Production Part Approval Process (PPAP) - A Guide
01. What is a Production Part Approval Process (PPAP)?
The Production Part Approval Process (PPAP) is a standardized process in manufacturing that ensures a supplier can consistently produce parts meeting all engineering design specifications and quality requirements.
This guide explains the key aspects of PPAP, when it's needed, and how to implement it effectively.
Purpose and Benefits of PPAP
For Suppliers
- Evaluate part manufacturability
- Ensure design documentation completeness
- Identify potential design errors
- Recommend manufacturability improvements
- Establish robust manufacturing processes
- Confirm manufacturing process capability
For Buyers
- Set up reliable supply chains
- Verify supplier understanding of design requirements
- Validate special processing steps
- Ensure consistent functional testing
- Establish supplier's ability to deliver quality parts
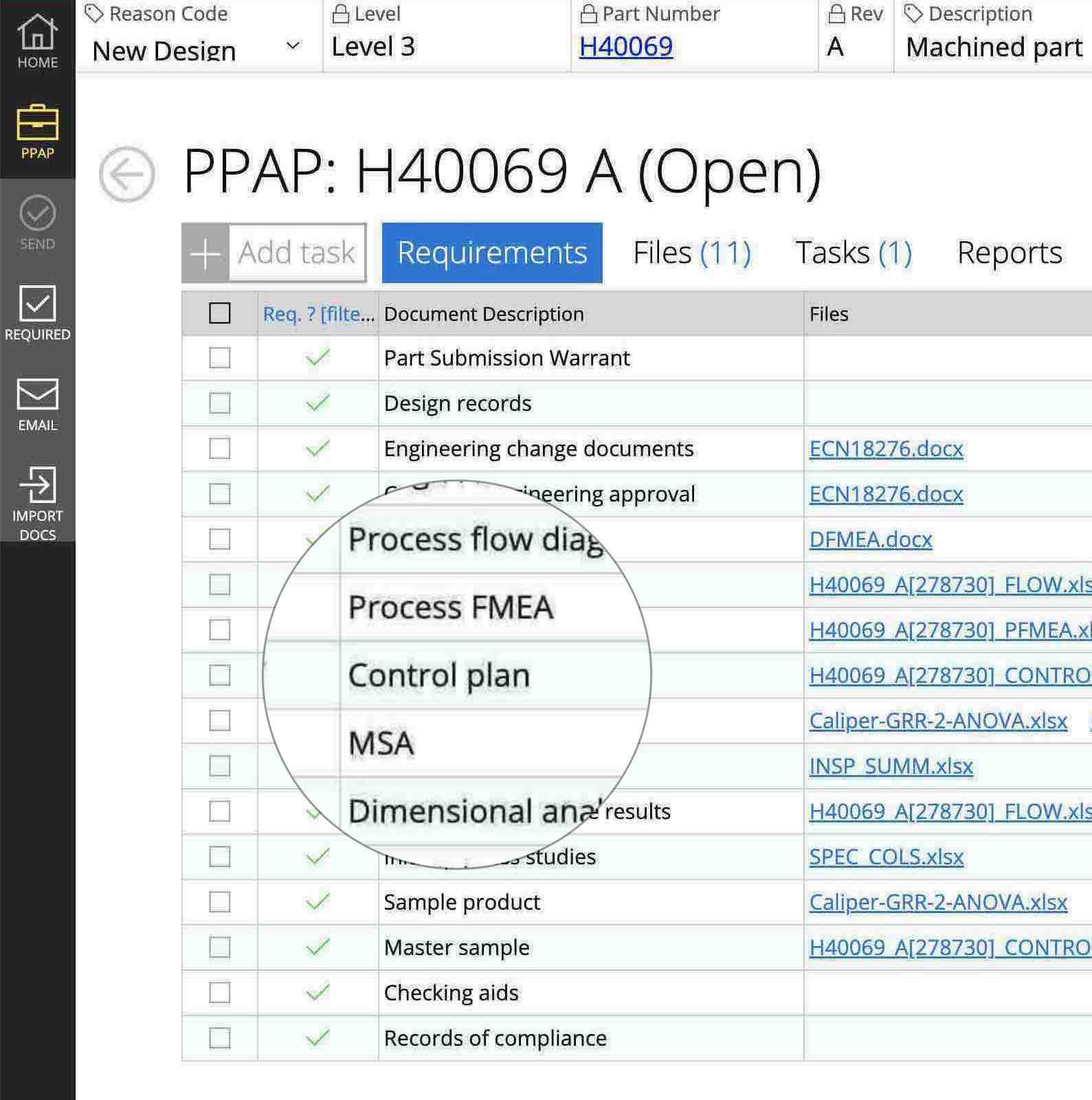
02. When is a PPAP needed?
A PPAP is required first during the new product introduction process and subsequently a delta PPAP is required for any change to the design or manufacturing process.
Once a PPAP is approved, we assume that every subsequent part is built to the same set of design requirements, and is built with the same manufacturing process as defined in the PPAP. Any change in the part's design or in the manufacturing process violates this assumption, and therefore requires a new PPAP.
Here's a partial list of conditions or events that will trigger a new PPAP:
- New Product Introduction
- Design Change (new Part Number or Revision)<.li>
- Manufacturing Process Change
- Vendor Change
- Factory Move
- Resuming Production After a Long Gap
Some of these changes require a complete new PPAP. For example, a change in manufacturing process from 4-axis CNC to a swiss screw lathe, will require a complete new PPAP. A more localized change, to a powder coating process for example, or a change to the packaging of part, may not require a full PPAP. Instead, a delta PPAP may be sufficient.
03. PPAP Levels
The PPAP Levels define the set of documents required for a given part. There are five commonly used levels, but it is common for each company to customize these levels to address their own industry-specific requirements.
Commonly used levels:
Level 1
- Create core PPAP documents
- Submit only Part Submission Warrant (PSW)
- Retain other documents for review upon request
Level 2
- Create core PPAP documents
- Submit PSW, product samples, and selected documents
- Retain remaining documents for review
Level 3
- Submit all core PPAP documents
- Include product samples
- Standard level for most submissions
Level 4
- Submit all core documents and samples
- Include additional customer-requested documentation
- Enhanced verification level
Level 5
- Create all core documents
- Retain samples and supporting data
- Make available for customer review on request
04. Commonly Requested PPAP Elements
There are a number of industry-standard PPAP requirements:
- Design Records
- Engineering Change Documents
- Design Failure Modes, Effects and Analyses (D-FMEA)
- Process Flow Diagram
- Process Failure Modes, Effects and Analyses (P-FMEA)
- Control Plan
- Measurement Systems Analysis (MSA / Gage R&R)
- Dimensional Results (for N parts)
- Run-at-Rate Study
- Raw Material Records
- Lab Results
- Functional Test Records
- Process Capability Study
- Appearance Approval Report
- Part Specification Warrant (PSW)
In addition, customers may provide requirements specific to their business and industry.
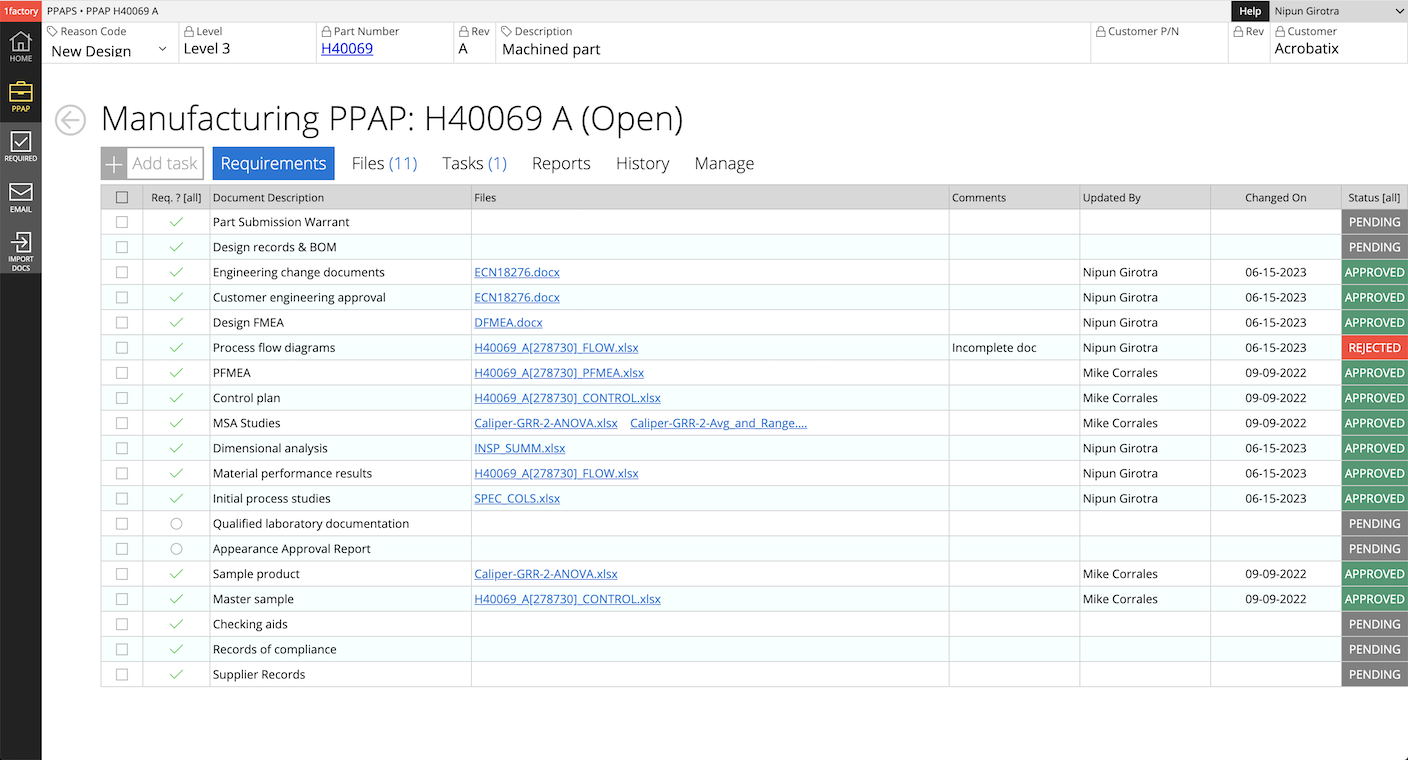
05. The Design Record
What It Is:
Design Records are the complete engineering documentation package that fully defines the product's specifications, including drawings, CAD data, material requirements, and performance specifications. They serve as the master reference for all product requirements.
Why It's Important:
Design Records form the foundation of the entire PPAP process. They provide the baseline against which all manufacturing processes, inspections, and quality controls are developed. Without accurate and complete design records, there's no way to verify if a part meets requirements or if manufacturing processes are capable of producing conforming parts.
Key Elements:
- Complete engineering drawings and specifications
- CAD data when applicable
- Material specifications
- Performance requirements
- Design tolerances and notes
06. The Engineering Change Documents
What It Is:
Engineering Change Documents track all approved modifications to the product design, manufacturing process, or testing requirements. They create a chronological history of how the product has evolved over time.
Why It's Important:
These documents ensure traceability and control of all changes that could affect product quality or performance. They help prevent unauthorized changes and ensure that all stakeholders are aware of and approve modifications before implementation.
Key Elements:
- Documentation of all approved engineering changes
- Change history and implementation dates
- Impact analysis of changes
- Verification of change implementation
07. Design Failure Modes, Effects and Analyses (D-FMEA)
What It Is:
Design FMEA is a systematic analysis tool that identifies potential ways a product might fail to meet requirements, evaluates the risk of each potential failure, and establishes controls to prevent or detect these failures.
Why It's Important:
D-FMEA helps catch potential design issues before they become problems in production. It drives design improvements and helps establish appropriate controls for critical characteristics, ultimately reducing warranty costs and improving customer satisfaction.
Key Elements:
- Systematic analysis of potential design failures
- Risk assessment of design features
- Preventive measures for design risks
- Severity, occurrence, and detection ratings
- Risk Priority Numbers (RPN) calculations
08. Process Flow Diagram
What It Is:
A Process Flow Diagram is a visual representation of the entire manufacturing sequence, showing each step from raw material receipt through final inspection and shipping. It includes all operations, movements, storage, and inspection points.
Why It's Important:
This document provides a clear roadmap of the manufacturing process, ensuring all steps are properly sequenced and no critical operations are missed. It serves as the foundation for developing the Process FMEA and Control Plan.
Key Elements:
- Step-by-step manufacturing sequence
- Inspection points
- Material handling steps
- Decision points and rework loops
- Quality check stations
09. Process Failure Modes, Effects and Analyses (P-FMEA)
What It Is:
Process FMEA analyzes potential failures in the manufacturing process itself. It examines each step in the process flow diagram to identify what could go wrong during manufacturing and establishes controls to prevent or detect these issues.
Why It's Important:
P-FMEA helps prevent manufacturing defects before they occur by identifying and addressing potential process weaknesses. It guides the development of process controls and inspection requirements, reducing scrap and rework while improving quality.
Key Elements:
- Analysis of potential process failures
- Manufacturing risk assessment
- Prevention and detection methods
- Process control strategies
- Risk mitigation plans
10. The Control Plan
What It Is:
A Control Plan is a detailed document that defines how each characteristic of the part will be controlled during production. It specifies what needs to be checked, how it will be checked, how often, and what happens if something is found to be out of specification.
Why It's Important:
The Control Plan ensures consistent quality by standardizing monitoring and control methods. It connects the requirements from the Design Records with actual production controls and serves as the primary quality assurance tool during manufacturing.
Key Elements:
- Detailed monitoring requirements
- Inspection methods and frequency
- Measurement techniques
- Sample sizes and control limits
- Reaction plans for out-of-control conditions
- Documentation requirements

11. Measurement Systems Analysis (MSA / Gage R&R)
What It Is:
MSA evaluates the reliability and accuracy of the measurement systems used to verify product quality. In manufacturing, we need to know if the differences we measure between parts are real or just measurement errors. A Gage R&R study helps us understand where variation comes from by answering two key questions:
- How much variation comes from actual differences between parts? (Part Variation)
- How much variation comes from our measurement system - the combination of the gage and operator?
For a measurement system to be reliable, most variation should come from actual part differences, with only a small fraction coming from the measurement system itself.
Why It's Important:
Without reliable measurements, quality control decisions could be based on bad data. Parts that measure close to specification limits (LSL or USL) are at risk of being incorrectly classified as Pass or Fail if our measurement system isn't reliable. MSA ensures that the tools and methods used to measure part characteristics are capable and consistent, providing confidence in quality decisions.
Key Elements:
- Measurement system capability studies
- Repeatability and reproducibility analysis
- Gage calibration records
- Measurement uncertainty calculations
- Operator training documentation
A Gage R&R study and supporting calibration records are typically required for every critical feature.
Learn more about Measurement Systems Analysis / Gage R&R in our "Guide to Gage R&R".
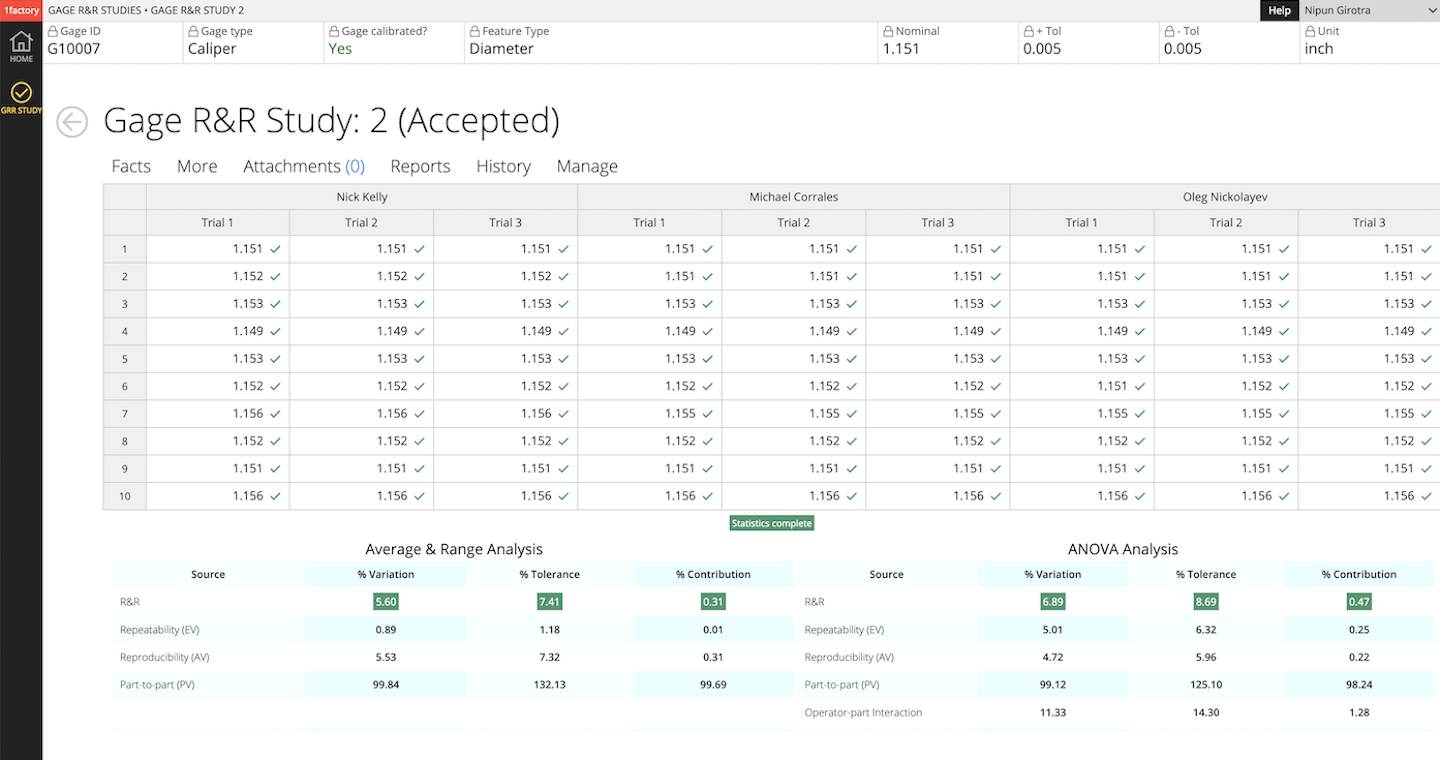
12. The Dimensional Record
What It Is:
Dimensional Results are actual measurements taken from a production sample of parts, typically using various measurement equipment such as calipers, micrometers, CMMs, and other specialized gauges. These results document that all part dimensions meet specifications. Measurements may be Variable (Numeric) or Attribute (Pass/Fail).
Why It's Important:
This verification provides concrete evidence that the manufacturing process can produce parts that meet all dimensional requirements. It serves as the baseline for future production and helps identify potential areas of concern before full production begins.
Key Elements:
- Actual measurements for specified sample size
- Comparison to design specifications
- Statistical analysis of results
- Documentation of measurement methods
- Traceability to measuring equipment
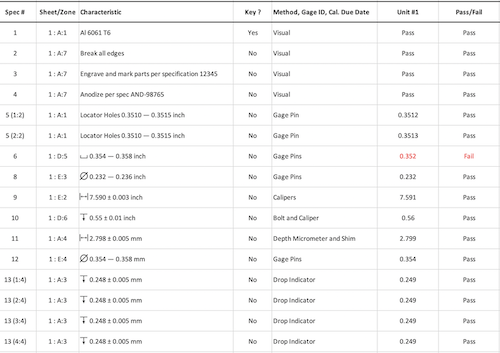
13. Run-at-Rate Study
What It Is:
A Run-at-Rate Study evaluates whether the manufacturing process can produce parts at the required production rate while maintaining quality standards. It involves running the process at full production speed for a specified time period.
Why It's Important:
This study validates that the process can meet both quality and quantity requirements under actual production conditions. It helps identify bottlenecks, capacity constraints, and quality issues that might only appear during sustained production.
Key Elements:
- Production capacity verification
- Cycle time analysis
- Quality achieved during full-speed production
- Process stability assessment
14. The Raw Material Record
What It Is:
Raw Material Records document the composition, properties, and specifications of all materials used in the product. These include material certifications, test reports, and traceability documentation from material suppliers.
The buyer will provide a raw material specification (e.g. AL6061 T6, 301SST etc.) and a reference standard. The supplier, in turn, must provide proof that the raw material used for the first article meets this specification.
This proof is provided in terms of a certificate of conformance (CoC) provided by the mill along with traceability information such as a Heat Lot number. The CoC will typically contain the key elements listed below.
Why It's Important:
Proper materials are fundamental to product quality. These records ensure that the correct materials are used and meet all specifications, which is crucial for product performance, safety, and regulatory compliance.
Key Elements:
- The Mill Name
- Material Grade
- ASTM Standard Number
- Material Form and Dimensions
- Heat Lot Number
- Quantity Covered by the Report
- Actual Chemical Composition
- Mechanical Test Results
- Country of Origin
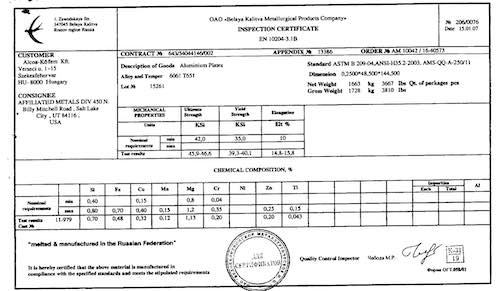
15. Laboratory Results
What It Is:
Laboratory Results include all testing performed to verify material properties, product performance, and compliance with specifications. These may be from internal labs or independent testing facilities.
Why It's Important:Laboratory testing provides objective evidence that the product meets performance requirements and specifications. This is especially critical for characteristics that can't be verified through normal inspection methods.
Key Elements:
- Material testing results
- Performance test data
- Environmental testing results
- Accelerated life testing (e.g. HALT) when applicable
- Third-party lab certifications
16. Functional Test Records
What It Is:
Functional Test Records document how well the product performs its intended function. These tests verify that the product works as designed under various operating conditions.
Why It's Important:
While dimensional measurements ensure the part is built correctly, functional testing verifies that it actually works as intended. This is crucial for ensuring customer satisfaction and product reliability.
Key Elements:
- Performance test results
- Environmental test data
- Durability test results
- Safety test documentation
- Compliance test verification
17. Process Capability Study
What It Is:
A Process Capability Study uses statistical methods to evaluate whether the manufacturing process can consistently produce parts within specification limits. It measures the natural variation in the process against the required tolerances.
Why It's Important:
This study predicts the long-term ability of the process to meet specifications. It helps identify potential quality issues before they occur and guides process improvement efforts.
Key Elements:
- Run Chart and Histogram
- Stability analysis
- Capability indices (Cp, Cpl, Cpu, Cpk)
Learn more about Process Capability in our "Guide to Process Capability".
18. Appearance Approval Report
What It Is:
The Appearance Approval Report documents that aesthetic characteristics meet customer requirements. This includes color, texture, finish, and other visual aspects of the product.
Why It's Important:
For products where appearance is critical, this report ensures that subjective quality characteristics meet customer expectations. It serves as a reference standard for future production.
Key Elements:
- Surface finish evaluation
- Color matching verification
- Texture assessment
- Visual defect analysis
- Customer approval documentation
19. Part Submission Warrant (PSW)
What It Is:
The Part Submission Warrant is the formal declaration by the supplier that all PPAP requirements have been met. It summarizes the entire PPAP submission and requires supplier authorization.
Why It's Important:
This document serves as the supplier's formal confirmation of compliance with all requirements and their commitment to maintain the validated production process. It's often the final step in PPAP approval.
Key Elements:
Declaration of PPAP compliance
Supplier information
Part information and revision level
Submission level
Customer approval status
Speeding-up the PPAP Process
1factory's PPAP & APQP Software automates and speeds-up every element of the PPAP process: Drawing Ballooning, Control Plans, FMEAs, Gage R&Rs, Raw Material Records, Dimensional Records, Initial Process Studies (SPC, Process Capability) and more. Learn More