First Article Inspection (FAI) - A Guide
01. What is a First Article Inspection (FAI)?
A First Article Inspection (FAI) is a business process that determines whether the manufacturing process for a part is capable of consistently delivering parts that conform to specifications.
A First Article is a comprehensive review of the engineering documentation and the manufacturing process from raw materials through conversion (machining, molding, casting etc.), special processing (anodization, plating, hardening etc.) and all the way through functional testing for one part.
A First Article is important for both the buyer and the supplier (manufacturer) of a part.
For the supplier, an FAI is an opportunity to evaluate the manufacturability of a part, ensure completeness of the design documentation, identify design errors, recommend design changes to improve manufacturability, and establish the manufacturing process and supply chain for the part.
For the buyer, an FAI is an opportunity to confirm that the design requirements have been understood, and that the supplier's manufacturing process, external special processing steps, and functional testing are indeed capable of consistently delivering good parts.
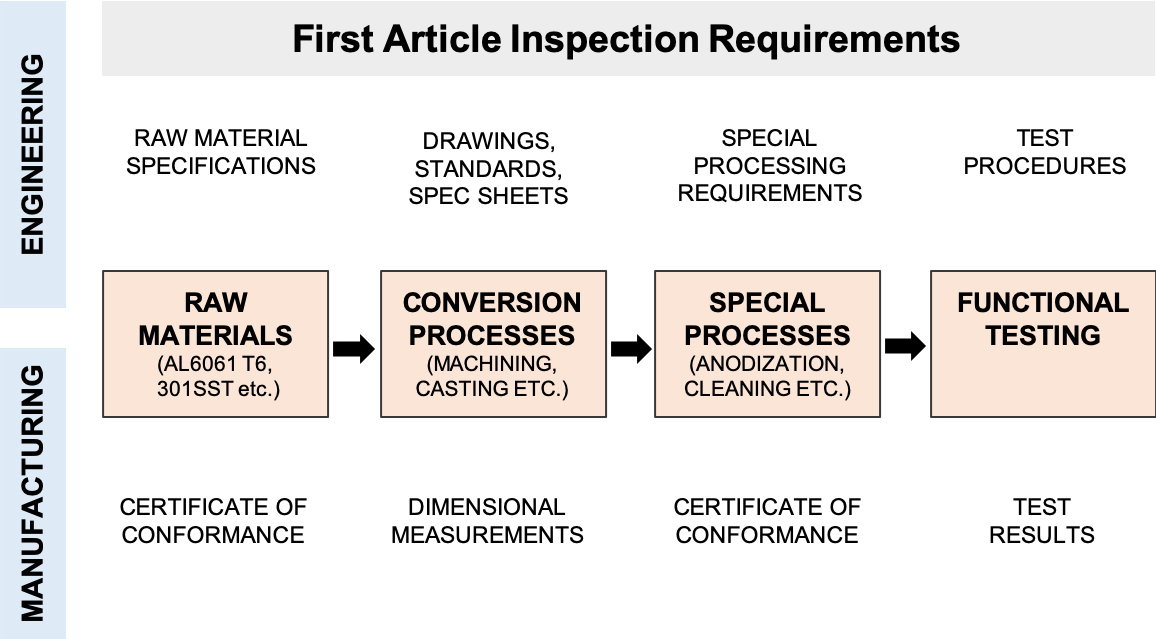
02. When is a First Article Inspection needed?
A First Article inspection is required during the new product introduction process to ensure that the manufacturing process is capable of consistently delivering products that meet specifications.
An FAI will typically evaluate one part with the important unwritten assumption that every subsequent part will follow the exact same manufacturing process, and the process will therefore consistently deliver good parts.
Any change in the part's design or in the manufacturing process violates this assumption, and therefore requires a new First Article Inspection. Here's a partial list of conditions or events that will trigger a new first article:
- New Product Introduction
- Design Change (new Part Number or Revision)
- Manufacturing Process Change
- Outside Processing Vendor Change
- A Factory Move
- Resuming Production After a Long Gap
Some of these changes require a complete new first article inspection. For example, a change in manufacturing process from 4-axis CNC to a swiss screw lathe, will require a complete new First Article Inspection. Similarly, a change from laser cutting to stamping will also require a complete new first article inspection.
A more localized change, to a powder coating process for example, or a change to the packaging of part, may not require a full first article. Instead, a partial first article may be sufficient.
03. Industry & Customer-Specific Reports
There are a number of industry-standard, and customer-specific First Article Inspection Report formats. These reports are identical in intent, but may vary greatly in layout and format.
For example, every First Article Inspection report requires a dimensional record. Most require a Gage ID against each measurement. And a subset further requires a Calibration Due Date for each Gage ID.
A FAI report will typically contain the following documentation:
- Design Records (Drawings, Bill of Material etc)
- Raw Material Records
- A Ballooned Drawing
- Dimensional Inspection report
- Measurement System Traceability
- Special Processing Certs
- Functional Test Results
04. What is the difference between a PPAP and an FAI?
A First Article inspection is a subset of a Production Part Approval Process (PPAP). There are therefore some significant differences:
- Unlike a full PPAP which typically requires the production of tens to hundreds of parts for run-at-rate and process capability studies, an FAI requires the inspection of only one part (in some cases three to five parts).
- A PPAP requires formalized documentation for every step of the new product introduction process, including Quality Control Plans, PFMEAs, Process Flow Diagrams, Gage R&R etc. In contrast, an FAI focuses on the dimensional record and a subset of the documentation: raw materials, special processing, and functional testing .
Companies that select the First Article process assume (often incorrectly) that their suppliers have Quality Control Plans in place, and that these quality control plans are actually being used.
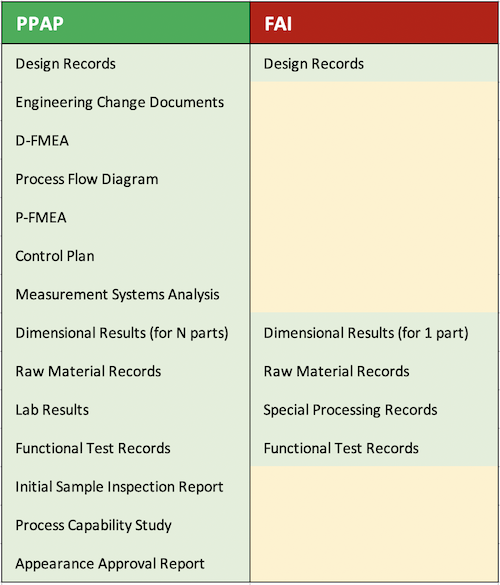
05. The Raw Material Record
The buyer will provide a raw material specification (e.g. AL6061 T6, 301SST etc.) and a reference standard. The supplier, in turn, must provide proof that the raw material used for the first article meets this specification.
This proof is provided in terms of a certificate of conformance (CoC) provided by the mill along with traceability information such as a Heat Lot number. The CoC will typically contain:
- The Mill Name
- Material Grade
- ASTM Standard Number
- Material Form and Dimensions
- Heat Lot Number
- Quantity Covered by the Report
- Actual Chemical Composition
- Mechanical Test Results
- Country of Origin
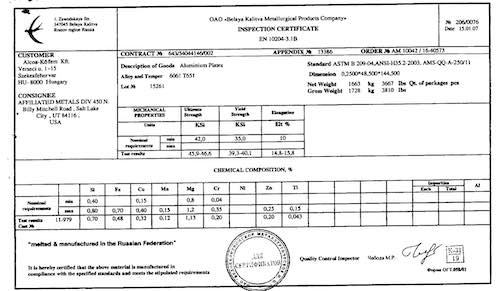
06. The Dimensional Record
The dimensional record will include Attribute Specifications (i.e Pass/Fail or Yes/No) such as Part Engraving Checks, and Variable Specifications (i.e. Numeric or Measured Value) such as linear dimensions, diameters, positions etc. Data will be captured by a wide variety of measurement equipment including pin gages, calipers, micrometers, in-circuit testers, CMMs etc.
It is essential the each measurement be traceable to the gage that was used, and to the calibration record of the gage. And, an underlying assumption is that the gage has adequate resolution (typically 1/10th of the tolerance of the feature being measured), and that each measurement is repeatable and reproducible.
Note: The dimensional record by itself (without the raw material record and the special processing and functional testing records) may be meaningless. If you focus solely on the dimensional record, you run the risk of product functional failure.
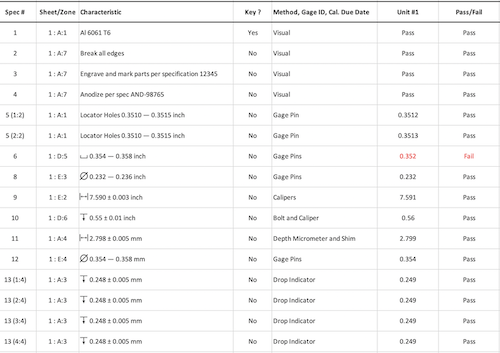
07. AS9102 - First Article Inspection Report
The aerospace industry uses the AS9102 First Article Inspection Report format. This report is divided into three forms:
- Form 1: Part Number Accountability
- Form 2: Product Accountability
- Form 3: Characteristic Accountability
Together, these three forms, provide a complete record of the build process from the Raw Materials and Components used, through Dimensional Measurements, Special Processing, and Functional Testing.
08. AS9102 - Form 1
Form 1 is described as Part Number Accountability, and achieves three goals:
- Ensure traceability to the engineering change order
- Ensure traceability to the manufacturing process (i.e. work order or job)
- Link the parent FAI to the FAI for each sub-component used
Form 1 defines whether the part being inspected is an individual component (i.e. a Detail FAI), or an assembly with a Bill of Materials (i.e. an Assembly FAI).
For an Assembly FAI, you must list each of the component part numbers that make up the assembly in Fields 15 and 16. If those components are serialized, include the serial numbers in Field 17. And finally, enter the FAI number for each sub-component in Field 18.
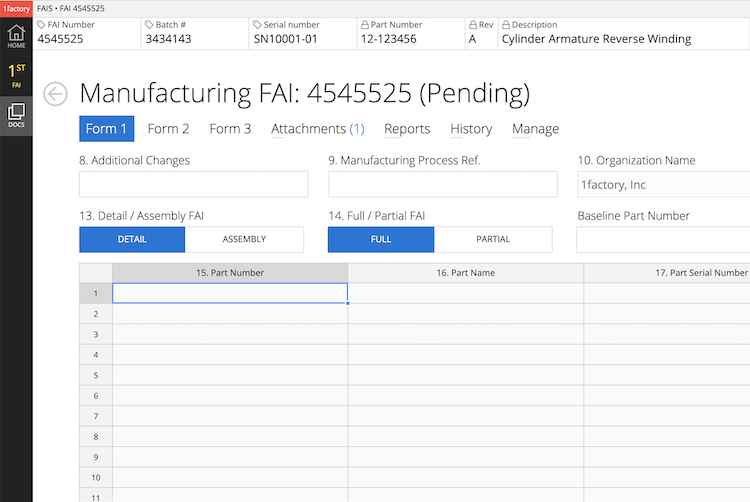
09. AS9102 - Form 2
Form 2 is described as Product Accountability, and has two sub-sections:
- Raw Materials and Special Processing section
- A Functional Testing section.
As an example, your raw materials may include a block of Al6061 T6, a conductive epoxy, and a copper tube. The machined aluminum part may be Hard Anodized Black. You must list each raw material (Al6061 T6, Conductive Epoxy, Copper Tube) and special process (Anodization) in Field 5, and the associated Specification Number in Field 6. If the special process has a customer-defined or industry-standard code, list that in Field 7.
Use Field 8 to list the vendor code assigned to the special processing supplier, and Field 9 to declare whether the special processing supplier requires approval from your customer (this will be dictated by the terms of each individual customer contract or PO.
Functional Test Procedure numbers are recorded in Field 11, and the file number for the test results (i.e. test data and pass/fail acceptance record) are listed in Field 12.
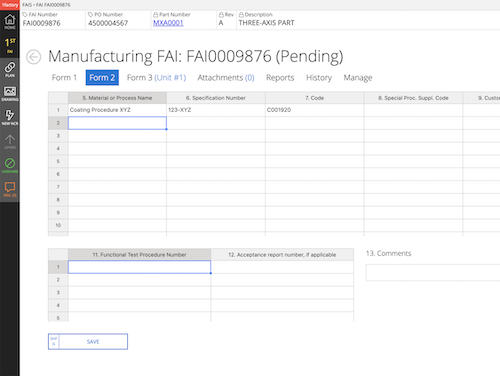
10. AS9102 - Form 3
Form 3 is the Characteristic Accountability form. A part may be defined by hundreds of dimensional, material, special processing and functional parameters. Form 3 ensures that each parameter is listed and accounted for
For each parameter (including notes on drawings), you must provide the characteristic or balloon number, the drawing sheet and zone, a characteristic designator (e.g. critical to quality / key), the specification (i.e. requirements) the measurement and the results (Pass or Fail).
For Attribute specifications, record Yes/No or Pass/Fail. For Variable specifications, record the actual value measured, and whether it Passed or Failed.
In addition, you must record the Inspection Method and Gage ID in the Designed Tooling field to ensure traceability to the measurement system.
Non-conformances or deviations from requirements must be listed under Field 11.
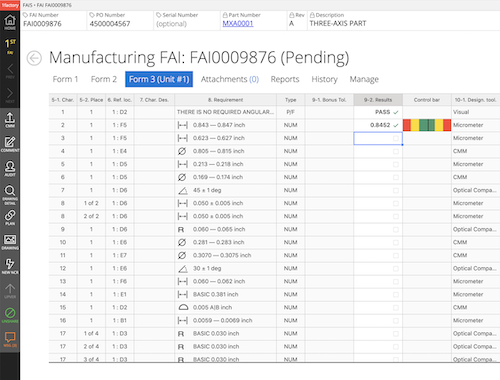
11. First Article Inspection Software
A first article inspection record is a lot more than just the excel report. You must therefore consider the following when selecting First Article Inspection Software:
- Drawing Ballooning: Does the software speed-up drawing ballooning?
- Quality Control Plan Creation: Does the software create a Quality Control Plan that you can use for in-process and final inspections?
- CMM Data Import: Does the software import data from the inspection equipment (CMM, Optical CMM) and test fixtures you use?
- Document / Certificate (CoC) Management: Can the software store and retrieve images and documents including CoCs?
- Linking Sub-Component FAI: Does the software link sub-component FAIs?
- Ease of Record Search and Retrieval: Can you easily find and retrieve FAI records by part number, customer, inspector name, gage ID etc.?
- Data Retention Requirements: Your contract will require data retention for many years, often for the expected service life of the part or the final product it goes into. In the aerospace industry that could be 30 years. For what period of time will your software retain data?
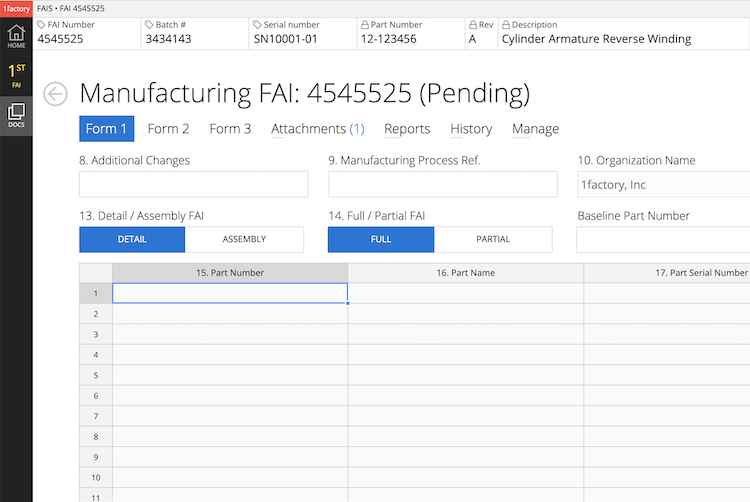
Speeding-up First Articles
1factory's Manufacturing Quality Control and Inspection Management software automates and speeds-up every step of the First Article process from drawing ballooning, to CMM data collection, and reporting, saving hundreds of man-hours each year. Learn More