Selecting and Implementing Quality Control Software: Case Study
The Breaking Point
As a Quality Planning Team Lead for a 500-employee aerospace manufacturing company, I witnessed firsthand how outdated quality control processes can hamper efficiency and growth. Our wake-up call came through employee feedback - both from formal questionnaires and candid conversations. The message was clear: our inspection documentation process was broken.
Our machinists and inspectors painted a vivid picture of the daily struggles. Paper-based documents would disappear into the ether or show up at Final Inspection soaked in machine coolant, rendering them illegible. Even where we had implemented data collection software, users described it as frustratingly slow and rigid. A simple typo meant halting the inspection process to track down someone with the right permissions for a correction.
The Quality Planning team faced its own set of challenges. We were juggling four different software packages just to complete basic tasks. Ballooning drawings, planning jobs, running custom macros, and manually transferring data between systems - what should have been a straightforward process could stretch from a day to over a week for complex parts.
Document control was another nightmare. Users searching for documentation would often encounter multiple revisions of the same part with no clear indication of which was current. It became painfully obvious that while our company had grown substantially, our quality planning and inspection processes were stuck in the past.
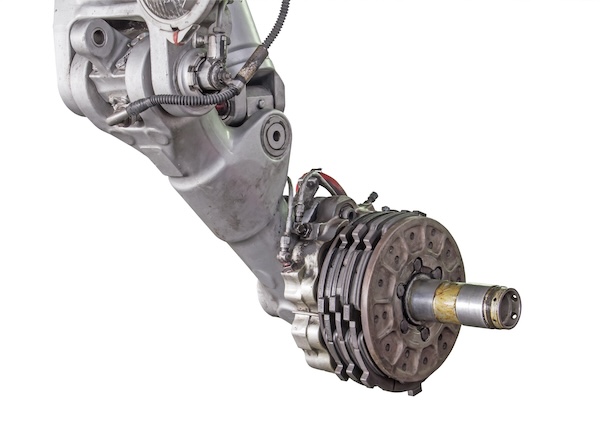
The Digital Imperative
Modern manufacturing moves at a relentless pace. Meeting tight lead times and maintaining competitive costs demands digital solutions. Quality software isn't just a nice-to-have - it's vital to the production process and a long-term investment in organizational success.
This is particularly true in industries like automotive and aerospace, where requirements go beyond dimensional accuracy and visual acceptance. These specifications ensure products are safe, reliable, and perform as designed. The ability to consistently manufacture products meeting these exacting standards isn't just about quality – it's about survival.
Understanding Our Needs
When I began searching for a quality software solution, I knew we needed more than just a band-aid fix. We needed a system that would show immediate results with our existing team, demonstrate clear ROI through improved productivity and error reduction, simplify compliance processes, and scale with our growing company.
Security requirements were non-negotiable. We needed to meet both industry-standard and customer-specific protocols for sensitive data, including ITAR and FedRAMP compliance.
Budget planning required a careful analysis of our current software costs. Which of our existing systems could be replaced with an all-inclusive solution? How much would this free up for investment in new technology?
I knew we needed buy-in from the actual users. I spent time talking with everyone involved in the current process, understanding what worked, what didn't, and what their ideal solution looked like. Together, we created lists of must-have features, nice-to-have capabilities, and things we could live without.
Most importantly, I was fortunate enough to work for a company that recognizes the importance of staying ahead of the curve when it comes to modern manufacturing and quality practices. Without the support of all levels of the leadership team, our hopes of a streamlined quality process would be a pipe dream.
The Search Process
With our requirements clear, I dove into researching available solutions. Looking at both industry leaders and emerging players, we evaluated each option against our criteria:
Fundamental Questions:
- Could it solve multiple problems or just one?
- Was it user-friendly and visually appealing?
- How steep was the learning curve?
- What kind of training and support was available?
- How comprehensive was the integration process?
- What were the ongoing support terms and costs?
- How frequent were updates and what did they include?
- What analytical and reporting capabilities were offered?
- Was a trial available to test the system?
During demonstrations, we paid careful attention to potential ROI. Would the software truly streamline operations? Could it improve productivity enough to justify the investment? How would it impact our daily operations?
Finding Our Solution
After extensive evaluation, 1factory emerged as our clear choice. It stood out by offering solutions for nearly every department:
- The New Product Introduction phase became dramatically more efficient, with auto-ballooning, planning, and documentation generation reducing days of work to hours
- Version control finally gave us clarity over document management
- Digital inspection recording eliminated lost paperwork and illegible notes
- Integrated NCR/CAPA/SCAR capabilities streamlined our quality engineering tasks
- Comprehensive gage control provided the traceability we needed
- Robust analytics gave us the insights for data-driven decisions
The Implementation Journey
Despite the excitement to roll out our new solution immediately, we took a measured approach. The Quality Planning team began using 1factory for all new jobs, gradually phasing out our legacy systems. This allowed us to introduce the software department by department, providing proper training and support along the way.
While many users were excited about the new possibilities, others were hesitant about learning another system. We found that personalized training approaches worked best. Most users took to it immediately, while a few needed repeated training, and a handful - the one's least comfortable with computers - required one-on-one sessions. But eventually, everyone got there and even the most reluctant users grew to love the system.
What happened next was unexpected but gratifying. As word spread about the benefits - faster processing, easier data entry, instant information access - departments not yet using 1factory began asking when they could start. People were actually excited about software.
Lessons Learned
Looking back on our journey, several key insights stand out:
- Take time to thoroughly understand your current problems and future needs
- Involve end-users in the selection process
- Don't rush implementation - a measured approach pays off
- Provide flexible training options to accommodate different learning styles
- Let success stories drive organic adoption
The path to modernizing quality control processes isn't always smooth, but with careful planning and the right solution, it can transform your manufacturing operations. Our journey from paper-based chaos to streamlined digital efficiency wasn't just about implementing new software - it was about changing how we think about quality control in the digital age.
About the Author
Matt Stanley brings over 17 years of hands-on manufacturing and quality control experience to this guide. His journey in manufacturing began on the shop floor as a machinist, where he gained firsthand experience with the challenges of production quality control. After transitioning to a full-time role in quality control, Matt spent two years honing his skills in parts inspection and CMM programming.
His career path led him to a leading aerospace manufacturer, where he advanced through multiple quality-focused roles over 15 years - from Inspector/CMM Programmer to Quality Engineer, then to Quality Planning Team Lead, Quality Manager, and finally Quality Continuous Improvement Project Manager. This progression gave him unique insights into quality management challenges at every organizational level.
Matt's interest in 1factory began in 2021 when members of his manufacturing and quality teams discovered the solution at the Precision Machining Technology Show (PMTS) in Cleveland. This serendipitous encounter would ultimately lead to the transformation detailed in this guide.