Guide to Quality Management Systems (QMS)
01. What is a Quality Management System?
Definition: A Quality Management System (QMS) is a formalization of the business processes with which an organization creates and delivers its products and services.
A QMS takes the business processes that may already exist (formally or informally) and puts them into a structured, documented system.
Some companies might have just a few essential processes, while others must coordinate hundreds of interconnected workflows.
A formal QMS becomes increasingly important as business complexity grows, and is absolutely critical in regulated industries where process deviations can have serious consequences.
A QMS ensures four critical elements are in place:
- Documentation: Processes are clearly written and accessible
- Training: Employees understand their roles and responsibilities
- Execution: Staff consistently follow the documented procedures
- Evidence: Records demonstrate compliance and effectiveness
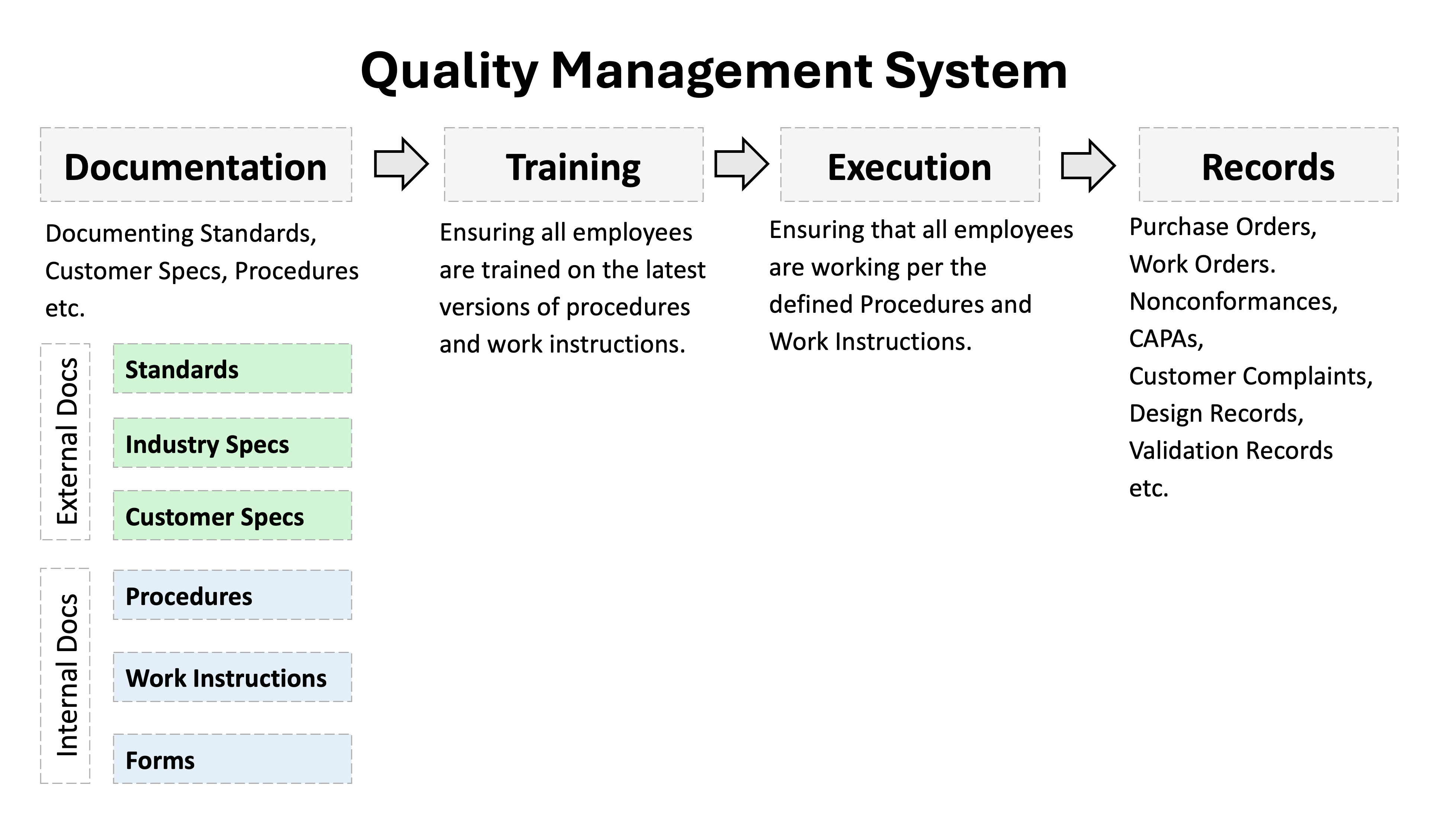
02. Quality Control
Quality Control (QC): Quality Control (QC) is the set of activities involved in ensuring that products meet specified requirements. Quality Control activities occur within the manufacturing environment, and include:
- Quality Planning: Determining what to measure, where to measure it in the manufacturing process, how to measure it (what equipment to use), and the sampling rules (how many pieces from a batch should you check?)
- Mistake Prevention: Building-in mistake proofing mechanisms to prevent defects. As an example, product designs often ensure that a part can only be inserted the right way, preventing accidental incorrect installation.
- Statistical Process Control: Monitoring production processes to detect problems before the result in production defects.
- Inspection: Measuring and/or visually inspecting products to ensure they meet specifications.
- Root Cause Analysis: Determining what may have caused a product defect.
03. Quality Assurance
Quality Assurance: Quality Assurance takes a whole-of-the-organization approach to quality. It is a systematic approach to designing and managing business processes across the organization to consistently deliver products and services that meet customer requirements. Quality Assurance activities include:
- Process Design: Defining and documenting how work should be performed (business processes), including roles, responsibilities, and decision points.
- Training and Competency: Ensuring employees understand their roles and have the necessary skills to perform their work correctly.
- Document Control: Managing procedures, work instructions, and specifications to ensure everyone is working from the current, released versions.
- Execution and Continuous Improvement: Ensuring documented processes are being followed, and systematically addressing problems when they occur by implementing changes to prevent recurrence.
04. Quality Control vs. Quality Assurance
Quality Control is a subset of Quality Assurance. While Quality Control focuses on detecting and preventing defects during manufacturing, Quality Assurance encompasses Quality Control plus all the other business processes that affect quality.
Quality Control asks: "How do we catch defects before they reach customers?" Quality Assurance asks: "How do we design our entire business system so defects rarely occur in the first place?"
Both are essential. You need robust Quality Control to catch problems that do occur, but you also need Quality Assurance to prevent most problems from happening at all. A company with excellent Quality Control but poor Quality Management might consistently catch defects in manufacturing while still struggling with customer complaints due to design flaws, supplier issues, or installation problems.
05. What is a Business Process?
A business process is a set of connected steps that a business follows to get work done. Each step takes what was completed before and adds to it until the job is finished.
As an example, consider a small deli that makes fresh sandwiches daily. To stay in business, it needs enough bread, vegetables, and meats ready each morning. The deli can't simply guess - it needs a reliable system that includes checking what's running low, deciding when to reorder supplies, placing orders with vendors, receiving deliveries, and storing ingredients properly.
All of these connected steps make up the deli's "inventory management business process."
This larger process contains several smaller processes working together: one for checking expiration dates and rotating stock, another for calculating order quantities based on sales patterns, and another for receiving and inspecting deliveries. Each process supports the overall goal of having the right ingredients available when customers want sandwiches.
06. Business Processes - The Source of Defects
Quality problems frequently originate outside the production floor, and as a result, Quality Management must cover all the key business processes involved in creating and delivering products and services.
For example, problems can occur before manufacturing (wrong customer orders, poor product designs, bad materials from suppliers), during manufacturing (untrained workers, broken equipment, poor communication), or after manufacturing (damaged packaging, rough shipping, incorrect installation, poor customer service).
Quality Management ensures that each individual process is designed and operated correctly, and that all these interconnected processes work together to prevent quality problems before they occur.
When something goes wrong with your product or service, the root cause typically falls into one of three categories: the process wasn't followed correctly, the process itself was poorly designed, or the handoff between process steps failed.
This is why Quality Management Systems focus so heavily on documenting processes, training people properly, and ensuring smooth transitions between different parts of the business.
07. Example: Quality Management in a Coffee Shop
Consider a simple coffee shop. Your experience depends on getting your order right, reasonable wait times, and good-tasting coffee. We've all had our orders messed up - you get the wrong drink, the cashier writes down your order incorrectly, the barista forgets an ingredient, or your coffee tastes burnt.
Each of these problems traces back to a process issue: unclear order-taking procedures, inadequate barista training, poor communication between cashier and barista, or inconsistent brewing methods.
A coffee shop's Quality Management System would document these processes clearly, train employees properly, and track performance to prevent these common problems from recurring.

08. Example: Quality Management in Manufacturing
Manufacturing companies face similar challenges but with higher stakes. Consider a company that builds custom machinery for semiconductor manufacturers. Common problems include shipping the wrong configuration, defective components, incorrect labeling, shipping damage, or installation failures.
Each problem traces back to process breakdowns: unclear order specifications, inadequate supplier controls, poor packaging procedures, or insufficient installation training.
A manufacturer's Quality Management System addresses these issues by documenting critical processes, training employees properly, and maintaining records that verify work was completed correctly.
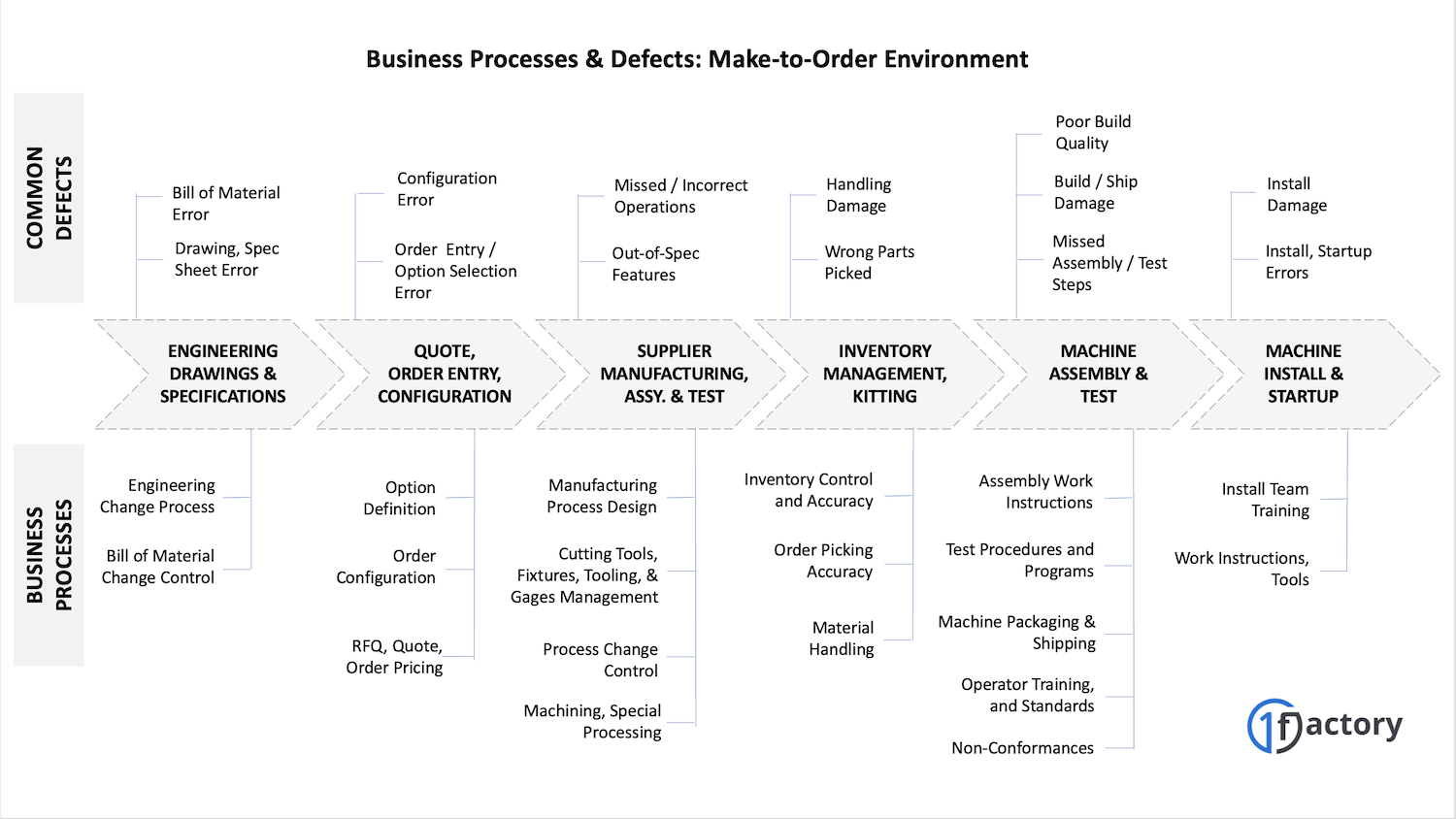
09. Document Hierarchy and Relationships in a QMS
A QMS creates a hierarchy of documentation that connects high-level requirements to day-to-day work:
Standards provide the framework. Organizations choose standards like ISO 9001 (general quality management), ISO 13485 (medical devices), or TS 16949 (automotive) based on their industry and customer requirements.
Each standard contains specific clauses that define what a QMS must address. For example, ISO 9001 Clause 8.5 requires "Control of Production and Service Provision."
Procedures explain how your company meets each clause requirement. For example, your procedure to support Clause 8.5 might be called "Manufacturing Process Control" and would explain your specific approach to controlling production.
Work Instructions provide step-by-step details for specific tasks. While a procedure explains the overall approach to manufacturing control, a work instruction might detail exactly how to set up Machine #3 for Product X, including specific settings, measurements, and safety checks.
Forms and Records capture evidence that work was performed correctly. These might include inspection checklists, calibration records, training certificates, or audit reports that prove your processes are working as intended.
This hierarchy ensures that every requirement in the standard translates into actual work being done correctly and documented properly.
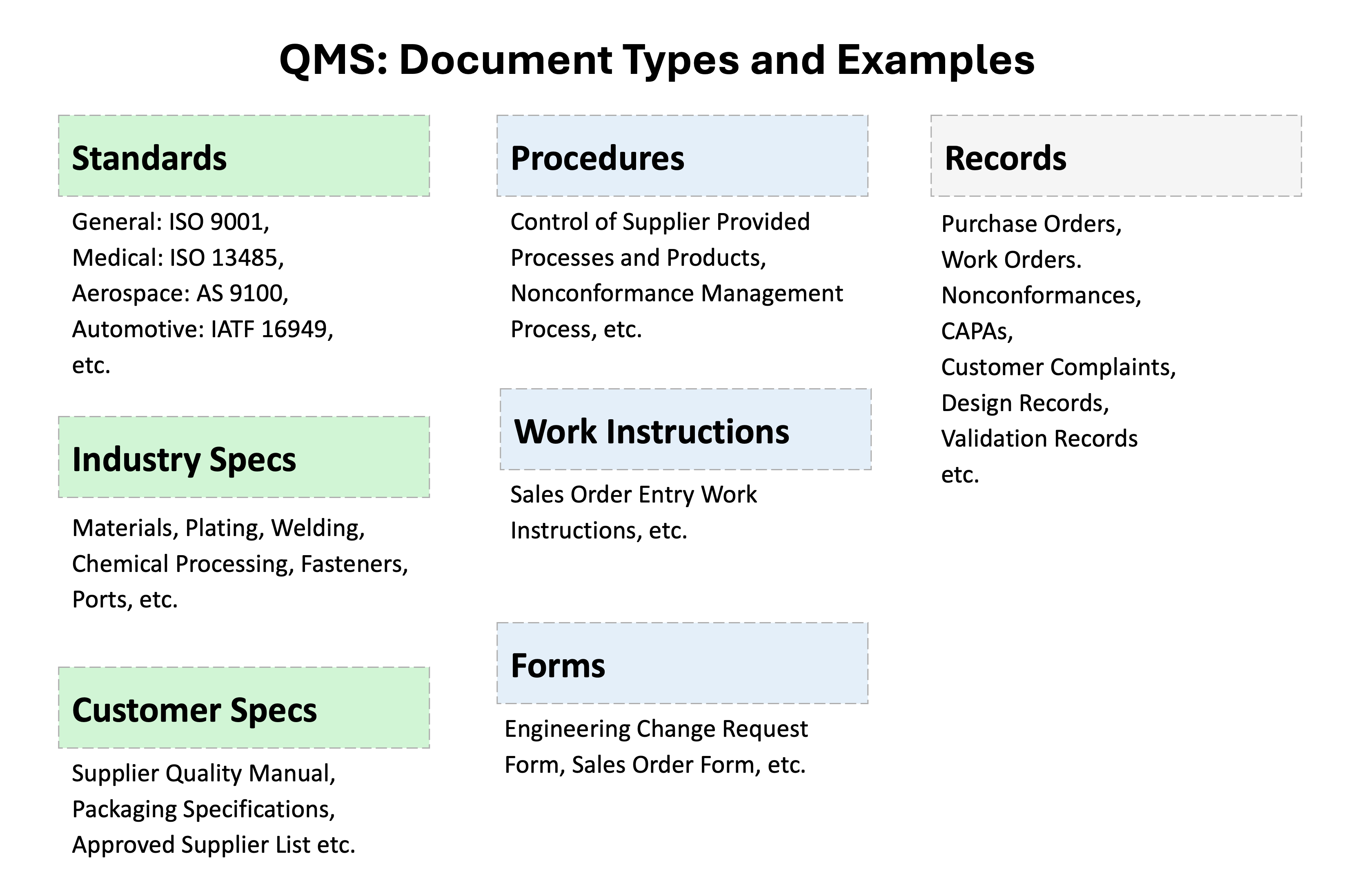
10. Document Control
Document control processes ensure that every employee is working with the correct version of procedures, work instructions, and forms. Document control must also ensure that the required documents are easy to find.
Version Control: Every document maintains a clear revision history showing what changed, who made the changes, when, why, and who approved them. Modern systems provide automated redlining that highlights changes between versions.
Access Control: Role-based permissions ensure people can access appropriate documents while protecting sensitive information. This includes view-only versus edit capabilities and audit trails of document access.
Approval Workflows: Documents are routed to appropriate reviewers, require electronic signatures from authorized approvers, and prevent unapproved documents from being used in production.
Document Relationships: Modern systems link related documents, creating connections between procedures, work instructions, forms, and standards requirements to help users navigate complex quality systems.
11. Training Management
Quality standards require organizations to prove employees are competent for their roles.
Training management ensures everyone has the knowledge and skills to do their jobs effectively and meet quality requirements. This involves determining what training each role needs, delivering training programs, and maintaining records of completed training.
Untrained employees create quality defects, safety incidents, customer service problems, and compliance violations. Well-trained employees work more efficiently, make fewer mistakes, and provide better service.
Training is required when someone is hired, changes jobs, when new procedures are released, when existing procedures are revised, and as part of corrective actions. Training must be documented and verified through testing, skill demonstrations, or peer assessments.
12. Audit Management
The health of a QMS is measured with the help of Audits. Regular audits help identify gaps in the quality system, maintain regulatory compliance, and drive continuous improvement.
An organization may need several types of audits:
- Internal Audits: Audits you conduct on your own processes and procedures.
- Customer Audits: Your customers may audit your facility to ensure you can meet their specific requirements.
- Supplier Audits: You audit your suppliers to ensure they can consistently deliver quality materials and services to you.
- Regulatory Audits: Government agencies like the FDA, FAA, or EPA may audit your facility to ensure compliance with applicable regulations.
- Certification Body Audits: Third-party certification bodies conduct audits to verify that your quality management system meets standards like ISO 9001, AS9100, or ISO 13485.
13. What is an eQMS?
A QMS isn't always a single software system. Instead, it's typically several systems working together to help you create, organize, control, and retrieve the required procedures and records.
For example, your purchasing process might be documented via a procedure in a document control system, the related training may be recorded in a training or human resource management system, while the actual purchasing process may be executed through your ERP system where all the records (quotes, purchase orders, invoices etc.) are created and stored.
An eQMS is a software system that helps create, organize, control and retrieve some or all of the following:
- External Documents: Standards, Customer Specs
- Internal Documents: Procedures, Work Instructions
- Training: Assignment and Tracking
- Evidence: Records

14. Digitizing Your Quality Management System
While you can certainly manage a QMS with paper forms and filing cabinets, modern businesses are moving to eQMS systems (digital QMS systems) for good reasons. These systems address all the requirements we've discussed while delivering dramatic improvements in quality, productivity, and compliance.
Digital QMS systems offer several key benefits:
- Ease of Migration: Simple to bring over your existing procedures, work instructions, and forms without starting from scratch.
- Ease of Implementation: Cloud-based systems can be deployed in less than a day, with full go-live possible within weeks.
- End-User Simplicity: Intuitive interfaces that require minimal training.
- Audit Readiness: Instant access to all the documentation auditors need.
- Scalability: Cloud-based solutions grow with your business without requiring additional infrastructure investments.