Complete Guide to Supplier Quality Management
01. What is a Supply Chain?
A supply chain is a network of interconnected processes through which a company transforms raw materials into finished products for customers.
Modern global supply chains are remarkably extensive networks that can span extraordinary distances and cross multiple international boundaries. A typical complex product like a smartphone or automobile might involve components from 15-30 different countries across 4-6 continents, with raw materials and finished goods traveling a combined distance of 50,000-100,000 miles from initial extraction to final delivery.
These supply chains routinely make multiple ocean crossings - raw materials might travel from mining operations in Africa or South America to processing facilities in Asia, then components travel to assembly plants in China or Southeast Asia, before finished products are shipped across the Pacific to North America or back across the Indian Ocean to Europe and other markets. A single iPhone, for example, includes materials that have collectively crossed the Pacific, Atlantic, and Indian Oceans multiple times during the manufacturing process.
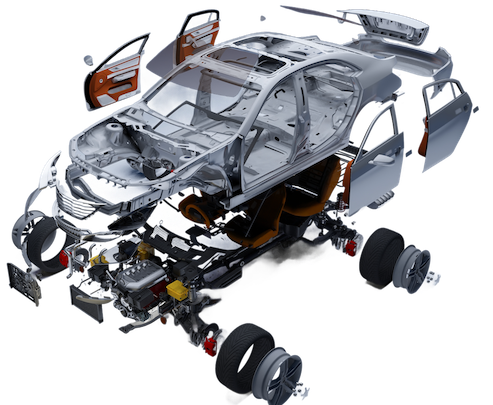
02. Understanding Supply Chain Complexity
Through the early 1990s, supply chains were relatively simple, supporting the mass-production of a limited range of products, with a significant portion of each product being manufactured in-house.
Since then, in response to evolving market conditions, product and supply chain complexity has grown exponentially. Mass-production, in some cases, has been replaced by mass-customization, and in-house manufacturing has been replaced by a multi-tiered, highly-specialized, globally-distributed supply chain.
Supply Chain Complexity is a function of many variables, such as, number of products, number of product variants, number of parts, number of bill of material levels, make vs. buy decisions, number of suppliers, number of supplier tiers, geographic distribution of suppliers, and number of specialized processes.
03. Impact of Complexity on Quality
In this new structure, Tier-0 firms have a limited understanding and almost no visibility into the detailed manufacturing processes through the supply chain, while firms at lower levels on the supply chain have limited visibility to the context in which the final customer uses the product, and as a result may not understand the importance of requested design features.
As supply chain complexity increases, the ability of a firm to control manufacturing processes across the supply chain diminishes. As a result, a large portion of total defects now originate in the supply chain. In fact, there is a direct correlation between supply chain complexity and the number of defects observed in a product.
Supply Chain Complexity is the biggest challenge for supplier quality management, and cannot be handled by simply adding more people to your supplier quality organization. Your business processes and IT systems now need to be transformed to meet this challenge head on!
04. The Supplier Quality Framework
Managing supplier quality across a complex supply chain requires a new framework. At 1factory, we recommend a 7-step approach to ensuring product quality across the supply chain:
1. Foundational Processes: Suppliers must have robust change control processes, equipment maintenance programs, gage calibration programs etc.
2. New Product Introduction Process: Supplier and Buyers must work together to develop a seamless NPI process that ensures product quality issues are ironed out before products make it to volume production.
3. On-Going Production Quality Control: Statistical process control, environmental controls (temperature and humidity), and mistake prevention systems ensure consistent quality during regular production operations.
4. Final Product Inspection: Comprehensive verification processes at suppliers ensure all products meet specifications before shipment, including dimensional, functional, and visual inspection.
5. Verification of Supplier Quality: Multi-layered quality verification including incoming inspection at buyers, and source inspection at suppliers.
6. Real-Time Supplier Monitoring: Continuous visibility into supplier quality data across the supply chain enables proactive issue resolution and performance management.
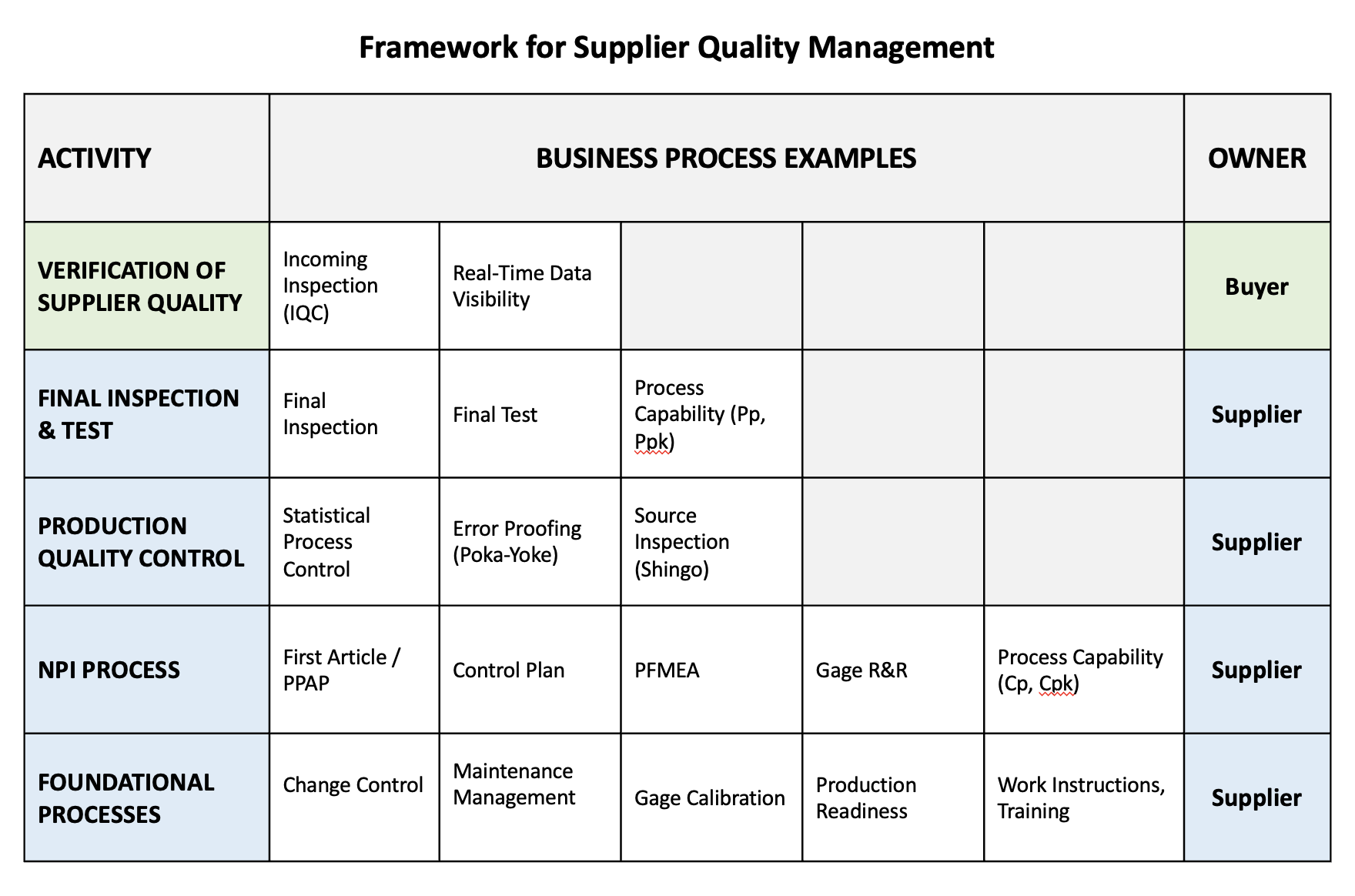
05. Foundational Processes
Robust foundational processes benefit both suppliers and buyers by preventing defects and reducing associated costs. These systems create the stable platform upon which all other quality activities depend.
Change Control Systems: Effective management of engineering changes, document revisions, and process modifications forms the backbone of quality consistency. When you provide a new drawing or revision to suppliers, they must ensure that old drawings, fixtures, CNC programs, and quality control plans are all properly updated.
Preventive Maintenance Programs: Equipment reliability through scheduled maintenance, calibration, and breakdown prevention maintains consistent manufacturing capability.
Production Readiness Verification: Setup verification, first piece inspection, and process parameter validation ensure consistent quality from the first part produced.
Work Instructions and Training: Detailed work instructions with visual aids, critical parameter identification, and quality checkpoints provide clarity for operators and ensure consistent execution.
06. New Product Introduction Process
Robust New Production Introduction (NPI) processes prevent product quality issues from entering the supply chain from the start. First Article Inspection (FAI) and Production Part Approval Process (PPAP) ensure that suppliers understand requirements and can consistently produce parts that meet requirements.
Design Review and Capability Assessment verifies that suppliers understand what you need and have the necessary capabilities to deliver it. This isn't just about equipment - it's about understanding critical characteristics, tolerance requirements, and how the part fits into your larger assembly.
Process Development and Validation ensures that manufacturing processes are robust and capable. Suppliers need to demonstrate not just that they can make good parts, but that their processes are stable enough to make good parts consistently.
Initial Sample Production and Testing provides proof of actual capability under normal production conditions.
07. On-Going Production Quality Control
Statistical Process Control (SPC) helps suppliers understand and control their processes. Control charts provide early warning of process changes. Capability studies identify improvement opportunities, and systematic variation reduction improves consistency.
Environmental Control protects product integrity throughout manufacturing. Temperature control, humidity management, contamination prevention, and proper material handling eliminate many quality issues that result from environmental factors rather than manufacturing processes.
Mistake Prevention systems implement error-proofing techniques and fail-safe mechanisms to prevent defects before they occur.
08. Final Product Verification by Supplier
Suppliers must implement comprehensive final inspection processes to verify that all products meet specifications before shipment. This includes dimensional verification, functional testing, visual inspection, and documentation review to ensure complete traceability and compliance with customer requirements.
09. Verification of Supplier Quality
Quality controls need to remain effective throughout your entire supply network, including sub-tier suppliers that may be invisible to you but critical to overall quality performance.
Incoming Inspection at Buyer serves as your final verification point before supplier materials enter your production process. While the goal is minimizing reliance on incoming inspection through effective supplier quality management, it remains critical for new supplier qualification, risk mitigation, performance monitoring, and change management. Focus resources on the highest-risk suppliers and characteristics while reducing inspection for proven, high-performing suppliers.
Source Inspection at Supplier provides an opportunity to verify product quality before products leave from Tier-2 Suppliers to Tier-1 Suppliers or from Tier-1 Suppliers to Distribution Centers and End Customers.
Real-Time Supplier Monitoring helps you understand and manage quality risks throughout the supply chain. Many quality issues originate at lower tiers where direct oversight is limited - suppliers providing services like cleaning, packaging, heat treatment, and surface finishing that significantly impact final product quality.
10. Supplier Performance Measurement and Monitoring
Effective performance measurement provides objective evaluation of supplier performance while driving accountability and improvement initiatives. This creates the foundation for data-driven supplier management decisions.
Supplier Scorecards evaluate performance across multiple dimensions rather than just quality metrics. Include quality performance (defect rates, first-pass yield, customer complaints), delivery performance (on-time delivery, schedule adherence, lead time consistency), cost management (competitiveness, reduction initiatives, total cost of ownership), responsiveness (communication effectiveness, problem resolution speed), and improvement initiatives (continuous improvement participation, results achieved, innovation contributions).
These scorecards facilitate data-driven discussions, maintain accountability, and identify opportunities for focused improvement efforts. They also help suppliers understand what's important to your business beyond just meeting specifications.
Quality System Audits verify ongoing supplier compliance and identify improvement opportunities through structured audit programs. Each audit cycle should include comprehensive checklists tailored to specific supplier capabilities and risks, pre-audit documentation requirements for efficient time utilization, thorough on-site or virtual audits with experienced quality professionals, and tracking of audit findings and corrective actions to ensure sustained improvement.
Regular audits demonstrate your commitment to quality excellence while helping identify risks and improvement opportunities across your supply base.
11. Corrective Actions & Problem Resolution
When quality issues do occur, having a structured approach to problem resolution builds supplier capabilities while preventing recurrence.
Supplier Corrective Action Process provides a formal framework for addressing quality issues identified in supplier materials or processes. Effective corrective action requests should require:
- Immediate containment actions to prevent defective parts from shipping
- Thorough root cause analysis using structured problem-solving methodologies
- Implementation of permanent solutions that address root causes rather than symptoms
- Verification that corrective actions successfully resolve the issue
- Systemic improvements to prevent similar issues from occurring
This structured approach ensures thorough problem resolution while building supplier problem-solving capabilities that benefit future performance.
12. Supplier Quality vs. Supplier Development
In general, a Supplier Quality team operates at the part-feature or process-parameter level, making corrections and improvements to manufacturing processes and quality control methods to fix and prevent problems. This team ensures that parts coming in from suppliers meet specifications, and that you can continue to ship finished products out to your customers. The payback on these efforts is usually in the short term. Supplier Quality activities are supported by a contractual obligation on the part of the supplier to ensure only conforming parts are shipped.
A Supplier Development team, on the other hand, operates at the organizational or business process level, and focuses on developing the supplier's capabilities, to ensure that both your supplier (on whom you depend) and you, continue to be successful in the long run. Supplier Development may not have a contractual basis, and instead requires a collaborative relationship between buyer and supplier.
13. Building Supplier Capabilities
You do not need to, and nor should you attempt to develop all of your suppliers. Instead, you need to identify the subset of suppliers that makes critical components, and cannot be easily replaced due to a technical or a capital investment barrier.
Key Capability Areas:
Capacity: On-time delivery is a function of capacity, yield, and shop-loading. Many small suppliers view capacity as a function of how many shifts they run, and how many machines they operate, while ignoring efficiency and yield.
Change Control: One of the most common root-causes for defects is inadequate change control at suppliers. When a buyer provides a new drawing or revision, how does the supplier ensure that the old drawing, the old fixtures, the old CNC code, the old quality control plans are all updated?
Inventory Control: Many suppliers do not have robust inventory controls in place. As a consequence, parts are everywhere in the shop, and raw, WIP, and finished products are intermingled.
Sub-tier Supplier Management: Most suppliers can barely get their own quality control work done. When sub-tier suppliers play a critical role, your supplier will need help in developing a sub-tier supplier management process.
14. Alignment & Long-Term View
Alignment of Objectives: Before you can begin a supplier development process, your supplier will need to acknowledge the need for improvement, and commit resources and management support for the project. Your Supplier Development team will also require internal support from your Supply Chain and Sourcing teams.
The Long-Term View: Always take the longer-term view. Don't waste your time worrying about how to split the benefits from the development efforts. Recognize that if your supplier's performance improves, you save money. For example, if the supplier improves quality, his yield improves, and you save money from fewer inspections and fewer defects. Similarly, if your supplier's capacity is freed-up, his on-time delivery to your factories will improve, making your production smoother and more predictable.
15. Automating Supplier Quality Management
1factory's Supplier Quality Management software automates many of the processes described in this guide, including supplier scorecards, real-time monitoring, corrective action tracking, and performance analytics. This automation saves significant time while improving visibility and control across your entire supplier network. Learn More