Towards a Robust First Article Process
Earlier this week, we met with a prospective customer, and discussed challenges with their first article process. The customer told us that they were going "back-to-the-basics" with First Article Inspections. Nearly 20 years ago, this company eliminated receiving inspections, and parts began to flow directly from the receiving dock into stock and on to the production line. Around the same time, a first article process was instituted, and the company began inspecting each first article that was shipped in.
Since then, business has grown significantly for this customer, with revenues now in excess of $10 billion a year. As business grew, the volume of first articles grew with it. Soon, a few hundred designs required first article inspections each quarter. Obviously, this created a significant resource challenge.
Meanwhile, defective parts were frequently making their way to the manufacturing floor as well as into the spares pipeline, contributing to shipment delays and customer dissatisfaction.
Eventually, people began to question the value of the first article process. Under pressure to cut costs, the company decided to stop inspecting first articles, and switched to a documentation review process instead. Today, suppliers inspect the part, and fill out a first article form. The customer reviews the form for completeness (are all features included in the first article form?), as well as for compliance to specification (is each feature in-spec?).
While costs of first article inspection dropped, the company continues to suffer from a large number of defective parts entering its manufacturing operations and spares pipeline.
So, in an attempt to reduce defective parts entering the supply chain, the customer has now decided to go back to what they described as "the basics" by actually verifying each first article measurement themselves (either in-house, or by witnessing the inspection by the supplier).
Is there any value to a first article inspection?
Our customer has come a full circle, but a critical question remains unanswered: will inspecting first articles actually help drive down the defect rate in on-going production?
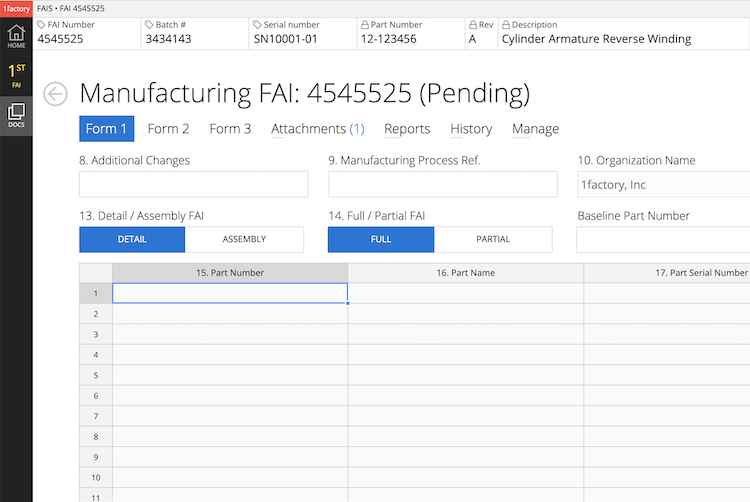
Screenshot: AS9102 First Article Inspection Report in 1factory
A first article review process needs to do more than simply check the first piece. While dimensional, material, packaging, color, and functional testing verifications are obviously important, they represent only part of the value of a first article process.
Here’s an example of what happens when you focus only on the "first piece". A supplier of high-precision medical components received a first-article order for a new component. Along with the first article was an order for 100 units. The supplier made the first 100 units on a 4-axis CNC. Parts were shipped, and were verified and accepted by the buyer.
A few weeks later, the first production order came in. The order was for 30,000 units in lots of 5,000. There was no way the supplier was going to be able to deliver 30,000 units on time with a manual load/unload process on a CNC. So the product was shifted to a Swiss Screw Machine with an automatic loader. Machining steps, fixtures, and tooling were changed on the fly, and parts were produced and shipped. Unfortunately, the new process had not been adequately validated, and the buyer’s incoming inspection found a 6% defect rate, leading to a huge escalation. The supplier nearly lost the entire business over this problem.
The change in manufacturing process had completely invalidated the first article. Even though nothing had changed in the design of the part, a new first article should have been done, given the change in the manufacturing process.
The purpose of a first article process
As the above example shows, a very important, but often-overlooked purpose of the first article process, is to validate that the production process that will be used going forward is capable of producing a good part.
First, we want to make sure that the manufacturing process and quality control plan are completely documented. The quality control plan is an opportunity to communicate critical features and align expectations with the supplier. It’s also what you come back to and reinforce in the event of a problem.
Next, we want to make sure that the first-article is produced using the machinery, fixtures, gages, and sub-supplier processes defined in the manufacturing process and in the quality control plan. By ensuring that the production process for the first article is representative of the on-going production process, you can weed out manufacturability issues that could interrupt on-going production.
And finally, it is important to note that the first article is not a one-time event. It must be repeated in the event of a change in design, manufacturing process, sub-supplier, or even change in packaging. For this you will need a robust bi-directional change communication platform.