance teams had followed established procedures, and there were no anomalies in previous inspections that would have indicated an imminent failure. The maintenance history was comprehensive and compliant, eliminating maintenance-related causes.
Design Review and Analysis
Investigators accessed original CAD models and engineering specifications for the hydraulic components and related engine parts. They found that the design itself met all required safety standards and had passed all simulation tests during development. The engineering analysis showed no design flaws that could explain the failure, pointing investigators toward the final domain in the digital thread.
Manufacturing Analysis: Finding the Root Cause
Finally, the investigation team examined manufacturing records and discovered the source of the failure: oil pipes within the engine had been improperly manufactured. The critical failure point was in a "stub pipe"—a short pipe that carried lubricating oil to a bearing in the engine.
The manufacturing records revealed that the pipe had been machined incorrectly, creating an uneven wall thickness where the internal circumference was not concentric with the external circumference. This resulted in one side being appropriately thick (1.42 mm) while the opposite side was dangerously thin (just 0.35 mm).
4.3 The Manufacturing Error
Detailed analysis of the manufacturing data revealed the exact sequence of events that led to the defect. During a process called counter-boring, the fixture holding the pipe—the "hub"—shifted slightly during machining. This tiny movement during precision drilling created a critical problem: the inner diameter of the hole and the outer diameter were no longer perfectly concentric, creating dramatically uneven wall thickness.
The Failure Cascade
This seemingly minor manufacturing flaw initiated a catastrophic sequence of events:
- The thin section developed a fatigue crack under normal operational stress
- This crack allowed oil to leak into an internal space with extremely high temperatures (365°C/689°F)
- The oil atomized under pressure and ignited, creating an intense fire
- The resulting fire heated the turbine driveshaft to the point of structural failure
- Engine components separated, rupturing the engine casing and damaging hydraulic systems
The manufacturing defect had escaped detection during quality control inspections because the external appearance of the component was normal. Only when investigators could access complete manufacturing process data through the digital thread was the root cause obvious.
4.4 Preventing Future Disasters
What made this incident particularly significant was how digital thread capabilities enabled rapid identification of other potentially affected components. By following the digital thread back to manufacturing records, investigators were able to identify the specific production batch and machining parameters associated with the defective component.
Fleet-Wide Risk Assessment
Using integrated manufacturing data, investigators quickly identified three additional engines with components from the same production batch that exhibited similar machining anomalies. These engines were immediately removed from service, potentially preventing additional catastrophic failures before they could occur.
Without comprehensive digital thread capabilities connecting flight data, maintenance records, design specifications, and manufacturing processes, identifying the root cause and locating other vulnerable engines would have been far more difficult and time-consuming—perhaps impossible before another incident occurred.
Systemic Improvements
The investigation led to immediate improvements in manufacturing processes, including enhanced fixture design, improved quality control procedures, and better inspection techniques for detecting concentricity issues. These improvements were implemented across the entire supply chain, preventing similar defects in future production.
The case demonstrates how digital thread capabilities transform isolated incidents into opportunities for systemic improvement. By maintaining comprehensive traceability from design through service, organizations can not only resolve individual problems quickly but also identify and eliminate underlying causes that could affect other products.
5. Strategic Benefits and ROI
Digital thread implementation delivers measurable benefits across multiple dimensions of business performance while creating strategic capabilities that become increasingly valuable as product complexity grows and customer expectations evolve. Organizations that successfully implement comprehensive digital thread capabilities report significant improvements in product quality, development efficiency, and customer satisfaction.
Quality and Risk Management
The most immediate and measurable benefits of digital thread implementation appear in quality and risk management capabilities. Complete traceability enables rapid root cause analysis that reduces problem resolution time by 60-80% compared to traditional approaches. When quality issues arise, integrated data allows teams to quickly identify affected products, assess impact scope, and implement targeted corrective actions.
Predictive quality capabilities emerge from the ability to correlate design, manufacturing, and service data over time. Organizations can identify patterns that predict potential failures before they occur, enabling proactive maintenance and component replacement that prevents customer-impacting incidents.
Development Efficiency and Innovation
Digital thread capabilities significantly accelerate product development by providing designers with immediate access to manufacturing constraints, service performance data, and lessons learned from previous products. This integrated view enables more informed design decisions that reduce development cycles while improving product performance and manufacturability.
Real-world performance data from field service feeds back into design processes, enabling continuous improvement that would be impossible without comprehensive lifecycle traceability. Design teams can see exactly how their products perform in customer applications and use this insight to optimize future designs.
Operational Excellence
Manufacturing operations benefit from integrated access to design intent, quality requirements, and service feedback. Production teams can make more informed decisions about process optimization while quality teams can implement more effective inspection strategies based on field performance data.
Service operations gain unprecedented insight into product behavior and maintenance requirements, enabling more effective maintenance planning and improved customer support. Complete component history supports better spare parts management and more accurate service life predictions.
Customer Satisfaction and Competitive Advantage
Digital thread capabilities enable organizations to provide superior customer support through complete product knowledge and rapid problem resolution. When issues arise, service teams have immediate access to complete product history, enabling faster diagnosis and more effective solutions.
Proactive customer communication based on predictive analytics builds trust and loyalty while reducing unplanned downtime. Customers appreciate being informed about potential issues before they impact operations, and proactive maintenance recommendations demonstrate ongoing commitment to product performance.
Return on Investment
Organizations implementing comprehensive digital thread capabilities typically achieve return on investment within 18-24 months through reduced quality costs, faster problem resolution, improved development efficiency, and enhanced customer satisfaction. The benefits compound over time as organizations build more comprehensive data assets and develop more sophisticated analytical capabilities.
The strategic value of digital thread capabilities continues growing as products become more complex and customer expectations evolve. Organizations that establish comprehensive lifecycle traceability today position themselves for success in an increasingly connected and data-driven business environment.
Digital thread implementation represents a fundamental transformation in how organizations manage product information and customer relationships. By connecting design, manufacturing, and service data into integrated frameworks, organizations create capabilities that deliver immediate operational benefits while building the foundation for future innovation and competitive advantage.
1Factory's Manufacturing Quality, Incoming Quality and Supplier Quality modules serve as critical enablers of the digital thread by capturing comprehensive quality control data at every step of the manufacturing process across the supply chain. From incoming inspection through final shipment, these integrated systems create the unbroken chain of quality data that transforms design intent into manufacturing reality while maintaining complete traceability from raw materials to customer delivery—the foundation upon which all effective digital threads are built.